The Article
KA-RC-1 Ultrasonic Cleaner From Kirmuss Pt.1
15th January 2019

Positioning itself as a midrange product, Paul Rigby exhaustively reviews the Kirmuss KA-RC-1 ultrasonic vinyl record cleaner. This is Part One of a two part review.
Growing in popularity, the ultrasonic record cleaner is becoming an essential part of many vinyl fan’s armoury. I have used every variant of vinyl cleaning known to man (manual and machine-based) and have found ultrasonic technology to be the most effective and efficient out there. I use this type of Record Cleaning Machine (RCM) on a day to day basis.
So what is ultrasonic cleaning, exactly?
The general idea is to dip your vinyl into a bath of distilled water (not low enough to wet the label, of course). That disc is slowly, mechanically rotated.
Built-in, bath-fixed transducers increase pressure and vibration in the water producing millions of rising bubbles that stretch and compress. The frequency of the transducers determine how large the bubbles become. Their structural integrity fails and they collapse…violently. If this happens near vinyl grooves, they will agitate and remove surrounding particles. This is known as cavitation. Any surfactant (a substance to lower water’s surface tension) added to the area attracts further bubbles.
Kirmuss has taken three years to develop the KA-RC-1, focusing on a particular ultrasonic frequency for vinyl cleaning, the correct height to hold the record in the bath, developing an effective surfactant and more.
The first time I saw the KA-RC-1, it was at the North West Audio Show at the Devere Cranage Estate in Cheshire, last Summer. I want to dwell on this occasion a little because it has a bearing on the product, the company itself and this review.
My first view of Kirmuss as a company was its staffer bedecked in a white coat. I had to smile at this. I thought, “Hello, what do we have here, then?” The coat may have been worn to instil confidence but that sort of adornment triggers the opposite from myself. Then I saw the machine, it looked bulky and gawky yet the feature-rich chassis was intriguing, as was the long and involved cleaning process. So I interviewed the company there and then.
INTERVIEW
During the interview, Kirmuss talked a lot of sense and it was generally informative. And yet, there were also issues that got in the way. Apart from the pantomime white coat there was also the self-aggrandising, self-mythologising and self-promotion. I was constantly dragging the interviewee back to the point. I’m sure Kirmuss only wanted to be informative but it also sounded like Kirmuss was revealing big Dan Brown-type secrets previously hidden, warning of terrible dangers and pointing a trembling, damning finger at my record collection while stating that the only chance I ever have of reaching analogue nirvana and quite possibly also surviving to my next birthday was via the use of a KA-RC-1. Basically, the spiel was just too much.
I wasn’t the only person there who felt like he had just faced a guy who was selling a potion off the back of a wagon that was guaranteed to give long life, enhance my attractiveness to the opposite sex and cure my dodgy knee…and all I had to do is pay him some money for the privilege. This market stall-approach to promotion was and is not the norm in the hi-fi industry. And not in a good way. And so my hackles were up and alarm bells rang.
More than that, I felt that the company desperately needed (and still needs) a professional PR and marketing team to act as a conduit and buffer between it and the public/press. Sometimes companies need help when trying to convey a message to the press and public. Kirmuss needs such help.
That thought would continue and intensify, as you will see below. Nevertheless, I continued to show interest.
Later, because I also write for the UK news-stand, national magazine HiFi World, I was given the opportunity to review the thing. I liked it too (and Kirmuss has wasted no time in plastering my comments on its website). The problem with print magazine reviews is the limited deadline time you have to fully investigate the product. Which is why, even if you’ve read that print magazine review, you should really ignore it and press the reset button in your memories. Since then, I’ve given this machine many weeks of further research and discovered many new areas that you should be aware of, as well as undertaking additional independent research and interviews, all of which are listed below and need digesting.
This is a big review but I don’t apologise for that. This product is important because it’s the first ultrasonic RCM to seriously look to bridge the gap between the DIY cheapo machines and the high end, super expensive models. It also has a host of options and potential that needs investigation with many additional, potentially contentious features that require careful thought.
MANUAL & WEBSITE
The options I mentioned are all described in the accompanying 8-sided, A5 manual, replete with illustrations.
The problem with this? The manual is a mess. It’s poorly planned and laid out, it’s confusing, grammar is a secondary concern and there is no sense of guiding the user through a graduated process of education.
Yes, the early parts of the manual have a semblance of order but that quickly degenerates into a confusing mixture of vinyl and record format history plus How To… instructions spread over the manual and various paper supplements.
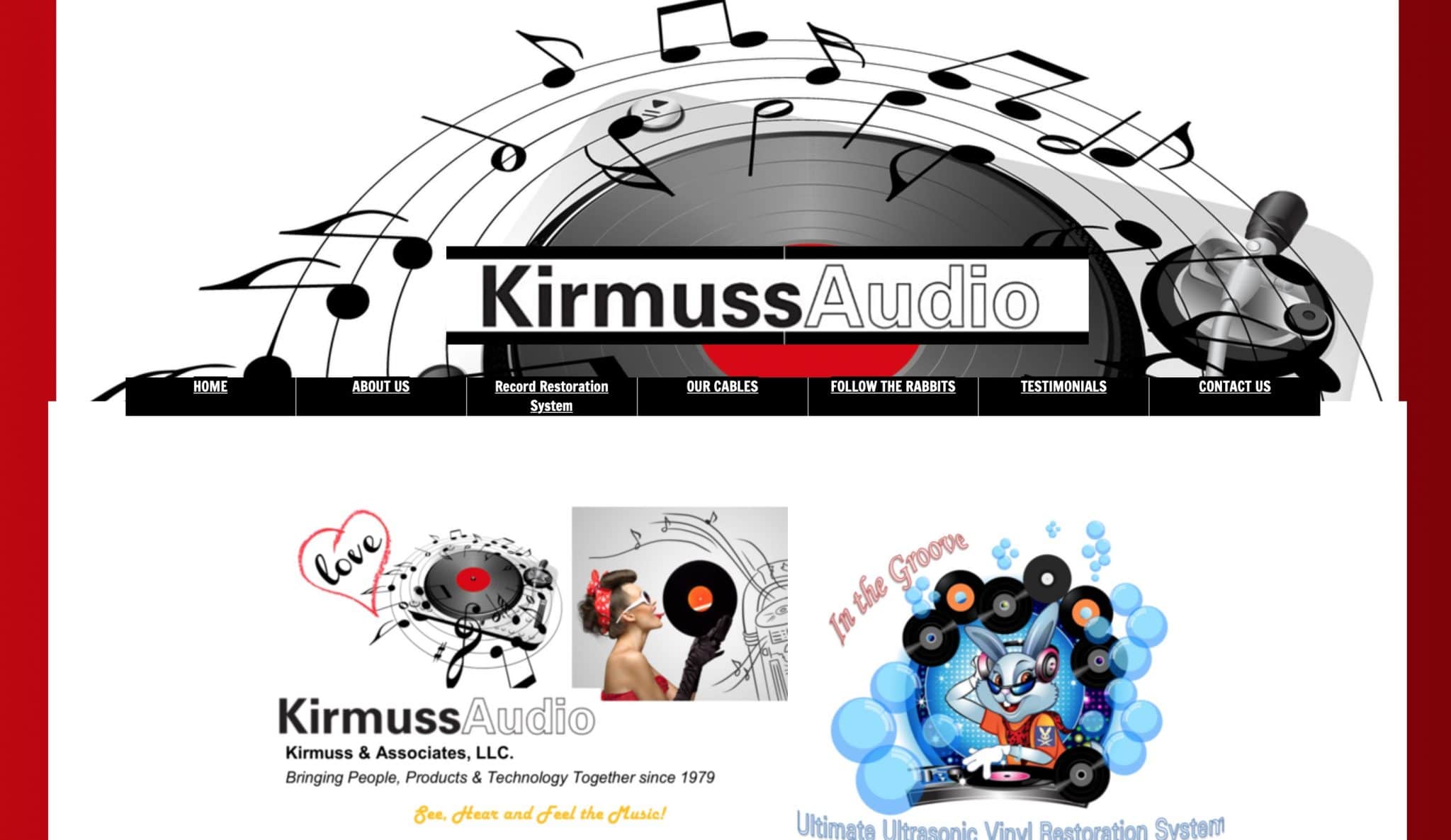
The website (www.kirmussaudio.com) retains this haphazard style with a lack of design thought, spelling mistakes and grammatical issues plus the insertion of massive blocks of confusing white space positioned in the centre of each page.

