The Article
KA-RC-1 ULTRASONIC FROM KIRMUSS PT.2
17th January 2019
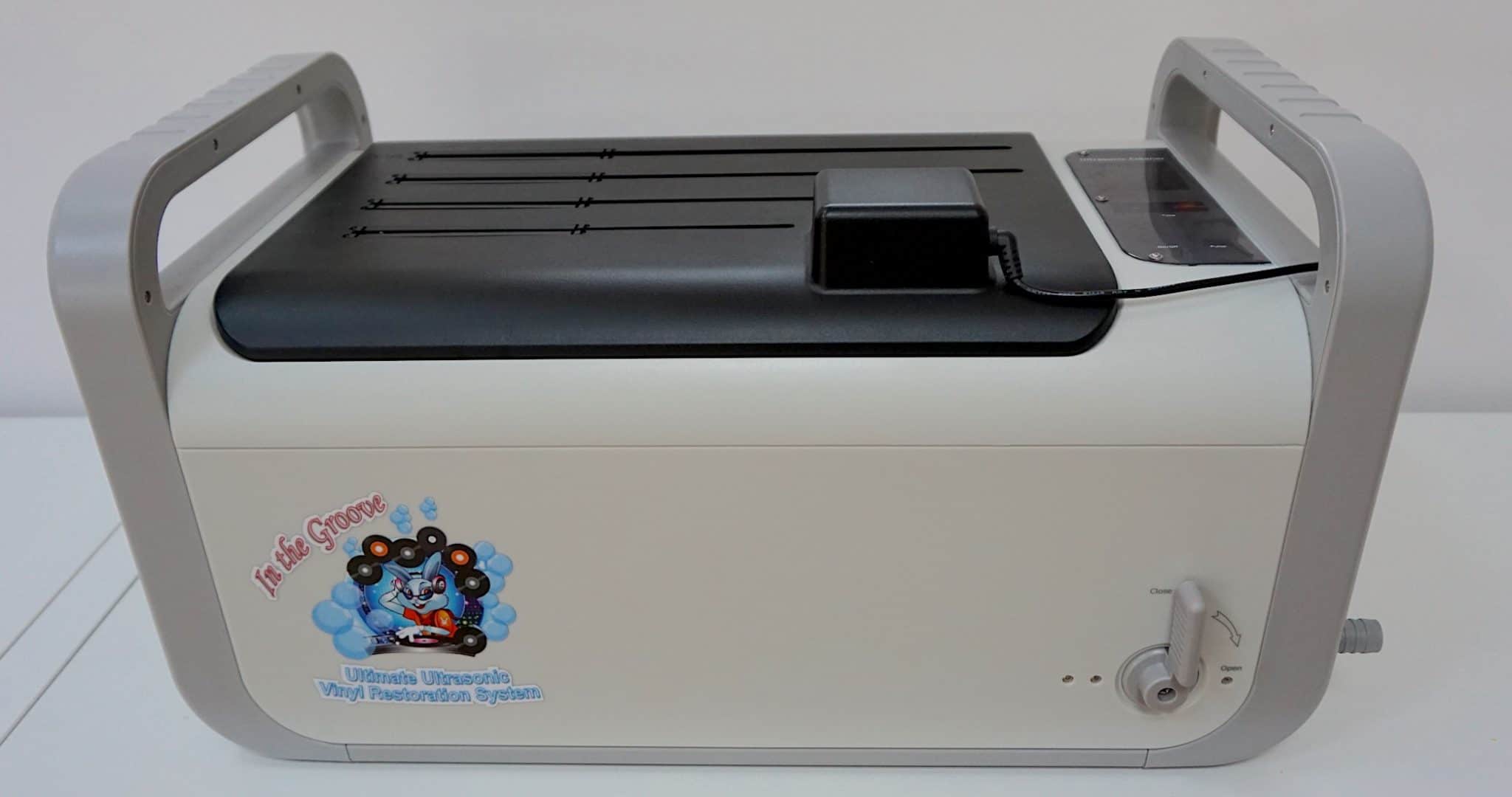
Positioning itself as a midrange product, Paul Rigby exhaustively reviews the Kirmuss KA-RC-1 ultrasonic vinyl record cleaner. This is Part Two of a two part review.
To repeat, this is the second of a two part review on the Kirmuss KA-RC-1 ultrasonic vinyl record cleaner. If you have yet to read the first part then I would strongly advise you to do that now by clicking HERE. Otherwise, you may be a tad confused by the following.
One of the issues with the KA-RC-1 cleaning cycle as a whole is the length of time that’s required to attend to each and every record. Kirmuss might add, “Well, if a job’s worth doing, it’s worth doing well.” And that the time taken is worth the final result.
I wondered about this.
A major slice of time is taken up with Kirmuss’ After Care system. When you finally take the record out of the record cleaning machine and that record has completed its ultrasonic cleaning cycle, you would think that the cleaning process would be over at that point. Not so. In fact, Kirmuss has plans for you and your record. There’s further cleaning steps to be completed before Kirmuss will let you go.
Before I begin, allow me to describe the After Care toolkit. You are suppled with a small mat, upon which you’re supposed to place the record while performing the After Care. There’s a couple of small microfibre cloths, the type you might receive free with a new pair of glasses. There’s a Kabuki brush (a stubby, dense bristled brush commonly used by ladies for make-up purposes) that is used to both apply surfactant and, later, a ‘rinse’ of distilled water. You’re also given a combo carbon fibre brush/felt sponge on a flip-over swivel axle. To use the desired brush or sponge, you rotate the brush. A thick cloth bedecked with pictures of bunny rabbits <sigh> is also supplied which can be used to help in drying your hands and cleaning the Kabuki brush from time to time. A bottle of blue stylus cleaning liquid is also supplied (I would recommend ignoring it and using a sticky pad system, such as the DS Audio ST-50 or one of several other specialist items currently on sale).
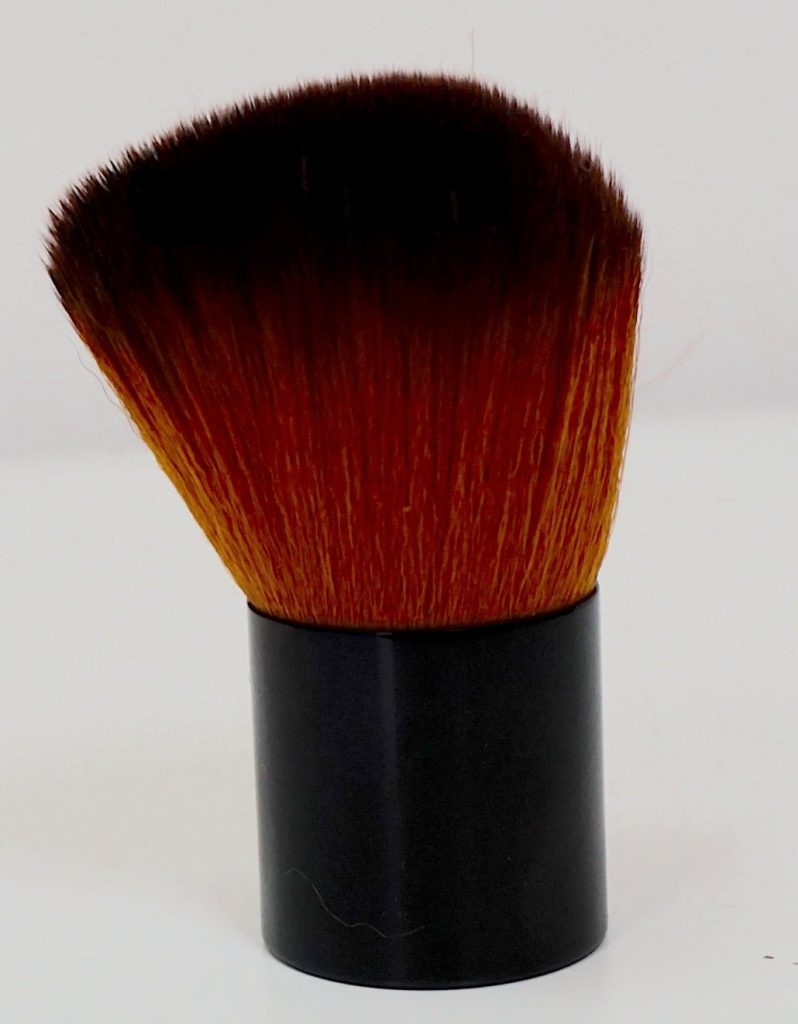
For the After Care section, you are asked to place the record on the miniature mat (felt side uppermost). You spray your record with distilled water (which you must buy – I bought a small empty hand spray bottle from the local chemist to do this bit). The distilled water is then worked into the grooves to, as Kirmuss says, “rinse” them by the Kabuki brush. That water is then dried and mopped up with the microfibre cloth. Then the sponge side of your combo brush is run around the record’s surface to lift excess water. After that, you add a touch of surfactant to the brush. Only a tiny amount is added. You do this by spraying into the air and then pushing the brush into the cloud which coats the tips with a small amount of the liquid. The brush is then run around the record. The reason for this, says Kirmuss, is to prevent static electricity build up. After that, you then run the carbon brush side of your combo brush around the record.
Of course, that’s a single side of vinyl record application. You’ll then need to flip the record over and repeat the entire process again on Side B. Even typing this process is exhausting. Never mind doing it.
Nevertheless, I had issues with most of this, I’m afraid
Firstly? Your work mat, the little felt mat that you’re supposed to place your vinyl disc upon to do all of this After Care work? It’s too large. There’s a risk too of re-contamination of the vinyl grooves from the felt mat. The solution? Either measure a circle diameter with a compass and trim or find an alternative. I’m still looking. Does anyone out there with Kirmuss experience have any ideas?