Hence, the overall impression from the public demo routine, the manual and the website is not a good one. They give the impression that you’ve just walked into amateur night. Again, there’s a need for professional PR and marketing help here.
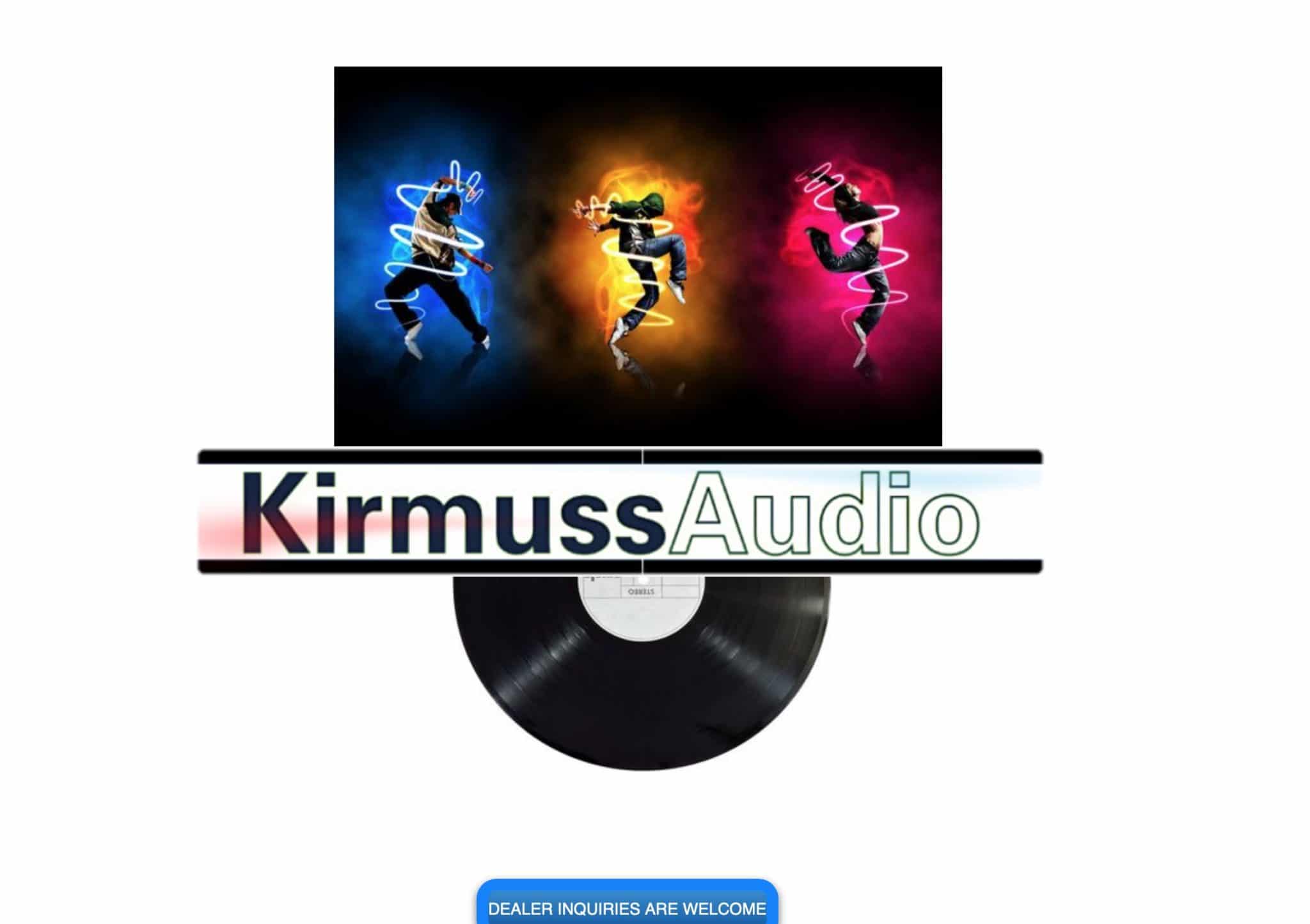
And the reason I’m telling you all of this? Because, faced with the above (and you might have been at some point), it’s easy to be discouraged. Stick with this product, though. It’s worth investing time and effort into the KA-RC-1. It might not be the magical force that Kirmuss infers but there is a solid product on offer here.
DESIGN
As you can see from the accompanying images, the chassis is a low-and-long design that, unfortunately, demands a fair amount of footprint. Many other ultrasonic cleaners user a vertical design that minimises the amount of space.
Another downside? The KA-RC-1 chassis also looks like a toy. There’s even an ill-advised cartoon graphic stuck on the side to emphasise the Toys R Us feel. One that I would remove 30 seconds after removing the chassis from the box, to be frank. When I first unpacked the KA-RC-1, I actually looked for the Nintendo logo. The KA-RC-1 chassis is even bedecked in that classic Nintendo gray shade.
Kirmuss won’t volunteer the information but this chassis is not their own, it’s bought in. Other, non-hi-fi, third party companies also use the same chassis as a basic ultrasonic cleaner. When I asked about the bath, Kirmuss revealed that it had approached the manufacturer and modified the original design to suit its own purposes. Hence, Kirmuss has invested in its own bespoke, vinyl-centric top plate section and has removed the temperature/heating options. The chassis normally arrives with its own internal basket to hold items for cleaning. That has been removed but can be bought back from Kirmuss if you want the KA-RC-1 to clean other, non-vinyl items in its chassis.
Of course, not developing its own chassis is how Kirmuss has been able to maintain a relatively low price for its RCM.
I do like the built-in handles on the chassis of the KA-RC-1. Other ultrasonic cleaners forget that you need to move cleaners around on a semi-regular basis during cleaning and refilling. I always feel that I’m about to drop my Audio Desk RCM, for example. Without built-in handles, accidents threaten. Kirmuss has the right idea here.
The bath system uses six litres of distilled water as the basis of its cleaning process, which is a lot. Competing systems (like the Audio Desk) often use a lot less – four litres is common – so you’re going to be spending a little more money on distilled water with the Kirmuss. This is not such a big deal, though because distilled water is not, in the grand scheme of things, that expensive.
The rear of the KA-RC-1 chassis features a power cable and rocker power switch. The right side is where the outlet pipe is situated, allowing the exit of bath water during cleaning, with the help of a supplied add-on flexi-tube. The front sees a sturdy valve switch to open/close that pipe. I tested both and they work with no issues.
The top-right features the cleaning controls and readout. The latter keeps a track of the countdown during a selected process, underneath the clock is a set of lights indicating the process underway as well as a colour-coded temperature gauge. Under that are buttons to change the cleaning time (78s, for example, only need two minutes of ultrasonic cleaning whereas vinyl requires the default five minutes).
Beneath those are two further buttons. The first is to set the ultrasonic cleaning in motion. The second is a degass (aka Pulse) button to remove latent bubbles within the distilled water. Reportedly, de-gassing makes the water bath a more unified body of water, enhancing cleaning efficiency. Without it, says Kirmuss, the cavitation process spends half its time removing the bubbles in the water, instead of concentrating on cleaning your vinyl.
After filling the KA-RC-1 bath with distilled water, I was asked to degass the water twice, a process that took just over 90 seconds each. Kirmuss recommends that you do this when you first fill the RCM but that you should also repeat after several disc cleans. The feeling being that the water will have been agitated enough to produce extraneous bubbles within the body of the bath liquid content.
RECORD ASSEMBLY
I loved the whole KA-RC-1 Record Assembly Unit concept. The modular nature of this area is quite brilliant and this one area justifies the larger chassis footprint. For a number of reasons. Firstly, it provides a range of record format options from the off, as a default. No costly extra adaptors are required for 7” or 10”/78 records. Both of these formats are included as part of the package, as are two 12” size discs: four in all. This is a welcome decision by Kirmuss to give the user this quality of choice from the basic package.
More than that, this Assembly is operated using an almost clockwork array of belts and cogs. It looks fixable by replaceable parts. It appears to be something that, if it broke down, you could actually repair. A concept that is rare nowadays.
More than that, the Assembly is a drop in solution. That is, the top assembly loosely fits onto the top of the bath. A short electrical lead connects to the side of the chassis to provide power to the gearing.
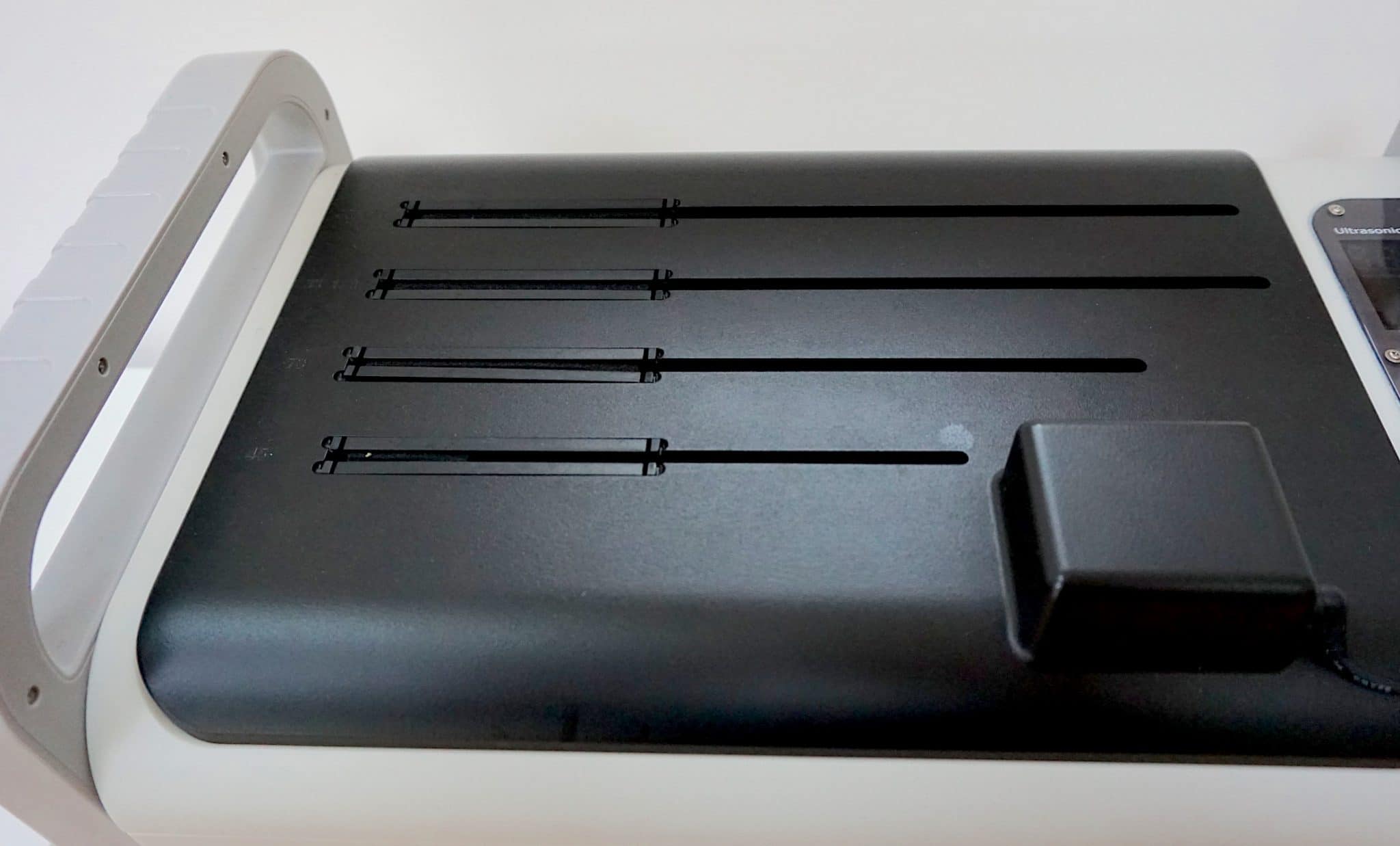
What I want Kirmuss to do now is work on a range of Assembly choices, to provide various format options. Hence I’d like to see Assemblies that you can buy as additional accessories. In my own mind’s eye, they could cater for: four 12” discs, four 7” discs, four 10” discs and an Assembly with half and half (two 12” discs and two 7” discs). And then I want Kirmuss to produce a rack for them all, holding a maximum of four Assemblies so that I can then pull the Assembly I need for that day from my rack, drop it into the KA-RC-1 and off I go.
Apparently Kirmuss is working on a new drop-in unit with an alternative slot arrangement but whether Kirmuss will actually have the cash and wherewithal to fulfil all of these record cleaning fantasies of mine is another question. It also depends on user demand.
That sense of potential flexibility is very exciting for someone who not only has thousands of vinyl discs in his collection but has a range of formats sizes to address.
CAVITATION
There are effectively two KA-RC-1 stages to cleaning a record. Firstly, there’s the active ultrasonic cavitation process. Then the record is removed and a sort of After Care process is begun. I’ll describe the cleaning process first. After Care – which is more significant to this review than you might think – will be dealt in Part Two.
The standard KA-RC-1 cleaning process, according to the manual, goes something like this.
You insert your record into one of the KA-RC-1 size-compatible slots. You can either change the cleaning time or run with the five minute default. The process begins after the top mounted On/Off switch is pressed twice.
After a single clean, for new records, Kirmuss wants you to remove it and play the thing there and then.
For used records, Kirmuss advises that you place the record on a 7” felt mat (supplied, I talk more about this mat in the After Care section in Part Two) and pump three sprays of Kirmuss’ ‘surfactant’ (also supplied) around the record. This stuff apparently helps to soften the muck and grime but its principle job is to remove surface tension from the distilled water and cavitation bubbles, allowing the bubbles to get closer to the grooves to remove groove muck. In effect, it makes the water wetter.
I want to emphasise the importance of a surfactant to this review. This is a first. It is the first time that any commercial company has promoted such a step in vinyl record cleaning. General cleaning liquids are applied to the record surface, yes, but don’t count because they are in effect all-in-one cleaning solutions and home-made recipes are excluded here too. I’m talking about a commercial, officially promoted system. This is a first. Other ultrasonic cleaners talk about surfactant use but they often include it as part of the bath liquid. Not as a separate application applied directly to the vinyl surface itself to then be washed off during the secondary cleaning process.
The surfactant is sprayed around each side of the record which is then worked into the grooves by a densely bristled brush (again, more in Part Two). Back into the bath the record goes for a further five minutes of ultrasonics to remove more gunk and wash off that surfactant. Then out comes the record for the After Care section.
Let’s pause right here and backtrack.