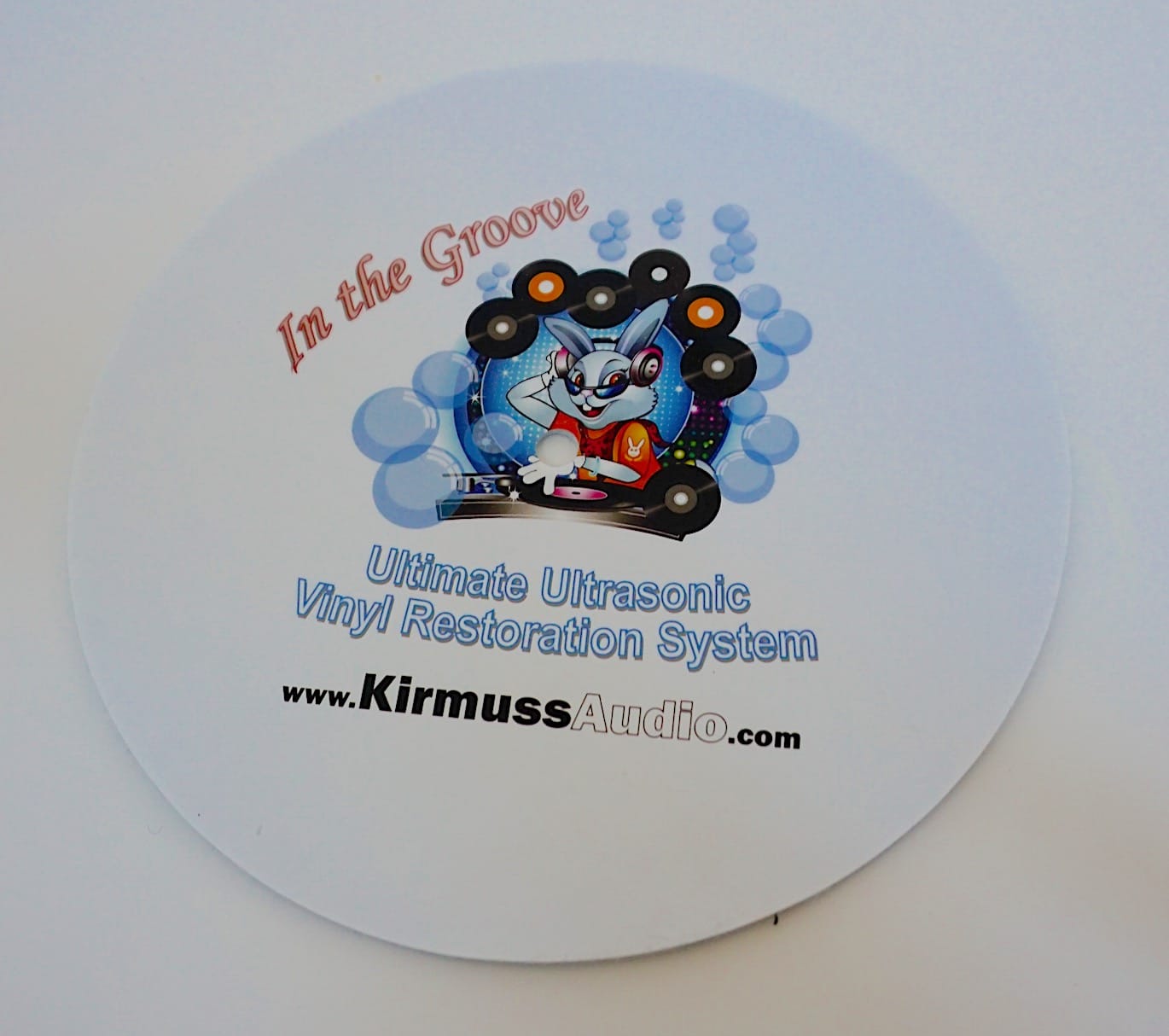
Next? The use of the microfibre cloths and the sponge side of the 2-in-1 brush may soak up excess water but you do find that you physically press on the grooves to do this. Isn’t there a threat, therefore, that any fragments of dirt hanging onto the grooves for grim death may then be pushed back into grooves, recontaminating them? Aren’t all of these actions counter-productive, to the cleaning process, therefore?
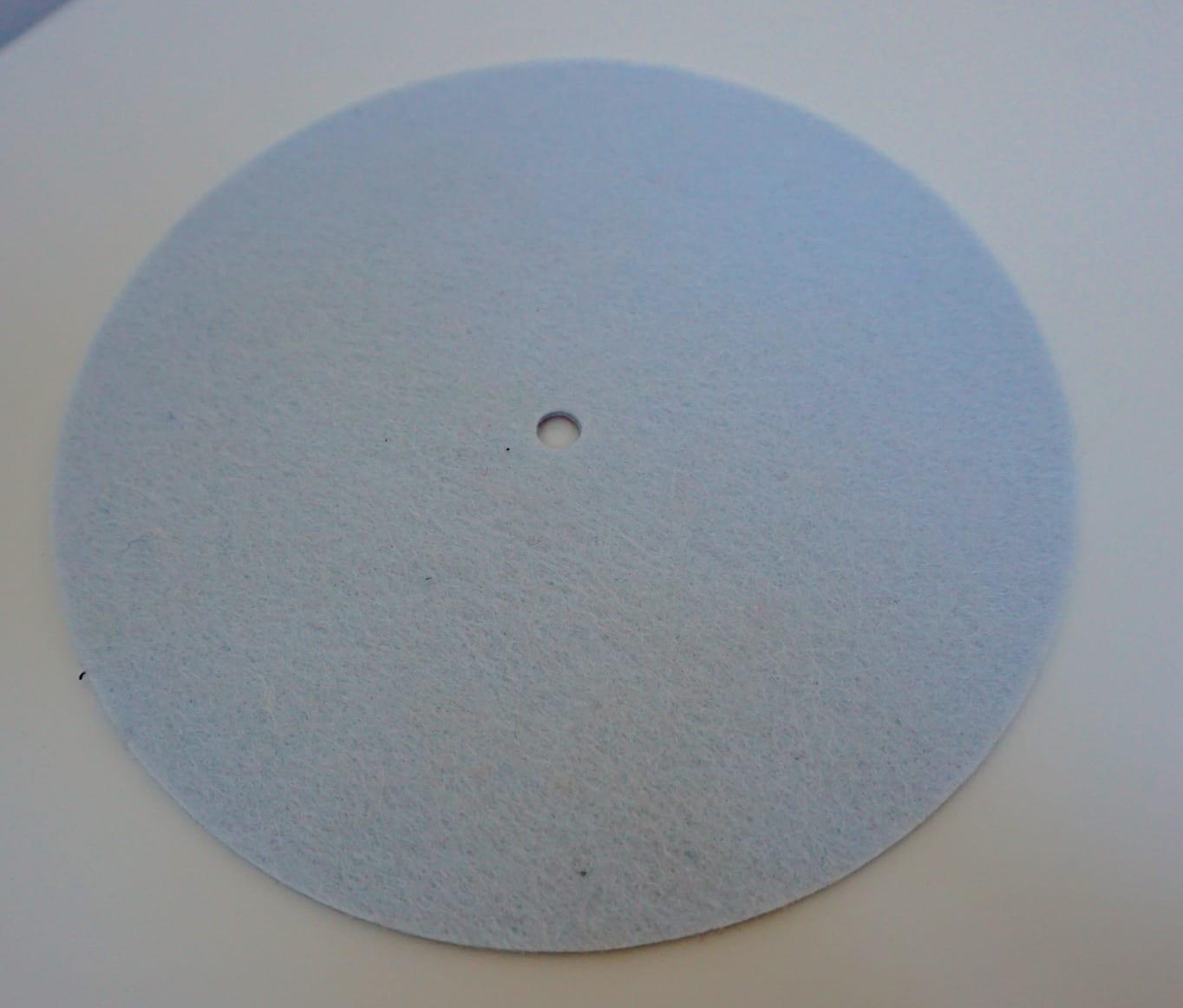
Then there is the recommended “rinse”. Initially, I wondered why you needed to rinse the record in more distilled water. Haven’t we just cleaned the disc? Hasn’t the surfactant supposedly melted away and fallen into the water? Hasn’t the alcohol now evaporated from the disc upon emerging from the KA-RC-1? What exactly are we trying to rinse here? I have to also ask, how does dousing the record in water and then mopping it up with a lint-free cloth constitute a rinse?
I’ll talk more of this later.
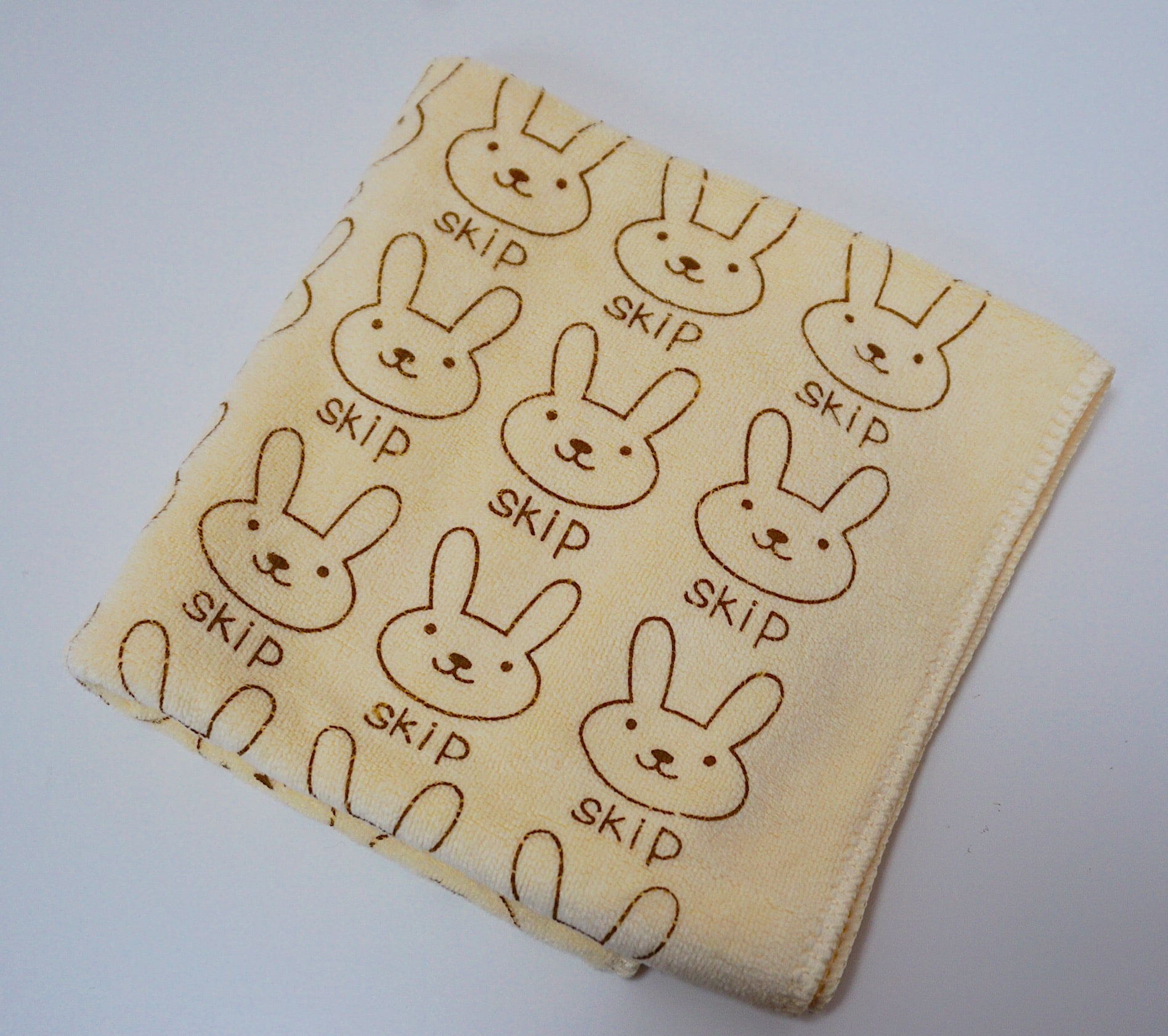
As for the application of small levels of surfactant to the vinyl surface once more for anti-static purposes, haven’t we just been using the KA-RC-1 to try to remove as much gunge, muck, dirty and dried crud? Why then are we once more adding surfactant to the grooves? The same stuff that apparently can only be removed from the grooves if dissolved fully in water and ultrasonic bubbles? Even if the general idea is to prevent static, aren’t you also adding a new substance to the grooves? Doesn’t that partly defeat the entire reason for using the KA-RC-1 in the first place?
If static prevention is the aim, why not promote the use of a Zerostat or the anti-static Furutech brush or Furutech DeStat? After use, none of these devices leave a residue on the groove surface.
SOUND TESTS 2
To see if the After Care process affected sound in any way, I cleaned my old Ritchie Havens record in the KA-RC-1. I had already cleaned this LP via the Kirmuss 10+ times so that the record was a clean as it was ever going to get.
I then did two things. I cleaned the record again, applied the full After Care treatment and listened via my reference hi-fi. I then cleaned the record once more, ignored the After Care and then did nothing more than air dry the record in a rack, used the carbon fibre brush to dislodge and final bits of rubbish and then played the record again.
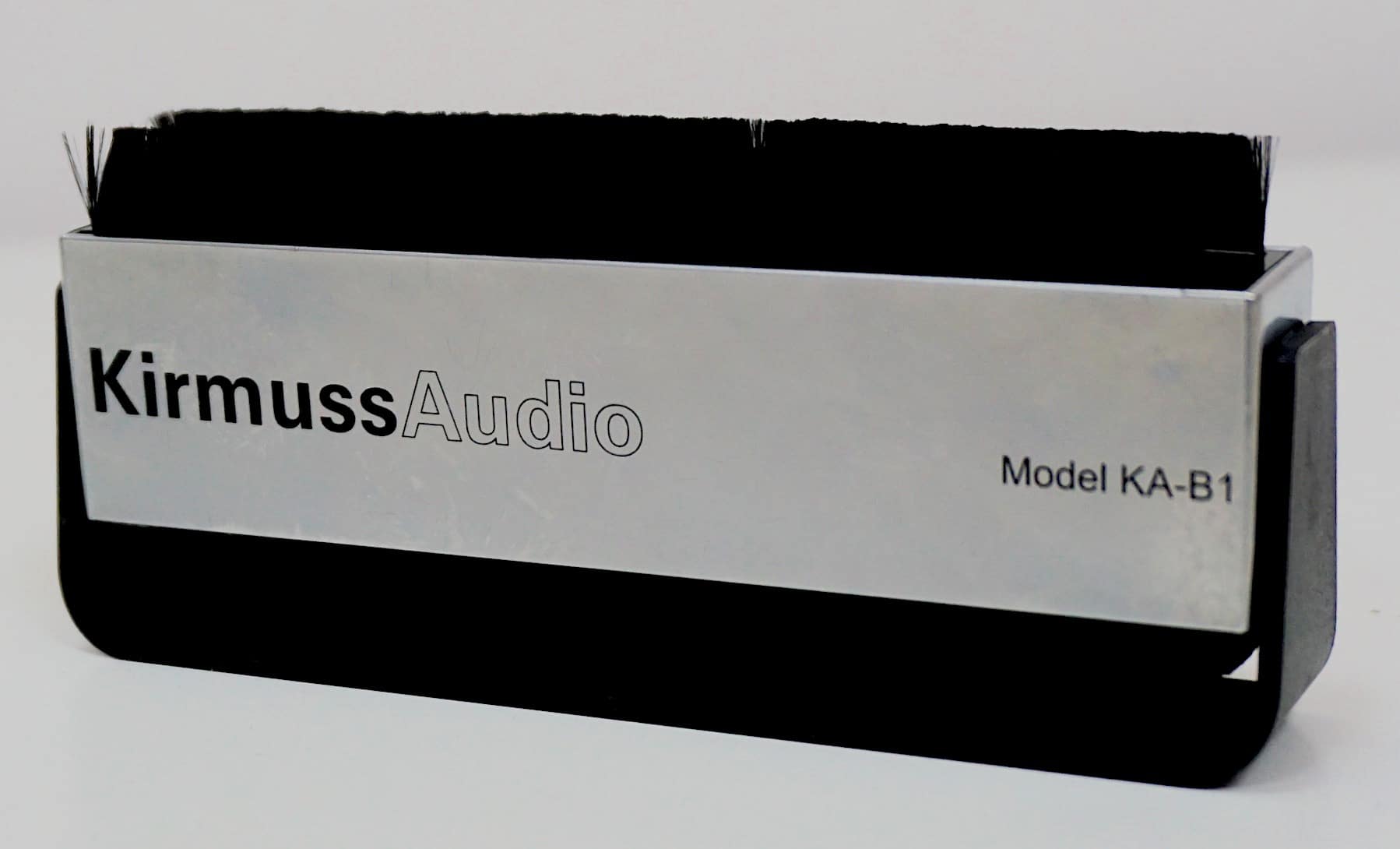
The result? As I feared, the After Care-affected record added a veiling layer to the record surface. The midrange, especially the upper mids, was slightly blunted and a little rolled off at the extremities. Dynamic range was snipped at the far end while treble was a little dull.
I put the blame for the veiling directly at the final application of the ‘anti-static’ surfactant. Once the veiled record surface was cleaned again by the KA-RC-1, the surfactant was dissolved and washed away and the dynamics were restored again.
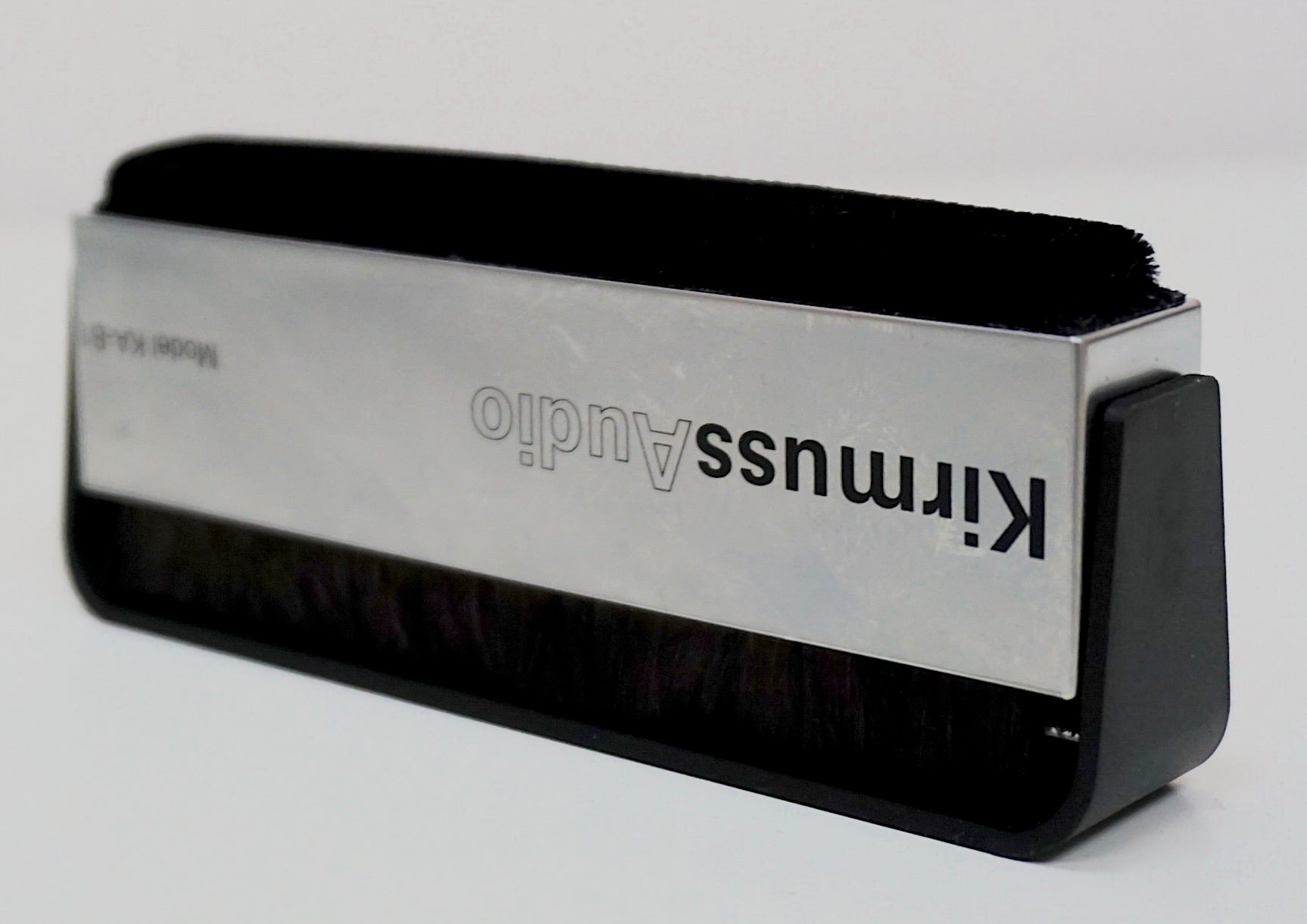
If the surfactant is added during this time to act as an anti-static application, not only do you add a sonic veil but your stylus then scoops the stuff up and collects it onto the tip. You then spend more time cleaning your stylus tip.