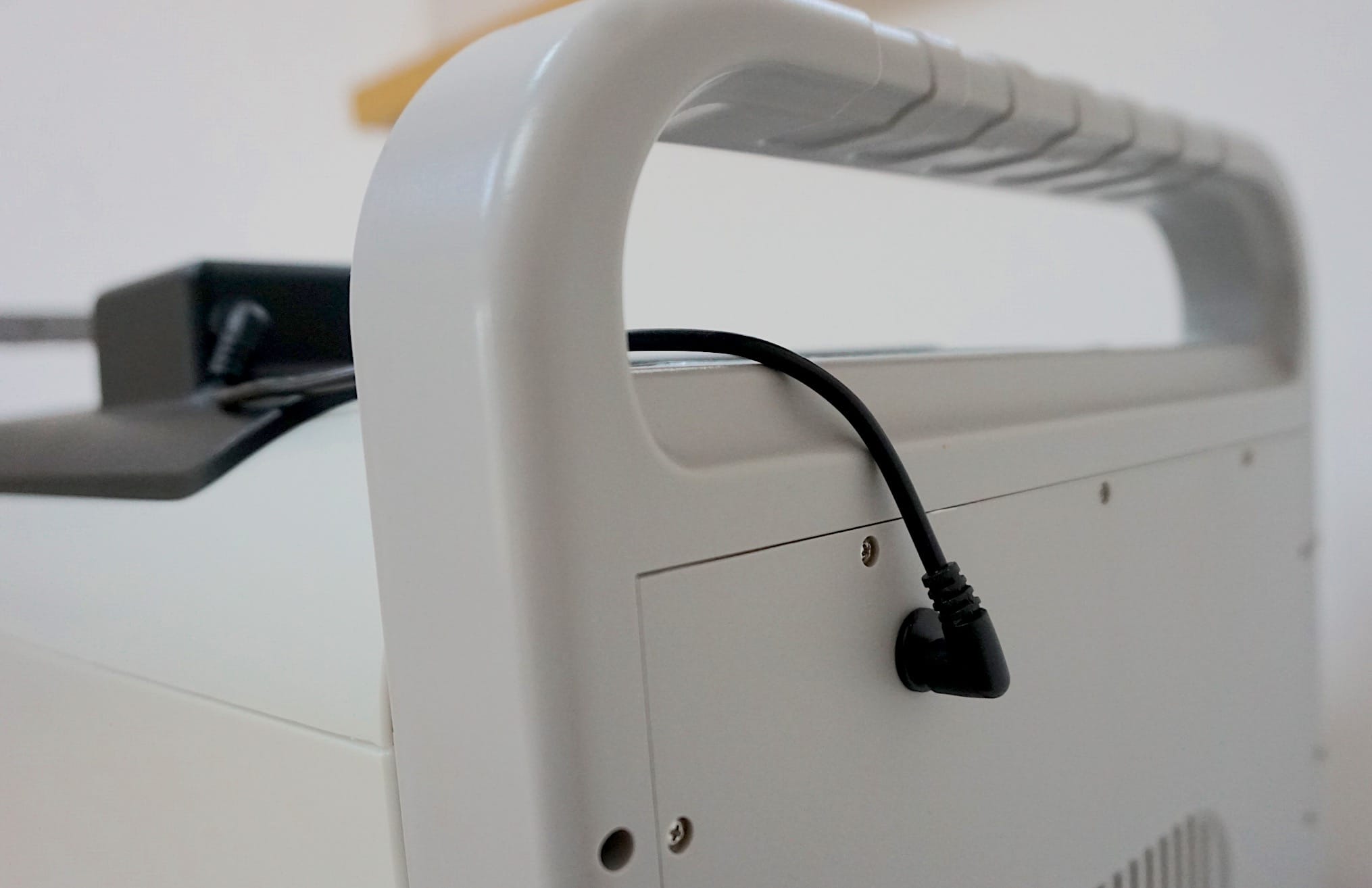
Firstly, if Kirmuss is recommending a surfactant at all, why shouldn’t you be using it with a new record as well as old, used records? After all, the surfactant is supposed to enhance cleaning efficiency, isn’t it? Hence, I recommend the use of surfactant on new records too.
As for that surfactant, what actually is it? Kirmuss, in its manual, describes the liquid as 1% propane-½-diol or Propylene Glycol, as it’s more commonly known. It’s used in the eco-variant of anti-freeze. Don’t panic, though, it’s the stuff which stops anti-freeze actually freezing and is non-aggressive. Propylene Glycol is even used in skin care products, in vaping, foods such as ice cream and it’s also in fake fog you might see in the theatre. Glycol isn’t a surfactant, though. It’s there to, in effect, keep the surfactant in place and stop the actual surfactant pooling on the vinyl surface. When Kirmuss mention the surfactant in the manual and suggest that it is merely distilled water and Glycol, that is a half truth. The actual surfactant ingredient is hidden from view. Kirmuss won’t talk about it. You can tell it’s there because this stuff has a perfume and it bubbles up in use. Glycol is greasy and has no smell. I asked Kirmuss on three occasions to reveal the full contents of the supplied surfactant liquid but it was reluctant to do so. Even when I promised to keep my mouth shut about their surfactant secrets. When pushed, it did reveal a rather confusing and murky chemical/brand name but refused to supply further information or links. I wanted to know more because of this…
WARNING
The Propylene Glycol is rated as safe in any documents you might read on the Internet. Potential hazards are few and far between and there’s no long lasting issues that I could find within the documents I found. That said, I had a reaction because of that unknown part of the liquid, the perfumed surfactant I mentioned above.
What happened was this. In use, when sprayed at the vinyl surface, a small amount of the spray kicked back and flew upwards from the vinyl surface. Looking closely, you could actually see this happening. I then unintentionally breathed the stuff in, it irritated my throat and I flew into a coughing fit. I had to reach for water to stop coughing. This occurred on four or five occasions, immediately after spraying. I did this to make absolutely sure that there was no other possible reason for the reaction (the things I do for you, eh?) The surfactant was used on older and, I hasten to add, brand new records.
I reported this to Kirmuss and owner Charles Kirmuss replied, “The splash back could have been…something coming off of the record as fungus.” Then he hurriedly quoted information relating to how safe his surfactant liquid was – even though I have no idea where the information came from, had no opportunity to double check it and didn’t know what liquid it referred to. Kirmuss’ assumptions may have had grounds if my treated records were all old and had been badly stored but mine were not. As I say, some were even brand new, so fungus infection was doubtful in the extreme. Kirmuss’ scientifically enquiring mind also didn’t think to ask any questions of myself. To save him the trouble, I can tell you that I can react badly to strong perfumes and I guess that was the cause of my reaction. Nothing more. I hope.
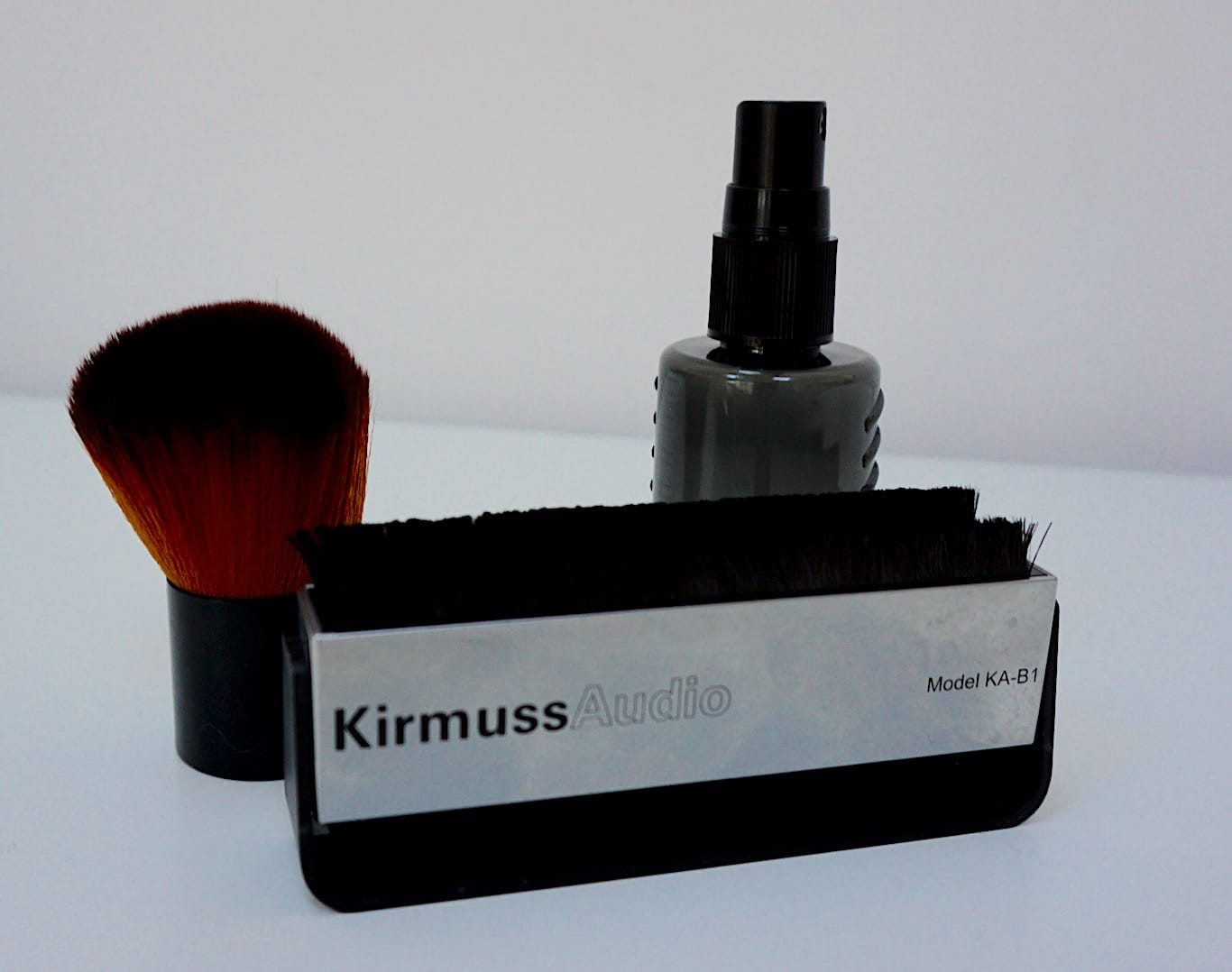
Again, I know that a PR and marketing team would have handled this situation better, would have been more thorough, less dismissive and more supportive.