HIGH DOSAGE
More than that, if you add surfactant earlier, during the basic cleaning cycles using the above-mentioned spray applicator then way too much is added to the grooves. The dose is too high. It takes a long time to get rid of this stuff. You’ll find that it will collect on your stylus for some time to come. Because of the spray action, I had to introduce a separate active rinse cycle, spraying the surface of my record with distilled water, brushing it in and rinsing the record again in the KA-RC-1 for up to 10 minutes. Not practical.
Because of my earlier health concerns (see Part One for the full story) and because I binned the spray, replacing it with an eye dropper pipette, I was able to reduce the surfactant dose. Instead of three large sprays in the 12, 4 and 8 o’clock positions, I recommend almost painting a thin line of surfactant with the tip of the eye dropper at the 12, 3, 6 and 9 o’clock positions. The amount of surfactant is vastly reduced and much less is dumped in the grooves. I found next to no surfactant collected on my stylus after this treatment.
AIR DRY OR NOT?
Once you remove the wet record, instead of pushing the muck back into the grooves with the Kirmuss-recommended cloths and sponges, you can air dry in a rack. You can use a rack that you may have fashioned yourself or, if you happen to have a Disco Antistat, that manual washer has an excellent drying rack. The rack prongs that are not too high, keep the records vertical but, at least for 12” records, only touch the run out grooves with plastic tips on the end of the racking prongs.

There is a better and higher-end option here: use the vacuum pump from a ‘spare’ RCM or, indeed, buy one in especially for the purpose. This vacuum RCM will cut drying/waiting times to a fraction, will remove the liquid plus any loose material hanging around the grooves and further reduce latent gunge collecting on the stylus. Something like a Moth, VPI or similar. If you do use a machine like this, take extra care not to reinfect the grooves with the vacuum arm’s felt layer. The bit that comes into contact with the record. I would recommend cleaning this felt after each and every record side. Also, as the Kirmuss rinse cycle cleans and wets both sides, be sure to dry the vacuum RCM turntable with a dry cloth before you flip the record over.
My luxury choice, though, was a Loricraft RCM which has the best vacuum system currently on the market. The vacuum pump never actually touches the record surface and addresses each part of the record slowly and carefully. You’re talking a hefty piece of spare cash for a Loricraft but, if the option is there, then I’d go for the Loricraft just for its vacuum option. Thinking about it, a combo KA-RC-1/Loricraft or KA-RC-1/VPI or KA-RC-1/Moth or whatever combo you choose compares favourably in cash terms with an Audio Desk ultrasonic cleaner. So maybe the idea is not so silly, after all.
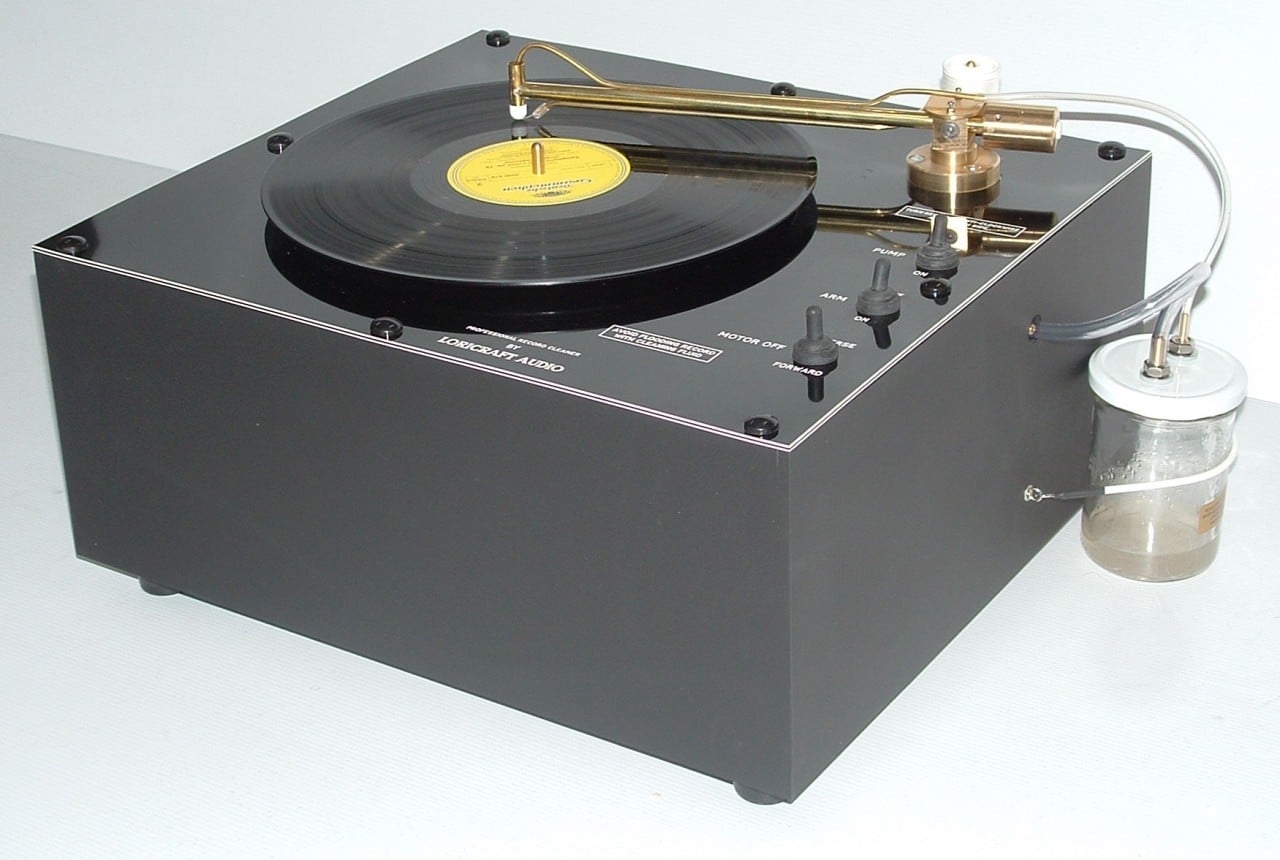
So what’s the recommendation for the Kirmuss After Care session? By all means use the carbon fibre brush for a final physical clean of extraneous dust or lint before play but, apart from that, bin the rest of the stages. They’re a waste of time and they cause issues. Then think carefully about the drying action in terms of air drying or bring in a vacuum RCM.
AN ALTERNATIVE SURFACTANT
If you buy a KA-RC-1, what happens when you run out of surfactant? You will need to buy another bottle. According to my research, each new bottle of Kirmuss surfactant costs £20 for just 60ml, which is extortionate! Kirmuss needs to look at this.
If you want to consider another option then I have an alternative that I thought was as good as the Kirmuss system, during my own sound tests.
Oddly enough, it includes the liquid supplied by competitor, Audio Desk for its own RCM. This liquid includes a surfactant. Audio Desk asks you to buy a little bottle of concentrate for £14. You then dilute this concentrate in five litres of distilled water. Instead of using that to fill an Audio Desk RCM, I would advise applying small amounts to the face of a vinyl record as an external surfactant. I would fill one of my favourite pipette bottles with just a small amount from that five litre source (which will last for ages).
Once done, I would then add half a pipette of Propylene Glycol (as discussed in Part One of this review) which can be bought HERE. This bottle will also last for ages. The Propylene Glycol will give the Audio Desk liquid a bit of bulk. When added, you shake the bottle to mix the two liquid.
When mixed, apply a full pipette around the record surface in a circle. Keep the record surface level for now and using the Kabuki brush work it into the grooves, follow a circular motion, covering the entire surface. Do that three times. Then grasp the near end of the brush to form a stiff bristle and work the surfactant into and along the grain of the grooves. Work in a spiral manner along the groove direction. Then repeat on the flip side and the record is ready for cavitation.
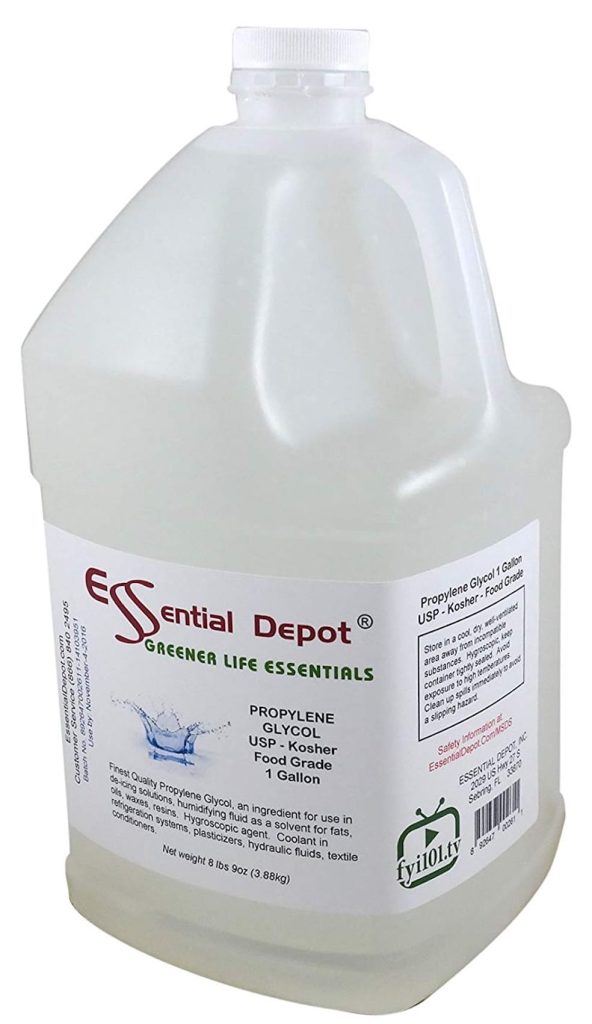
If you find that, during play, the stylus is accumulating gunk, you’ve probably added too much Glycol. Just back off on the quantity a bit and make up a new bottle. You’ll have plenty to use for experimentation.
The Propylene Glycol will keep the surfactant in place in the grooves until cleaned by the cavitation and alcohol. Using a minimal amount of Propylene Glycol will mean less will collect on the stylus tip.
Doing it this way, each 60ml bottle should cost you around 25p instead of £20 as Kirmuss demands.
Before I move on, if you decide to buy larger value packs of Propylene Glycol to make your own surfactant be careful that you purchase the correct liquid. Make sure that you buy Propylene glycol. Do NOT – I repeat, do NOT buy Ethylene glycol. The latter is nasty, can cause major problems if ingested, breathed in and the like. I’m talking central nervous system issues…brain problems…how about coma? You catch my drift on this one? Oh, and if your pets drink it accidentally, it will kill them. So then, double check that you’re buying the correct formula, eh? Propylene glycol is fine. Ethylene glycol is not.
SOUND TESTS 3
How effective can the KA-RC-1 be? How efficient is it? What are its potential cleaning possibilities? How far can it go? I wanted to test this area using, not just a dirty record but one that is full of hard, encrusted gunk.
I came across one such LP in my own collection. It was a Sarah Vaughan album on the Mainstream label, a live show in Japan. I cleaned it twice on the Kirmuss, on both occasiobs, I used surfactant scrubbed into the grooves and a total of two cycles of five minute ultrasonic cavitation.
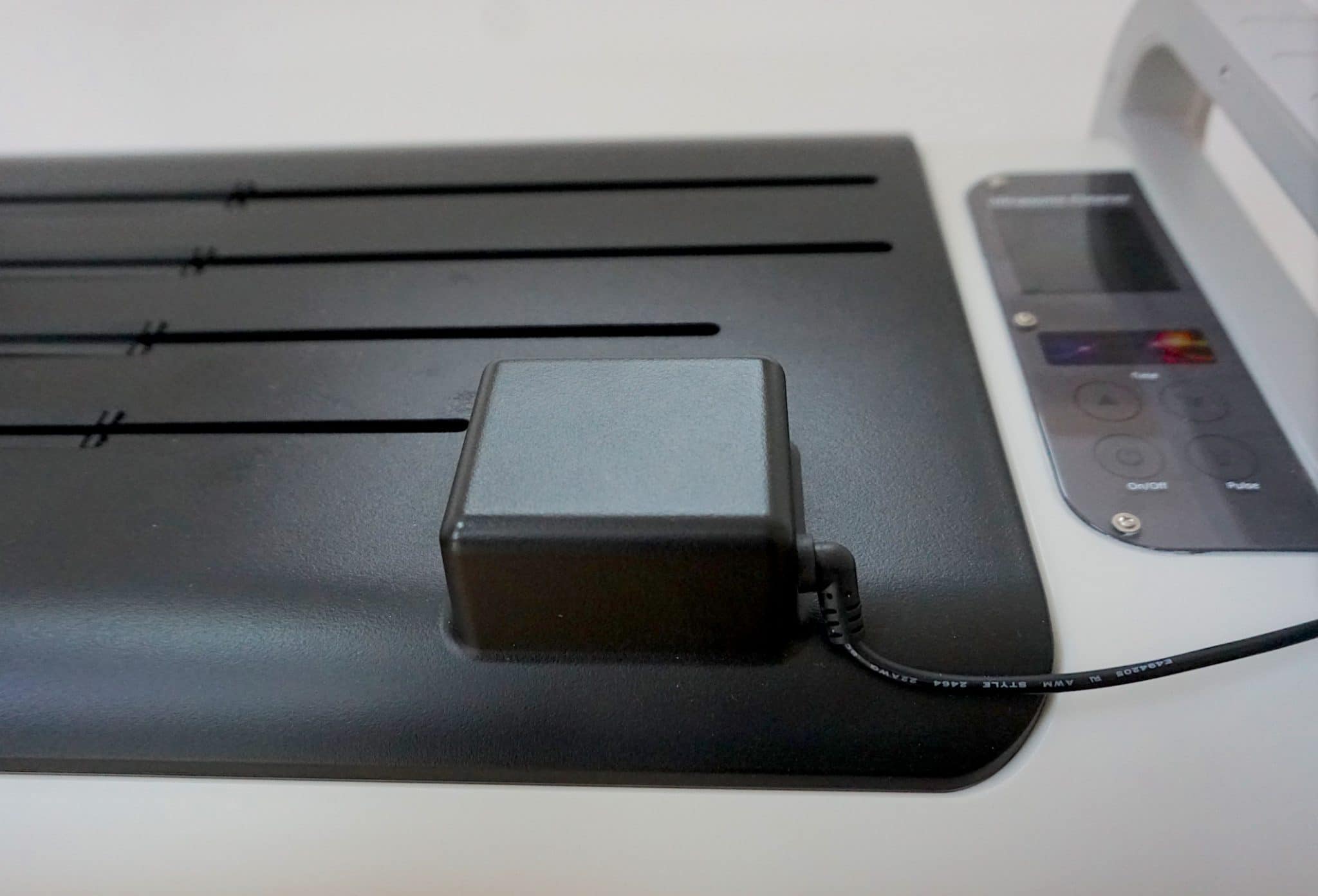
Kirmuss says that such bunged up records can be spotted by the grease-like substance that emerges on the grooves surface when the surfactant is worked in by the brush. I must admit that I didn’t see that at all. Nevertheless, if my eyes missed this so-called Kirmuss effect, my ears spotted it immediately. Playing the record immediately afterward two separate cleaning cycles was a horrendous experience! Truly poor. It sounded like the stylus was caked with muck. Yet, upon inspection, the stylus was clear. What was it? It was muck and grime that was slowly lifting off the groove floor and sides because of the early cleaning cycles and rising inexorably to the surface. It just hadn’t got there yet. So, in effect, the sound quality was worse than when I began. If this happens to you, don’t panic. In fact, see it as a good thing. A work in progress, you might say.
So I gave the record two more cleaning cycles. The results were better but not perfect. Another two cleaning cycles were employed (now, six in all). And that did it. The record sounded a little damaged around the edges but startlingly brilliant in broad terms. A RCM cannot repair a damaged record but the final sound was superior than the sonic experience I had previous to the clean. There were some beautiful upper midrange highlights here with a bass that could be actually heard for once. Instrumental separation now existed for the first time and the soundstage offered a genuine 3D depth. Hurrah!
The moral of this tale? Be prepared to experiment, tweak and thoroughly mess around with your records and this RCM to get the vinyl performance you want. You may have to keep at it, though. I had to clean this record six times but be prepared for more.
DISCLAIMER
I finally felt that I was getting somewhere with the KA-RC-1 but one thing bothered me. The KA-RC-1 did as well as the Audio Desk RCM in terms of removing gunk and muck but the Kirmuss sounded better in sonic terms. As I said in Part One, I felt the reason for that was the use of a tiny amount of alcohol in the bath in the Kirmuss RCM. The Audio Desk didn’t feature any alcohol in its bath when I compared it earlier.
What if I added alcohol to the Audiodesk then? Would that enhance the Audio Desk’s sonic performance? How would an alcohol-fed Audio Desk perform against the KA-RC-1? Wouldn’t that be a fairer comparison between the two? The ultimate shoot out?
That’s what I did but I don’t recommend that you do it. Why? Because, apparently, adding the tiniest drop of alcohol into an Audio Desk RCM will remove the warranty on the affected machine. So, officially, I would encourage you NOT to add any alcohol to the machine at all. DON’T DO IT! If you use alcohol in the Audio Desk vinyl cleaning machine and you later suffer a technical hitch to your Audio Desk RCM but the machine is rejected by the host company because of your prior alcohol use in the RCM then BE IT ON YOUR OWN HEAD. Don’t say that I didn’t warn you.
Going against the grain and breaking rules is part of my job, though. So in went the alcohol in my machine. The same amount: 0.43% of the total water volume.
SOUND TESTS 4
My first test will probably enrage Audio Desk but it was an option I had to try to cover all of the options fully. The Kirmuss uses 0.43% of alcohol in its bath. So I did the same to the Audio Desk. That is, I added 0.43% of alcohol to the Audio Desk bespoke cleaning liquid/distilled water combo and listened to that.
I played my Ritchie Havens track again and the result was pretty good. The sound opened up from its previously rather dull offering to one where the vocal was more expressive and emotive. Previously, the guitar strums dragged a bit, slowing the track. Now, the attack was more immediate and the transients were faster. I gave the LP a second cleaning cycle in the Audio Desk but found no obviously beneficial extra sound quality from this second cycle.
Then I moved on to the next level. I totally drained the Audio Desk-based liquid, cleaned the internals of the RCM and refilled it with nothing but distilled water and 0.43% alcohol. The Audio Desk bespoke liquid was not added this time. That is, Audio Desk’s own cleaning liquid was not part of the bath’s contents.
I played Emmylou Harris and You’re Free to Go from the album, Thirteen. The sonics improved still further. The upper mids where now extended as was the dynamic range. The resultant sound was never harsh nor bright but was just a tad edgy. There was a beautifully transparent quality to the sound but there was a slight, just a slight sharpness to the sound.
Next, I added Kirmuss surfactant to the surface of the Emmylou Harris LP to see if this step added something to the sound. It certainly did. All of the above sonic qualities remained but the soundstage appeared to extend left and right while the sound now had a richer, more mature aspect. It was balanced with, critically, no edge or sharpness.
Repeating this cycle a second time, including a second application of the surfactant improved matters still further. Mids were smooth, treble was extended and more information was available.
OK then, so here’s the crunch. Using the two-cycle process of surfactant application to the vinyl surface followed by an ultrasonic clean, which RCM was the best in sonic terms? The Kirmuss or the Audio Desk?