I trust that this is the only issue in terms of health and I assume that, even then, only some people with sensitive throats will be affected in this way. That said, I’d rather not be breathing this stuff in at all and I was. As I say, I could see it lifting off the vinyl surface. It might not do me any bad but it certainly won’t do me any good, either. The day after my coughing fit, I had a slightly sore throat. Nothing worse than that, though.
So, what to do? Forget the KA-RC-1? No, there’s no need to take such drastic steps. As I say, any spray hitting vinyl will rebound upwards towards your face. If you want to continue with the Kirmuss-supplied liquid (or if you spray any surfactant of any type onto any vinyl surface), I’d recommend buying a pipette, eye dropper-type bottle from Amazon with a relatively high capacity bottle (click HERE to see more). This will stop the issue of spray entering the air, retains my good health (and yours too) and, an additional benefit, will be more precise in terms of application so it won’t accidentally spray all over your precious record label.
THE USE OF ALCOHOL
Then we get to the bath of distilled water. There’s something else included within the water itself. Kirmuss recommends the use of Isopropyl alcohol. This is not sprayed onto the vinyl, as I say, but added to the actual bath of distilled water. Hence, your vinyl is cleaned with distilled water, cavitation and alcohol. You need to buy the alcohol yourself. It’s not supplied. Kirmuss recommend a bottle of 70% alcohol. This liquid is sometimes labelled as Rubbing Alcohol and arrives in two flavours: pure and ‘tainted’. The latter includes impurities for safety reasons, added to make it taste pretty bad. Some Rubbing Alcohol products are pure, though and that’s what I used in the review. Others are literally labelled as 70% alcohol. The other 30% volume is distilled water. You could, of course, use less of the 100% Isopropyl alcohol variant too.
When preparing the bath of liquid for the KA-RC-1, you add 40ml of the 70% solution to the bath of distilled water which amounts to 0.43% total volume. A very low figure indeed.
The addition of alcohol and its recommendation by Kirmuss will be of major concern to some. It was to me, I have to admit, even if only 0.43% was being added. To this point, I have had a zero tolerance of the stuff. In the past, I’ve found it to be nasty and aggressive. It can ruin a vinyl disc.
I have tested an LP to destruction with 100% proof Isopropyl alcohol. In those tests, the first couple of cleans produced a brilliantly clear and open suite of sonics but subsequent cleans produced an increasingly edgy and harsh sound, brittle and bright in tone. After a while, the LP became unplayable, such were the sonic extremes that the alcohol took the sound. The reason? Melting vinyl and groove damage. I’ll address that subject in more detail below.
Suffice to say, I avoided Isopropyl alcohol from that point. I know plenty of people who use it now and swear by it and use various liquid recipes containing it. Often 25% or 20% volume is a common figure in many user’s recipes. I was nervous, though, because I had no facts or figures as to exactly when alcohol caused damage. What was the boundary, over which damage to vinyl occurred? When did alcohol change, transferring from a friendly groove-cleaning product to a damaging, ruinous acidic destructor? Where was the line to be crossed? Was it more than 25%, How about 40%? Maybe it was 15%? Who knows? No-one I ever talked to could tell me for sure. Everyone had an opinion. But no-one actually knew.
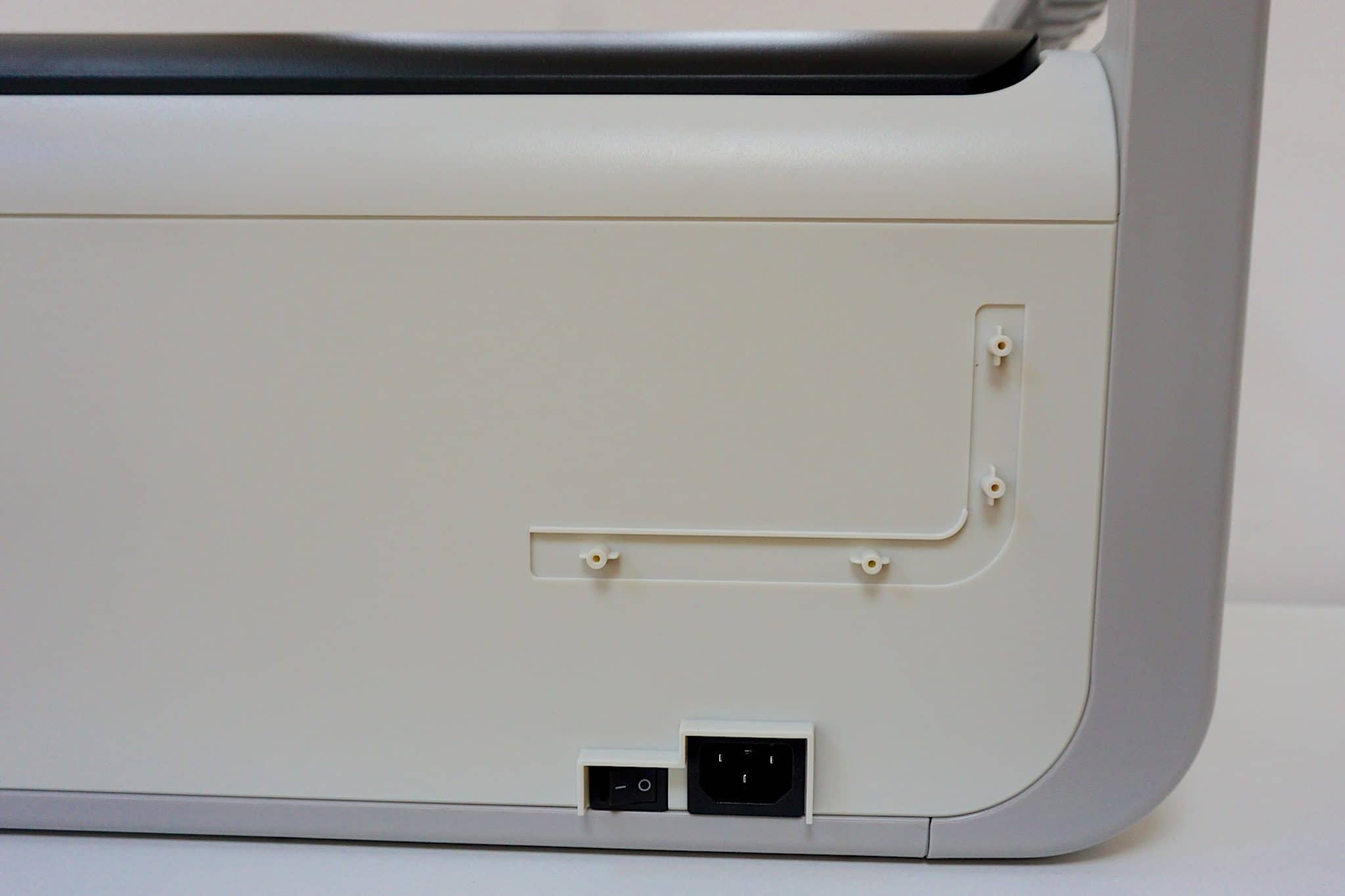
Because alcohol is so contentious as a cleaning ingredient and because the liquid is so much at the core of the KA-RC-1, I felt that I had to learn more about it. How could I truly recommend the KA-RC-1 if I could not trust a key part of its cleaning process?