The results were interesting. The Audio Desk was the best in terms of control and maturity within the midrange, treble offered better structure and bass was tonally more interesting. The Kirmuss could be a little wayward in how it handled the overall frequency range. The Audio Desk was rather more coherent in this respect.
That said, the KA-RC-1 remained excellent in terms of its sonic performance. In purely sonic terms, there was plenty of detail on offer, clarity and transparency were both excellent the dynamic reach was impressive.
What the Audio Desk had up its sleeve was a chassis and mechanism that was wholly bespoke to the task of cleaning vinyl. This test proved that the chassis and all that mechanical gubbins inside really does matter. That’s what the Audio Desk is made to do – that’s why you pay so much cash for it. The Kirmuss, may I remind you, uses an off-the-shelf model that was tweaked for vinyl use. I feel that the tailored design of the Audio Desk told in the end. So, to repeat, given a level, alcohol-soaked, surfactant-strewn, playing field, the Audio Desk is the obvious and clear winner. Records sound better from the Audio Desk under these conditions.
That said, I’ve been using a ‘naughty’ version of the Audio Desk for these tests, complete with alcohol and surfactant. An Audio Desk from the wrong side of the tracks, you might say. An Audio Desk from the Dark Side.
Hence, officially, this test doesn’t exist because Audio Desk rejects the use of alcohol and doesn’t sanction the use of an external surfactant. Audio Desk wants you to use its own cleaning liquid. So, in official terms, at this stage of the game, the Kirmuss is the clear winner. And that’s how it’ll be (officially) until Audio Desk changes its mind and its focus. If and when it does, though…
CONCLUSION
There is just a touch of the P.T. Barnum about Kirmuss. I say that with a smile on my face because I have no wish to insult or denigrate the company. They mean well but the outfit brings this feeling upon itself.
If you attend one of its demos, you’ll see the man in the white coat, the Ringmaster’s badge of supremacy, acting like the barker Billy Bigelow in the Hollywood musical, Carousel. He’s designed to impress.
The company offers thrills and spills. It scares you with its warnings about encroaching fungus, tales that will keep any vinyl fan up at nights, a substance that threatens to cover your vinyl as Jeff Wayne might describe the Red Weed in his version of H.G. Well’s The War of the Worlds.
There are magical illusions such as the never-ending emergence of magical grease from the vinyl groove that forever spews forth like multi-coloured handkerchiefs from the mouth or some sort of analogue ectoplasm that requires the immediate assistance of the Kirmuss Ghost Busters.
There’s even the mysterious Charles Kirmuss, the man of a thousand talents, his wonders to perform (according to his adoring staff).
And it doesn’t help. None of it. Despite what Kirmuss might think. The above adds a sense of the suspicious to the company. A nervous element. You wonder how far you can trust this lot.
Yet, from what I can gather Kirmuss, as a company, has the best of intentions. I’ve talked to them a lot and that’s my feeling. It just tries too hard and it comes out wrong. It doesn’t really need to. Kirmuss has a good product here. They could turn it into a great product. They could even turn this product into a minor industry all of its own. If Kirmuss would just step off its marketing pedal with it’s eccentric manual and its slightly bizarre website and its overly quirky persona then the green gas would clear and we would all see that.
My tests prove it to me, at any rate. The core KA-RC-1 is a good product. It does the job and it does the job well. Yes, the footprint of the KA-RC-1 is very large, yes you really don’t need the After Care gear, yes you need to tweak the cleaning system to fit your circumstances and yes the basic design of the machine looks like a 12 year old’s toy but the price is about right, the performance is bang on and the core research from the design team is thoughtful and even innovative.
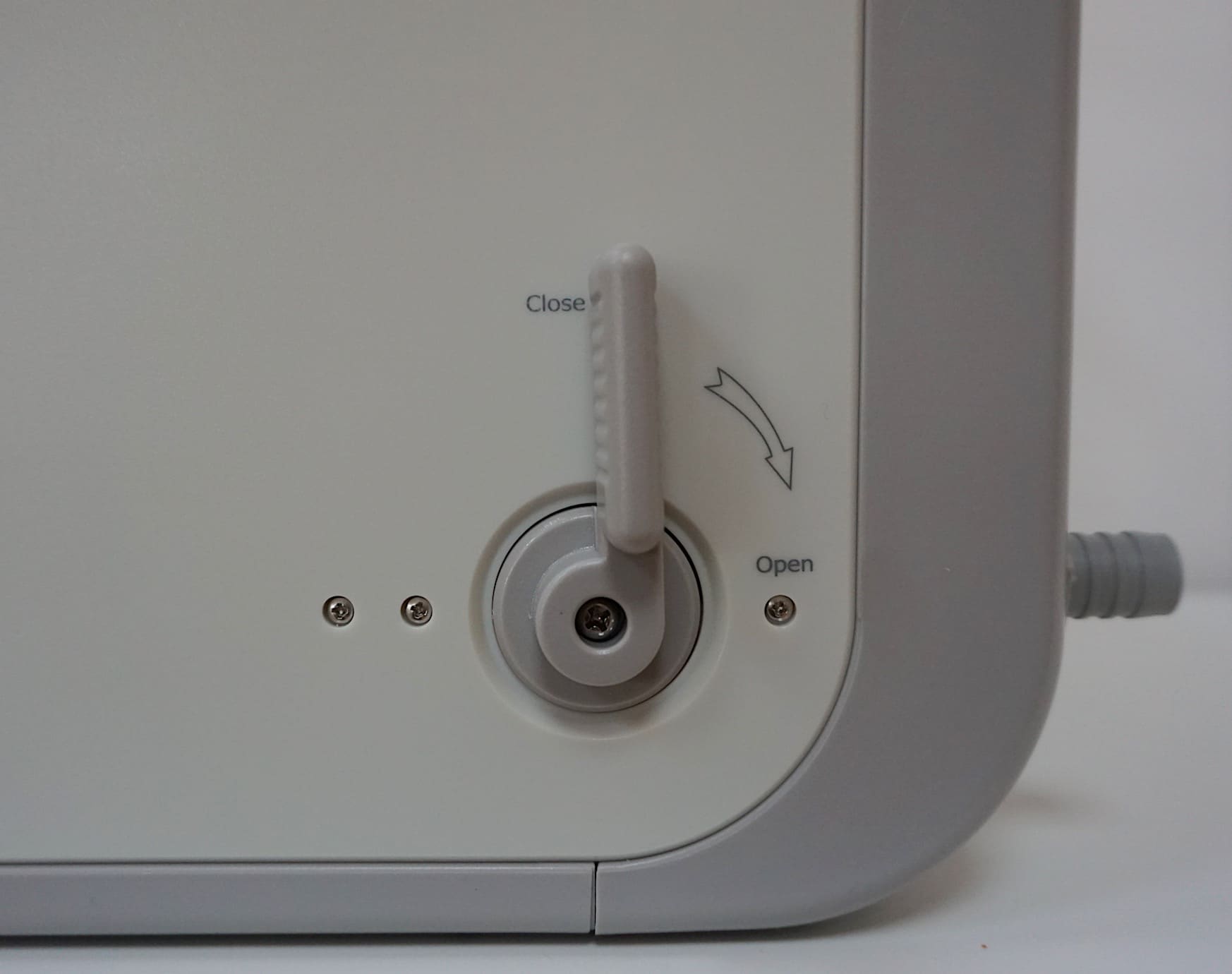
This new machine will – or should – inject the flowering ultrasonic market with a few shivers. The competitors need to look closely at what Kirmuss is doing right. They need to consider the flexibility of the Kirmuss technology. They need to re-look at the use of alcohol as part of the cleaning process.
The KA-RC-1 isn’t perfect, though. The more expensive machines out there do some things better: they offer a smaller footprint, an automatic cleaning system that people actually like with an assured feeling that the machine has everything in hand. This approach can be comforting to many. This is an important factor for many buyers. If you look at the Kirmuss tests above and wonder if it’s all too much effort and trouble, then avoid the KA-RC-1 and stick with a product like the Audio Desk.
Your buying decision should be based on your priorities in terms of vinyl cleaning, as well as your budget.
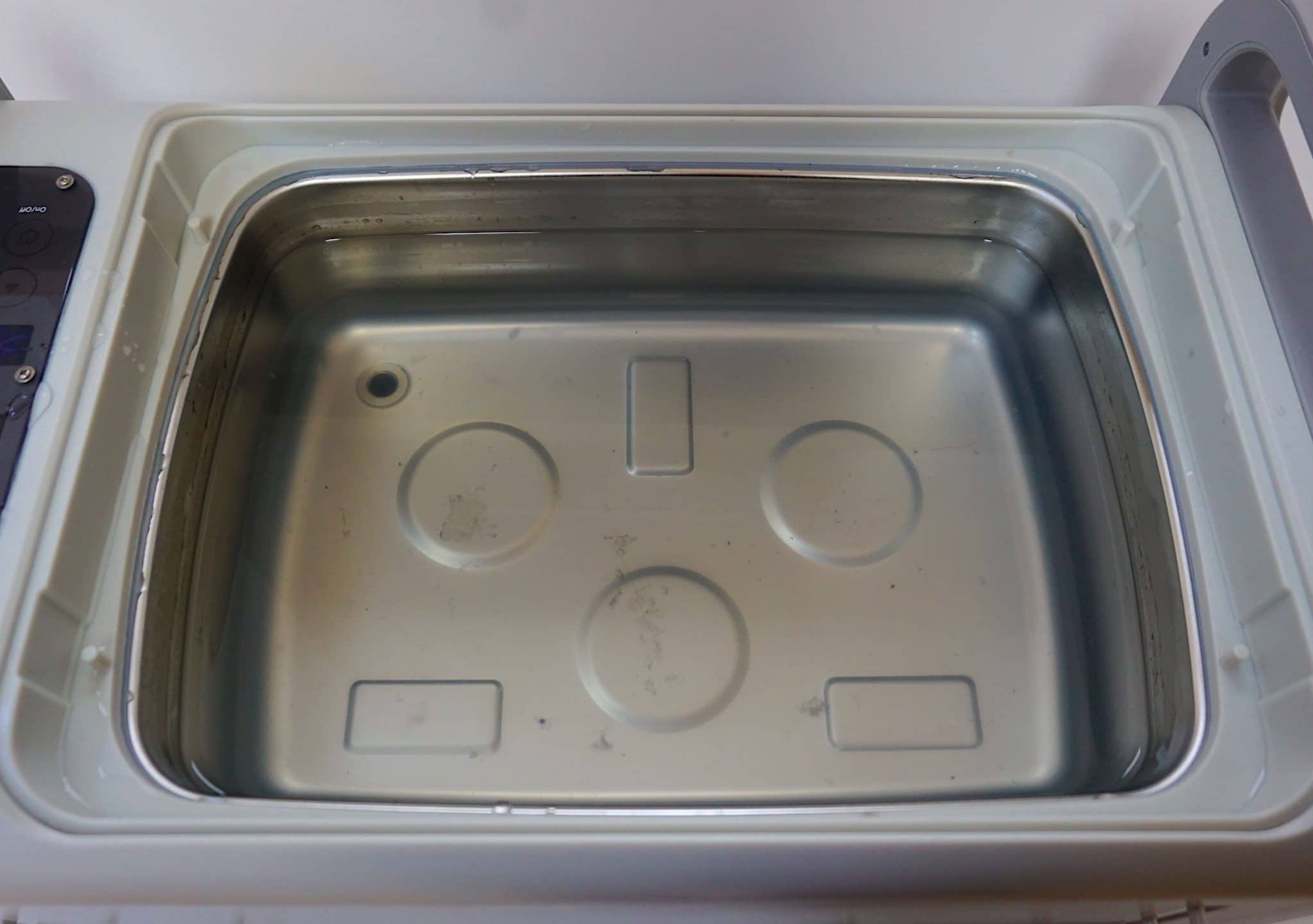
Think of it like this, the automatic RCM types like the Audiodesk are the Apple Macs or the iOS devices of the ultrasonic world. They are beautifully designed, offer a tailored and bespoke chassis and wall you off from the real world. They offer security but little freedom.
The open and flexible nature of the Kirmuss means that it represents a PC-like or Android-type of device. Imminently flexible and tweakable. With enough features and options to fit the needs of any audiophile who likes to dabble, experiment and doesn’t mind spending time on the machine to get it right while getting his hands dirty (or clean…this is a RCM, after all).
But there is that bottom line, isn’t there? One that needs addressing. And so I ask, is the Kirmuss a recommended cleaning machine? And the answer? Well, if you’ve read this feature all of the way through then you’ll know that the answer is a little complex. Firstly, because you’ve got to factor in Kirmuss the company who just insist on getting in the way and trying its best to undermine and diminish its own machine. A truly bizarre situation, via its eccentric and less than satisfactory cleaning recommendations. If pushed, at this specific moment in time, at this price point (very important), in terms of its flexibility and potential, the default format options available and in terms of its sheer sonic improving performance then the KA-RC-1 is recommended.
KIRMUSS KA-RC-1 ULTRASONIC CLEANER
Price: £1,197.60 (shop around, I have seen it on sale for £995)
Website: www.kirmussaudio.com
GOOD: cleaning performance, sonic qualities, default disc formats, carry handles, tweakability
BAD: manual, after care stage, the company itself
RATING: 8
[Don’t forget to check out my Facebook Group, The Audiophile Man: Hi-Fi & Music here: www.facebook.com/groups/theaudiophileman for exclusive postings, exclusive editorial and more!]
REFERENCE
Origin Live Sovereign turntable
Origin Live Enterprise 12″ arm
Van Den Hul Crimson XGW Stradivarius Cartridge
Soundsmith Paua Mk.II cartridge
Icon PS3 phono amplifier
Aesthetix Calypso pre-amp
Icon Audio MB845 Mk.II monoblock amplifiers
Quad ESL-57 speakers with One Thing upgrade
Tellurium Q Silver Diamond cables
Blue Horizon Professional Rack System
Paul, thank you for your interesting article – it is making me think again about about the use of isopropyl, what I am hearing and the more instinctive record cleaning decisions I have made. I have been using an AudioDesk for some 6 or 7 years now and love its conveienince for cleaning new records as they arrive, but I have found myself going back and repeating the cleaning cycle using a manual application of disc doctor miracle record cleaner (ddmrc) with a tap rise before cleaning again with the Audio Desk when time allows. Also on the odd occasions I apply the ddmdc first, I do see differences in the amount of foaming between records which is not unlike manual Kirmuss treatment. I think the thing that concerns me most with the ultrasonic cleaners is, as the water gets contaminated, how much is left on record, but one has to stop somewhere.
The problem of ‘where to stop’ is one I have too, Simon 🙂 As for the contamination, the theory is that, in an Audio Desk ultrasonic cleaner at least, the heavier muck will fall to the base of the machine while the filter is suppose to remove the rest. You could, if OCD struck, brush into the vinyl surfaces a coating of distilled water and then transfer that to another, vacuum-based, RCM for that to suck the remaining grime. I talk about this option for the Kirmuss, in fact, in its review. It’s an option. That said, I was pretty happy with the Audio Desk performance on its own.
Incidentally, I’m still experimenting. Currently varying the amount of alcohol (up to 3%, will test 6% and possibly go as high as 10% but no more) and looking at alternative surfactants.
I wonder if the AudioDesk concern with alcohol is linked to affecting the pump and internals of the machine, or a concern about the vinyl. And if the former, is it through use or long term storage or both. With the Kirmuss and its bath it is not an issue for the hardware.
Hi Simon – your guess is as good as mine, I’m afraid. They’re not the easiest people to grab hold of for a quick chat, I’m afraid 🙂 That said, the alcohol I’ve been experimenting with was very small in percentage terms. I wonder if they fear high concentrations being used.
Great review. A lot of valuable information
I do not intend to buy, in near future, an ultrasonic cleaner but, nevertheless, the article is instructive for all kind of cleaning techniques. Since my collection is rather small, 70-80 records, I will order a Knosti Disco-antistat. This set comes with a cleaning solution (I don’t know what ingredients contain) which I intend to use as a surfactant in first step and in second to clean the record with a solution from distilled water with 0,5% Isopropyl alcohol. What do you think about it?
I am very interested in your future experiments with 3%, 6% and even 10% isopropyl alcohol.
Hi Calin – thanks for your kind comments. Rather than answer you here what I’ll do is ask you to look out for a new feature I’m currently researching on cleaning in terms of ultrasonics which will have a bearing on other forms of record cleaning too. This includes experimenting with different surfactants, alcohol levels, rinsing cycles, etc. Won’t be too long I hope 🙂
Hi Paul,
I am looking forward to your follow up article. After reading Part 2 I have tried including IA mixed with the ASVC with very positive results. I am now wondering how long it takes for the IA to evaporate from the once in the AudioDesk tank. I have read the results of one test where 50% of neat IA evaporated in ten days at an ambient temperature of 22C. Thinking about the agitation the water/IA/ASVC mix gets during a cleaning cycle, and the average house tempertaure it makes me wonder about the need for topping up the IA content on a periodic basis.
The feature won’t be too long now Simon 🙂 I think the alcohol, as it is wholly soluble and thus completely mixed into distilled water, will either be drastically slowed in terms of evaporation or, in fact, will not evaporate at all. Hence, I don’t think that this particular issue should be a problem. Quite apart from that, I think the bath levels will reduce quicker because other reasons, mainly the day to day use of the unit. That is, there will be a continued lowering of the bath water over and above any basic evaporation because there will be some loss during vinyl cleaning. Some of the bath water remains on the vinyl surface and that, in itself, is evaporated by the dryer sequence at the end of the full cleaning cycle.
Thank you for the excellent review, by far the most extensive one on this product I have read. I really appreciate the comparisons to the Audio Desk, as I have wondered how they compared given the price difference. Reading the review has convinced me to try the KA_RC1. I plan to keep my Nitty Gritty for drying purposes, since it only contacts the label and purchasing a Furatech Destat III.
With regards to the frequency (35Khz) that this RCM uses. I have read that a lower frequency may actually be harmful to vinyl in the long run, which is why most other RCM’s use a higher frequency. Any thoughts on that?
Hi Henry – thanks for your comments. I need to do more research into the frequency question. What I know, thus far, is that there seems to be issues either way: too low or high. There seems to be a sweet spot for vinyl – although what that is is open to question. The higher the frequency, the more penetrative the cavitation, it appears, the smaller the bubbles the more effective they are cleaning, say, circuit boards. The lower the frequency, the greater the bubble size, the greater the erosion which is ideal of steel parts, for example. I’ve heard that 35kHz is the best but I don’t *know*. Hence, I need to check it out…for a possible follow up feature on ultrasonics perhaps? 🙂
Thanks Paul. Look forward to reading your possible follow up regarding ultrasonic RCM’s and frequency. It may end up like your quest regarding alcohol and its effect on vinyl. Different answers but no one knows for sure, but could prove very insightful as well.
Hi Henry – true! 🙂 First up, I’m researching surfactants and a recommended liquid-based approach. So watch out for that one!
I’m getting enough light coloured build-up on my stylus to require cleaning the stylus after each side of playing, sometimes mid-side. This was my first cleaning batch as I just bought the Kirmuss machine.
From now on, I think I’ll forgo the final spritzing with the surfactant.
How can I remove the gunk that is on the records that I’ve already cleaned?
Hi Michael – I would give them a rinse or two. That is, give them a couple of cycles in the machine without adding anything to the vinyl surface. That should help reduce or remove the gunk.
New review in the german magazine “Stereo Magazine” (in english) : no more surfactant !
The spray is only used as an antistatic at the end of the process …
Hmmm, you’re welcome, of course, to follow that advice Fr√©d√©ric, but I would strongly disagree with both of those points. As you can see in Pt.2 of my review. A surfactant isn’t exclusive to Kirmuss, it’s a well known tool in removing surface tension while the spray is not, in my opinion the best antistatic application. In fact during tests, it veiled detail and dulled clarity because you’re adding a new substance to the vinyl groove before you play.
Great work Paul! I have recently acquired the Kirmuss machine and am in the process of understanding its capabilities. A lot of my records have been treated with either Permastat or Gruve Glide over the years. It appears that a lot of cycles in the Kirmuss device are required to reverse my gullibility of years gone by. As a tip for others in this situation, Kirmuss recommends multiple 2 minute cycles rather than 5 minute cycles. This way you don’t die waiting for the end result… Once the white emulsion reduces during the subsequent surfactant applications you can resume a couple of 5 minute cycles. This info is buried in the website’s FAQ section. So far, on records that have been coated with previous solutions, ten plus cycles are needed and even then surface noise is still present, but sonics are greatly improved. Cheers and thank you for alerting everyone to this machine and also opening up the possibilities of experimentation.