So I undertook lengthy independent research to find out which was spread over a period of months. I reached out to the vinyl industry because, if anyone would know the answers then they would, right?
NEW RESEARCH
I approached five separate sectors of the vinyl industry. I first talked to a UK company, Transcom, that supplies acetate discs to Abbey Road. These discs are made from a soft acetate to test a master before committing to a full pressing. I talked to a Canadian-based chemist, a lady whose name I’ll keep to myself to retain her personal privacy, who also works on a regular basis with Abbey Road and knows vinyl. Next, I talked to Vinyl Factory, a UK vinyl pressing plant and the guy who runs the place. Based in the UK, this is a factory that actually makes vinyl records. Finally, I talked to the two largest producers of vinyl pellets in the UK, one was Dugdales the other wished to remain anonymous (it’s a nervous and competitive world, the vinyl pellet business). I’m talking about the raw vinyl. The core material that is supplied to the record pressing plant. Bags of these pellets are supplied to the vinyl pressing plant for processing.
Now, surely, if these guys didn’t know the answer, then no-one would.
I initially asked these experts about alcohol but learned a lot more than I bargained for – all of it valuable and fascinating and of use to audiophiles. I’ll share some of this information with you now (Not all, I’m wary at the final size of this increasingly large review!) and hope to share more, for those who might be interested, later in a separate feature.
The most important conclusion from talking to all of these industry experts is that no-one, I repeat not one person I talked to, knew how alcohol affected vinyl. Not in all encompassing and definitive terms, at any rate. Yes, they told me that Isopropyl alcohol was an issue when used neat. I knew that already but no-one knew when Isopropyl alcohol actually became a danger to vinyl. No-one could tell me at what stage or at what point or at what strength Isopropyl alcohol actually attacked vinyl or if repeated use of safe levels was a problem over time. There are, I was told, no figures. None at all. Yes, everyone had a personal opinion and the conversation quickly degraded into conjecture but nothing official was offered.
To say that I was surprised at this was an understatement. Then I found out why. The reason is down to the vinyl itself. You may think that vinyl is vinyl is vinyl. PVC, eh? No. In fact, far from it. Vinyl records are not made from a single substance. The vinyl in your collection is created from a recipe of chemicals. Only one of those is PVC. There’s between four and 10 elements to any one vinyl recipe.
One contact I talked to had many recipes, ready to go at any one time, “We have around six difference black record formulations we make depending on the state of the [pressing] machines but that can increase if the presser wants something ‘a little softer’, for example.” The “state of the machines” refers to age and wear and tear and if the pressing machines vary in pressure and the like. So that’s at least six (maybe more) different types of vinyl recipe from this one company here and today. But there’s more, my contact’s company has changed the recipe of its vinyl pellets over time.
One of the supposed devastating effects that Isopropyl alcohol has on a vinyl record is to distort the plasticiser with it. The bit the helps the grooves retain their form. Everyone I’ve ever talked to in the hi-fi industry believes that plasticiser is and always has been part of a vinyl record. Now I find that it’s just not so, at least not exclusively, “There is no plasticiser added in our formulations,” said my contact, “other companies might add them but we stay away from them as they distort the record if the balance isn’t right and depending on what it is, the surface finish would be hazy and not crisp and glossy.”
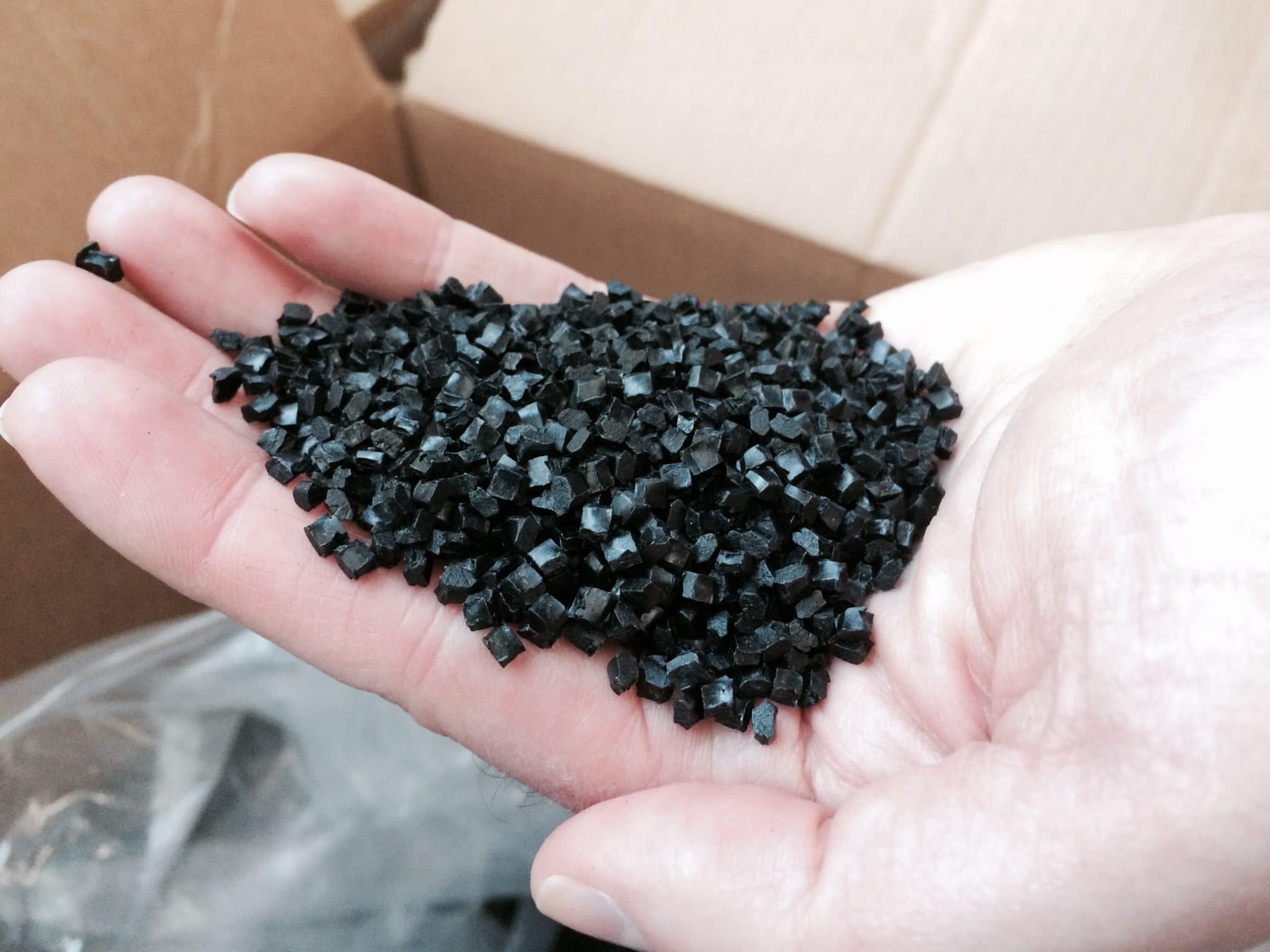
Other chemicals have come and gone too. This adds to the variations in the vinyl recipe. If one company requires six vinyl recipes at any one time then, as above, replaces the plasticiser to create another new recipe (so, that’s six new recipes available on a daily basis), then changes more chemicals (another six variants multiplied by the changes) and keeps doing that over the decades, imagine how many different types of vinyl there are on the market from that one supplier alone? And if you have a different combinations of chemicals making up vinyl disc, it makes sense that alcohol will react differently to each, yes?
There’s more than one company out there making vinyl pellets to create vinyl discs, though. And it’s a highly competitive business. Each company lives and dies by its own bespoke recipe, “…every compounding company will have their own formulations and ingredients, there is no set formulation,” said my contact.
If every company has its own secret formula, how many companies are there in the world creating raw vinyl? My contact said, “I would say, including us, there is around 40 to 50. Could be wrong but Asia have a load and the US have loads as well.” And then going back into history? What about those companies who don’t even exist any more?
Just how many variations are there exactly? No-one knows. It’s an impossible figure to consider. What is entirely possible is that there are hundreds, more like thousands of different types of vinyl out there. You might play 20 vinyl records from your collection and it’s possible that every single one is constructed from completely different vinyl recipes. Or not. Who knows? Because of that, each vinyl disc, theoretically, will react differently to cleaning with alcohol.
So what to do? I decided to put my fear of alcohol to one side and complete a sound test with and without alcohol.
78s
Before I get to that, a word about alcohol and 78s. Kirmuss recommend that you clean 78s in its bath containing 0.43% alcohol. Most 78 users are told that alcohol should never touch a 78 disc. Kirmuss says that the 78 discs will not be damaged because the cleaning cycle is ‘only’ two minutes long and the discs are not exposed for long in the tiny amount of alcohol contained in the water bath. I didn’t have a chance to test this because of limited time, I’m afraid but you have been warned.
SOUND TEST 1
I began the first KA-RC-1 sound test tests with a Richie Havens original release. The LP, Something Else Again and a track called From The Prison. The track possessed a continual stream of noise that sat underneath the vocals.
I undertook the sound tests, initially, by the Kirmuss book but included no alcohol as part of the bath of distilled water. So I firstly inserted the vinyl into the KA-RC-1 to soften up the muck and dirt in the grooves, ran through a single, five minute, ultrasonic cavitation cleaning process, took out the LP, applied the spray-on surfactant to the LP (to soften up the muck some more) and cleaned it off with another cavitation clean.
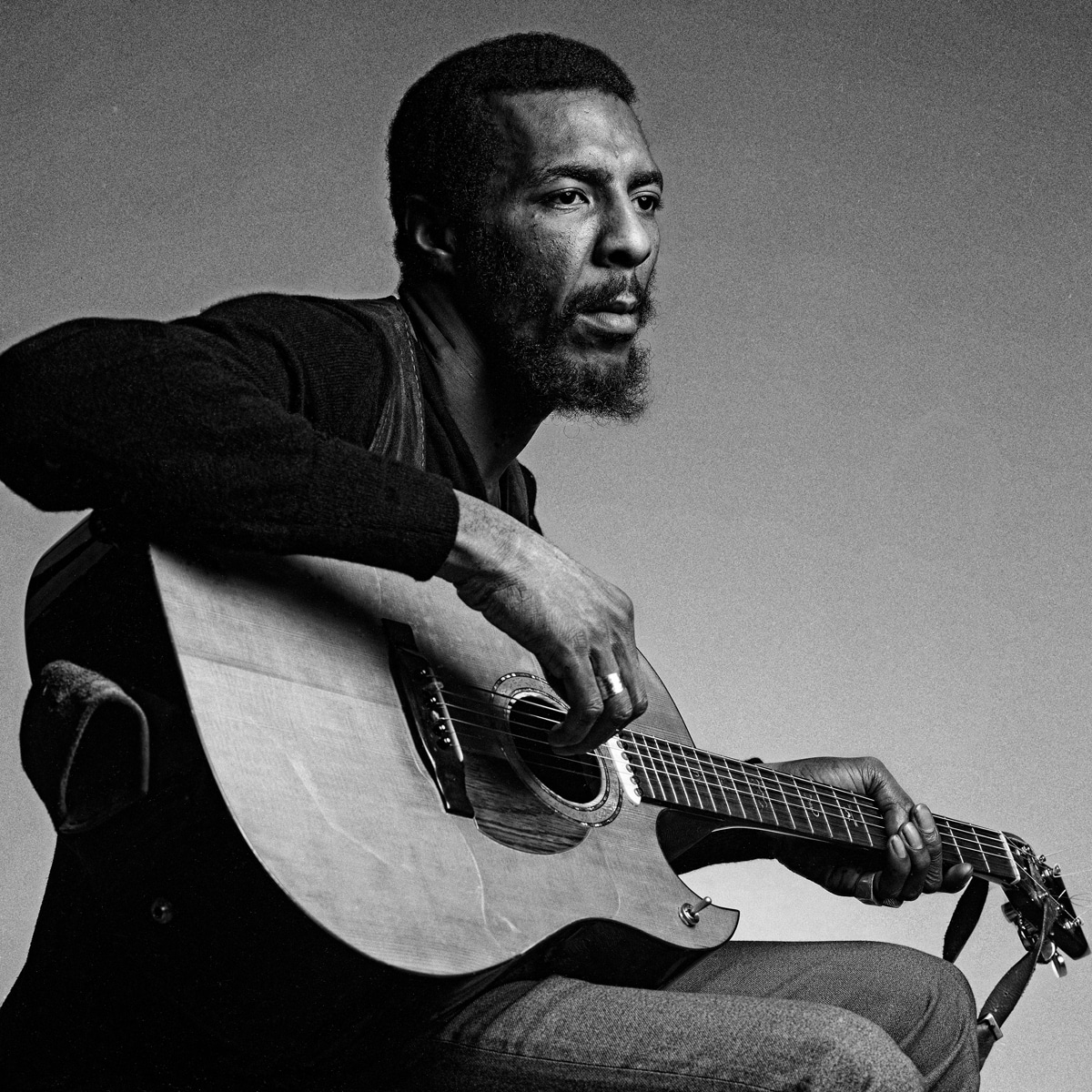
Sonically, I noticed a dramatic reduction in noise. Some noise could still be heard but the overall effect was much improved with sonics also benefitting from being smoother, less edgy and with an informative midrange.
I decided to give the same record an additional surfactant spray and another ultrasonic/cavitation application, again without alcohol as part of the bath contents. The noise reduced still further while sound quality improved again. Clarity improved while extra air and space was heard across the soundstage.
I did notice a mucky build up on my stylus tip. So I tried a third time. I sprayed more surfactant, cleaned that off with another cavitation cycle and played the record. It was this third application that I realised that I’d hit a bit of a wall and no further sonic improvements were occurring.
At this point I added the alcohol to the water, degassed the KA-RC-1 liquid bath again and repeated the cleaning process. More reduction in noise occurred. What remained was very low level, mostly heard between tracks and at the very beginning of the LP. This could easily have been age and vinyl wear.
What really hit me, though, was the sonics. The effect was, how can I put it, less, “Oh that was nice.” And rather more, “Wow!” The minor levels of alcohol are supposed to act as a “grease remover” and that sense of a veil being lifted from right across the frequency range was certainly heard here. Focus, precision and clarity were all enhanced as was a slight increase in gain. Haven’s voice was enhanced in terms of the texture and gravel-like nature of his crescendos while his acoustic guitar was powerful and expressive during his powerful strumming routines.
I did notice a tiny deposit on the stylus tip so maybe the record could have done with one last clean (see the After Care section in Part Two for more on this). I decided to leave that, having satisfied myself of the enhanced sonic qualities.
Instead, at this point, I took the record out of the KA-RC-1 and ‘cleaned’ the same record in my Audio Desk ultrasonic cleaner. The latter featured bespoke Audio Desk liquid within. No alcohol was present in the Audio Desk RCM.
I then played that same Havens’ cleaned record on my reference system and I have to say that, compared to the KA-RC-1, a thin veil had now newly appeared over the music once more. The sound quality was still excellent, lots of detail and so on – this wasn’t a disaster I was hearing by any means. So, let’s not get carried away. That said, there was a dulling, a muting of the top end and a lack of excitement around the vocal delivery. String plucks lacked that organic tonality that I was hearing before. The KA-RC-1 naturalism had largely gone or, at least, had been softened and restrained. Almost as if a thin layer of something had covered the grooves.