Thanks Dahl.
Thanks for the thorough article, Paul. I’ve not found a more detailed review than yours.
I purchased a KA-RC-1 a few months ago and have mixed results. I am happy with the hardware but the After Care is something that I think is the cause of my problems. First of all, the foam inserts in the top damaged a few new records. They eventually ripped and caused adhesive to stick to a few records. I decided to remove them and the cleaner works much better. I no longer have issues with dirty, surfactant-soaked foam contacting or scratching my records.
The distilled water with the 0.43% IPA is clean with the first record. As you run more records through it with surfactant applied, the surfactant gets mixed into the bath more and more. I’m going to experiment with running two batches: the first for cleaning with surfactant, and the second as a final rinse for records that have been externally rinsed first with distilled water only.
Finally, I work in the semi-conductor industry. We use clear high-grade plastic carriers for 12-inch silicon wafers. These contact the wafers only on the very edge, so they are perfect for placing a 12-inch record in when cleaning it or applying surfactant because the backside does not contact anything. I know these aren’t readily available to the public, but it is ideal for this.
Thanks for you kind words, Allan and for your following notes. Let me know how you get on with the two-bath solution. Those carriers sound interesting – any chance of posting a link for an image, by any chance?
Here is a link to photos of the wafer carrier, before and after I disconnected the top from the bottom.
https://www.amazon.com/photos/shared/BL2Id2xbTJiQ2VS3bxCCUA.hDNK6XsnPQx2Ri-rR-Psts
The two batch experiment did not yield good results. In fact, nothing has so far. I listened to the last few records that I’ve received BEFORE cleaning them. They were quiet for the most part. Afterwards, there are “crackles” that weren’t there before. I am doing more harm than good at this point. I will keep experimenting.
Thanks for the update Allan and also the link. Much appreciated. Are the carriers available to buy generally?
They are available to buy but I don’t know the price. Here is a link:
https://www.entegris.com/shop/en/USD/products/wafer-handling/wafer-shipping/300-mm-wafer-shippers/300-mm-H93-Single-Wafer-Shipper/p/300MMH93SingleWaferShippingBoxes
It looks like a minimum order of 5 and I’m sure they are expensive.
UPDATE: I have an old discwasher(R) brush and D4 fluid from the early 80’s. I figured the D4 fluid had gone bad by now, but after seeing a Michael Fremer video about his TM-7 fluid from 1985 still being good, I decided to give it a try. Applying the D4 with the discwasher(R) brush reduced the static almost completely. I think I am on the right path now. I ordered a Pro-Ject VC-S and TM-8 fluid to perform a final clean on my records after I run them through the KA-RC-1. I also ordered the LAST Record Preservative for the final step. We’ll see if it works.
Excellent stuff – glad you’ve found the right path, Allan.
Regarding the white toothpaste-like substance that you see Mr. Kirmuss discuss in all his videos, I found the following on the LAST website:
https://thelastfactory.com/misc/mystery-appearance-hibernating-vinyl-crud/
It seems like it might be related.
I do see this white substance on some records more than others. It is hard to tell if it bubbles from the scrubbing or some other substance. I have cleaned some records 8-10 times but it never completely went away.
Hi Allan – I don’t doubt that you are seeing the toothpaste substance and I’m also not surprised that its appearance varies but I wouldn’t worry too much whether you see it or not and I wouldn’t rely on it as a fixed indicator of performance or a particular cleaning state.
How are you cleaning the records exactly during the times when it “never completely went away”?
Apart from the above…despite the tiny nature of grooves, the poor things can be subject to many horrendous cleaning products (if second hand) while we really don’t know the true nature of many of the original vinyl recipes employed by some vinyl pellet suppliers over the decades (I’m doing research on this). For second hand records, far too many people clean vinyl with soap or household products and its possible you might be seeing that sort of thing on some.
Apart from that, as I say, the gamut of vinyl recipes (all secret, I have to add) means that the naturally occurring “release agent” which hardens after production might also be secreting something odd during cleaning (not sure about your case but, again, it’s entirely possible). You might be coming across these isolated occurrences.
The problem I have with Kirmuss is that it generalises and insists that you should see it *always* if you use a Kirmuss machine and that, if you don’t, you’re doing something wrong or you’re using a non-Kirmuss machine and you should almost feel guilty for that. For Kirmuss, its surfactant is a producer of this toothpaste substance (I found this during the review during before/after tests along with stylus gunge build up) which only confuses the issue further.
I only just re-entered the vinyl hobby, so all of the records I have been cleaning are new. The white paste has occurred only on new records. My old records, what few I have left from the 80’s, were poorly stored and are badly damaged. At some point, I will attempt to salvage some of them. I only used discwasher D4 fluid on them back in the day. I will report if I see anything.
Hi Allan – yes, very happy to hear from you on this.
UPDATE: I have good results to report. I cleaned a new album and I didn’t hear a single click or pop on side A and possibly two on side B. I was very surprised but very, very happy. I started with the Kirmuss and ended with the Pro-Ject, with the final step of applying the LAST Record Preservative.
I used the Kirmuss for ultrasonic cleaning only. I didn’t do the full regimen. I filled it with distilled water with no alcohol, and added a very small amount of TERGIKLEEN. I removed the foam strips from both 12″ slots. I ran the record through four 2.5 minute intervals (total 10 minutes), in the following positions: 12″ slot 1 with side A left, 12″ slot 1 with side B left, 12″ slot 2 with side A left, and finally 12″ slot 2 with side B left. My reasoning is that the record surface would get more ultrasonic activity in all four positions than if it sat in only one position.
Next I used the Pro-Ject the “standard” way with TM-8 fluid, which seems thicker than the Project fluid. It seems to leave more of a film on the record. I’m concerned about the force of the vacuum arm on the record surface and if it is scratching it.
Finally, I put a coating of the LAST Record Preservative on the record after it was dry. I will experiment further but at least I now can clean records with great results.
Excellent work Allan – congrats! Nice idea re. moving the record into different positions. Intriguing. Which triggers the question, are there ultrasonic ‘hot spots’ in any one typical machine? I may ask a few questions if I can find an industry expert. I haven’t looked yet but is Tergikleen a Tergitol based concentrated formula? If so, does it modify the original substance, Tergitol, in any way?
When you place a single drop of the Tergitol-based TERGIKLEEN in the ultrasonic tank when it is full of distilled water only, the drop floats around for a while because it doesn’t dissolve quickly in water. You can easily see the ‘hot spots’ when the drop floats close to them. That’s what gave me the idea that each track on the record may not get full exposure in one position.
Paul, one last thing. Regarding removal of the foam pads on the 12″ slots: if only a few drops of TERGIKLEEN are used, I can lift a record very slowly out of the slot and it will have almost no drops of fluid on it, looking like it was dry. It takes about 15-20 seconds but I don’t have to worry about fluid dripping on the top of the slots or having to wipe off the record before putting on the Pro-Ject vacuum RCM.
Plenty to think about Allan – thanks again 🙂
Hello, my name is Edwin and I am from Peru, I have translated all this to understand well, I love the idea of ​​cleaning my vinyl in the best way, for reasons of cost (and currency exchange) just buy a GT ultrasonic wash tub Sonic 6 liters and 40 Khz. A question to be able to make the alternative solution that you mention (distilled water, audio desk solution and propylene glycol) could you tell me the formula for a liter of distilled water and audio desk solutin, how many drops of propylene glycol should I make?
Thanks for your question edwin. Since this feature, I’m ‘upgraded’, as it where, my thoughts and liquid cleaning system. I would buy distilled water, alcohol, the glycol but also Ifotol to use as a surfactant: https://www.amazon.co.uk/Ilford-Ilfotol-Ionic-Wetting-Litre/dp/B000KZ7QWK/ref=sr_1_1?keywords=ilfotol&qid=1565944780&s=gateway&sr=8-1
Dilute the Ilfotol as directed in the instructions on the bottle.
Take a litre of distilled water. To that full bottle of water, add 7% of isopropyl alcohol. No more than that. Shake well. Using that mix ratio, fill the bath of your ultrasonic cleaning machine.
Fill two pipettes of glycol, add them to its glass bottle (i.e. here’s the bottle/pipette combination, you can buy here https://www.amazon.co.uk/gp/product/B00IZOCRB8/ref=ppx_yo_dt_b_search_asin_title?ie=UTF8&psc=1)
Take the diluted Ilfotol (diluted in distilled water of course) and fill the rest of the glass bottle. Close. Shake well.
There’s your machine bath mix and your surfactant mix.
Hi, I didn’t buy Ilfotol, although I think I can get it, tell me it’s very different from 10M nonylphenol (tergitol NP10) ??? This if I obtained, assuming that I follow your instructions for the ultrasonic tub, it would be for 5 liters of distilled water to add 35% isopropyl alcohol.
On the other hand for the spray with surfactant (ilfotol) and its preserving agent (propylene glycol) I did not understand very well, for a bottle with a capacity of 50 ml, how many drops of ilfotol and how many of propylene glycol should I make?
I thank you in advance for helping me and for your patience.
I’ve yet to try the Terigotl, Edwin. It’s on my research list.
No, 7% alcohol to any amount, 35% will damage your vinyl.
The Ilfotol should be diluted in distilled water as per the instructions on the rear of the Ilfotol bottle.
Re Glycol – using that pipette bottle I indicated, two full pipettes of glycol to be inserted into the bottle (each pipette actually fills about three questers of the way, I find). Then fill the rest of the bottle with the diluted Ilfotol. Then shake too mix.
Paul
Does your recipe for the surfactant mix do the same toothpaste thing as the Kirmuss surfactant?
A moot point George – and thanks for the question – because I challenge the entire toothpaste before/after thing spouted by Kirmuss. I say its irrelevant and a marketing ploy. I also say this after directly challenging them on several occasions without any satisfaction at all. All of the company’s responses to my direct surfactant queries were evasive. Basically? Ignore that supposed effect.