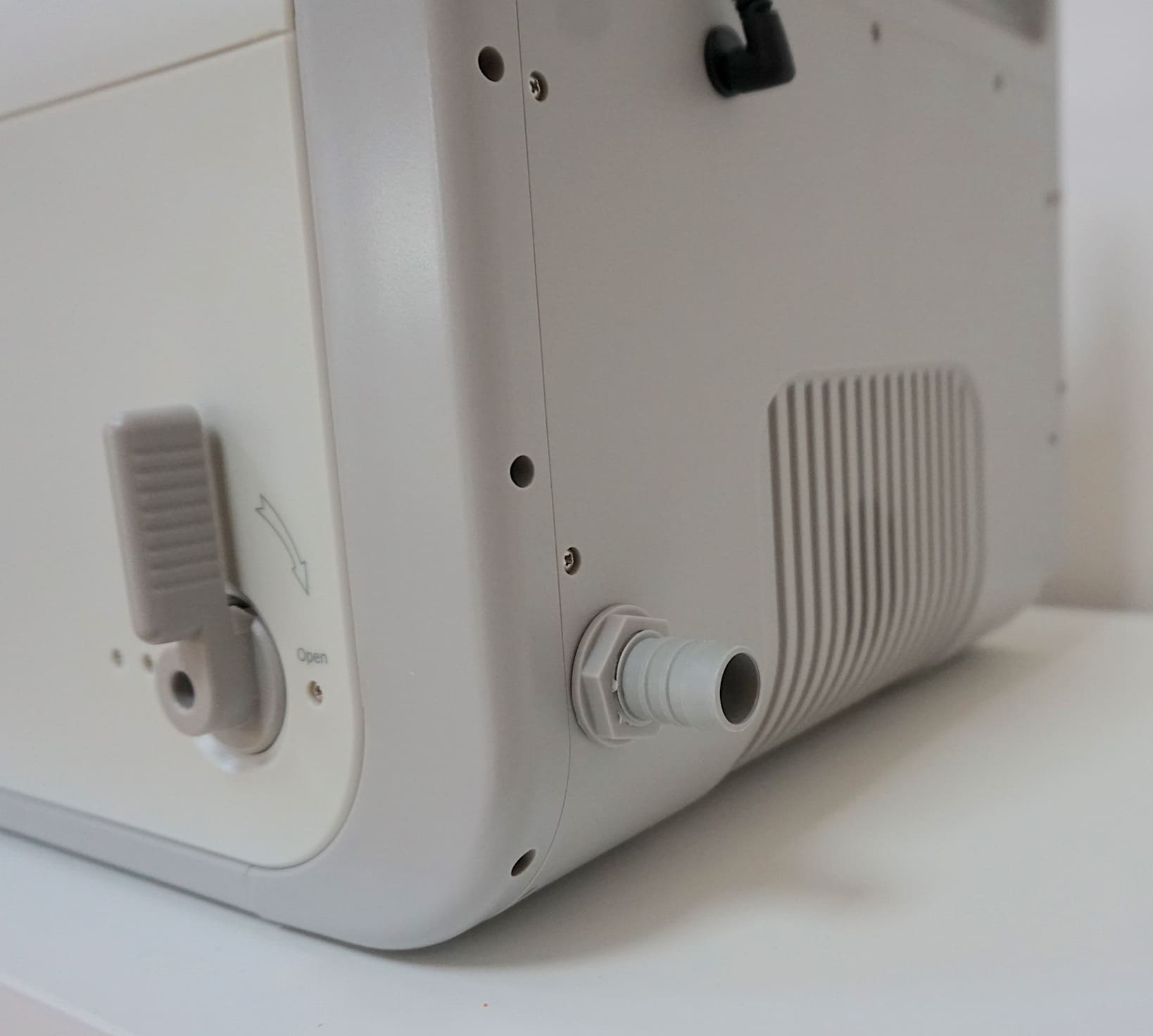
I then took the record out of the Audio Desk and cleaned that same record once more with the KA-RC-1 RCM and the passion come back, so did the dynamic reach, the mids opened up allowing space and air within the soundstage once more, tonality was enhanced, the reverb ‘ring’ off the back of the strummed guitar strings was more evident now and the vocal was far more expressive…even the gain increased.
The revelation was absolute. The shock or rather aftershocks of this test were unquestionable.
Yet there was a single variable that was proven to be responsible for this sonic change. Alcohol. At least alcohol enhanced by the ultrasonic action – and I think the latter is very important here. Remember, only a tiny portion of alcohol was used but this one factor (in conjunction with the ultrasonic action) was key to the change in sonics. Up to the addition of the alcohol, I felt that the performance of the KA-RC-1 and the Audiodesk were roughly on par in terms of sound. That is, sound quality was very good indeed in terms of sonics and the removal of noise, pops and clicks. These physical obstructions had been reduced by both machines to a similar level.
That, in itself, was an intriguing find because the Kirmuss was achieving roughly the same anti-noise performance for around half the price.
Nevertheless, it was the the addition of the alcohol (plus ultrasonics) that was giving me the addition of the sonic lift, removing that dulling veil across the entire soundstage. The alcohol was the important part of the recipe that increased sound quality.
At this point, I’ll end Part One of this test of the KA-RC-1 RCM. Please don’t draw too many conclusions from this one Sound Test – there’s more to come and the story changes. I hope to see you for PART TWO which includes the After Care section, more direct tests with the Audio Desk RCM plus a few suggested tweaks to hone the performance of the Kirmuss (and the Audio Desk) and that final rating.
[Don’t forget to check out my Facebook Group, The Audiophile Man: Hi-Fi & Music here: www.facebook.com/groups/theaudiophileman for exclusive postings, exclusive editorial and more!]
REFERENCE
Origin Live Sovereign turntable
Origin Live Enterprise 12″ arm
Van Den Hul Crimson XGW Stradivarius Cartridge
Icon PS3 phono amplifier
Aesthetix Calypso pre-amp
Icon Audio MB845 Mk.II monoblock amplifiers
Quad ESL-57 speakers with One Thing upgrade
Tellurium Q Silver Diamond cables
Blue Horizon Professional Rack System
Harmonic Resolution Systems Noise Reduction Components
Fantastic article, thank you for your research. When can we expect part 2? I’d like to read it before continuing to use my KA-RC-1.
Very kind of you to say so, Shawn. Working on Pt.2 right now 🙂
That was a lot of work. Thank you.
True! And no problem 🙂
Thank you very much enjoyed immensely and lots of hard work looking forward to,part 2
And thank you for your kind words Neale – Part Two is now up and ready to read 🙂
I would think, also comparing Clearaudio’s Double Matrix Sonic Cleaning Maching, as being part of this series of cleaning machines will give the ‘buyer’ a better understanding of all three machines. In addition, will you be comparing the ‘newset’ 2019 Audio Desk model? Thx. Bg. 1/27/19
Hi Bernard – thanks for the suggestions. I hope to be reviewing more ultrasonics in the future.
An absolutely brilliant article that was thorough. It was very helpful.
Jag – Singapore
Thanks for your kind comments 🙂
Cant that you enough for the article. I almost bought a KA-RC-1 and not sure what to do at this point. I may just stick with this spin clean unit even if I am killing brushes almost monthly for the amount of records that I clean.
No problem, Joe – if you thought about the Kirmuss, like the idea of ultrasonic technology and the Kirmuss is where your budget is at then by all means grab one. It’s a decent cleaner. The core tech is ok. It’s just that I have issues with the company selling it and their advice. So, if you’re still up for it, buy it and then by all means come back and talk to me, ask any questions you may have and I’ll offer any help and guidance you need.
Thanks for the uber-extensive review! You did so much work on this, it is quite amazing….)
Very kind of you to say, Daren – thank you.
This article is un readable. As soon as you get to the first graphic the page widens, hiding half the text, so I was not able to read this article.
I’ve never had that complaint before Terry and I’ve just checked here and now on a desktop and phone and it looks fine. Might I suggest trying a different device and/or browser?