The Article
VINYL CLEANING GUIDE PT. 1: MANUAL METHOD
18th December 2020
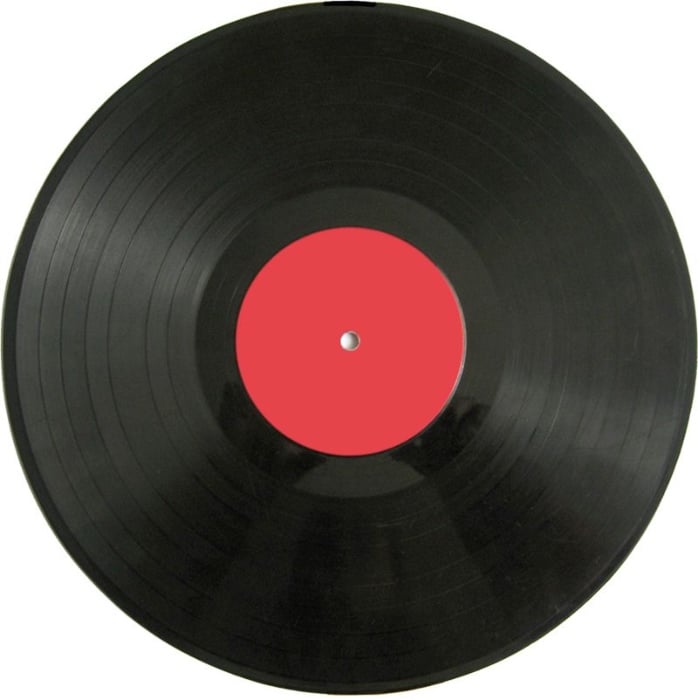
Much requested and long promised but it’s finally here, the Vinyl Cleaning Guide. This is the first of a proposed trio of ‘How To…’ features. In this initial outing, Paul Rigby examines how to clean vinyl using a manual process
As there are a multitude of ways to clean your vinyl, I’ve decided to split this Vinyl Cleaning Guide into three parts.
Part 1 is the manual option and the one I’ll be looking at here. There are a multitude of ways to clean your vinyl. If funds are tight, you can use a manual process. What do I mean by manual? Things like a felt pad, a Pixall Roller (remember them?), carbon fibre brush, Disco Antistat manual machine and its brethren Spinclean and the like. More on this below.
Then there’s the fully-fledged record cleaning machines based upon a vacuum process. Everything from the low-cost Moth and Pro-Ject machines up to the more expensive Loricraft et al. The RCM method will be reserved for the Vinyl Cleaning Guide Part 2.
Finally, ultrasonic technologies will be discussed in the Vinyl Cleaning Guide Part 3.
To save time, if you just want to skip to the cleaning methods and that’s all you signed up for here then, by all means, scroll down to the heading: Required Tools.
If you’re already kitted out then skip that and scroll down further to Cleaning Your Vinyl – Step by Step and read from there.
ROOTS OF THE SYSTEM
For everyone else, a bit of background might reassure but also provide a bit of context as to why I decided upon this method.
After all, you’re being asked to use this new Vinyl Cleaning Guide on your precious vinyl. To have confidence in the system itself, via a bit of background and an explanation of the system itself, should be in order I reckon.
I haven’t come to this point in isolation and I haven’t just picked it out of thin air because it sounds good or a chap told me about it down the pub. There’s been years of application and research behind it.
This Vinyl Cleaning Guide was the result of ongoing and exhaustive testing. If new technologies or techniques presented themselves, I experimented with those and either discarded or adopted them as part of the ongoing evolution.
In that quest I was aided tremendously by my job. That is, as a full time hi-fi journalist I have been very fortunate to be able to call upon new products, of varying types and price points, to test on a regular basis. Whether they be low cost tools, elaborate cleaning machines, liquids, brushes and more. Having the opportunity to compare and contrast a host of products, I was able to undertake a broad comparison with most of the products out there, currently on the market.
Hence, there have been numerous occasions over the past years where I thought I’d found ‘the answer’. The final cleaning system. The One. Only to be presented with a new cleaning liquid or new technology or new technique. That’s then opened new doors to further tests and possible improvements.
Hence, I realise that the Vinyl Cleaning Guide I offer here will, I have no doubt, be improved and enhanced in the future sometime.
As such, there is no ultimate cleaning system. And don’t be fooled by the person that says that such a system exists. There’s only the best system you have, thus far. Improvements will be lurking around the next corner. Or should be. I know that I never rest and am always testing new hardware, liquids and techniques.
The final parts of the puzzle began to be applied late last year. At that time, I began to undertake the testing of a range of ultrasonic machines. This began around September 2018 and finished during the Summer of 2020.
During that time, I took it upon myself to seek out and interview a host of professionals who might be better able to shed light on the vinyl product itself, its make up and behaviour. The idea was to better understand thus stuff called ‘vinyl’.
That involved a range of interviews with the vinyl industry itself. And when I say vinyl industry I mean people who are involved in actually creating the raw material, those who use it in pressing plants and recording studios.
Hence, I talked to two UK companies who create vinyl pellets (i.e. INEOS and Dugdale). Two of the most important outfits currently in operation in the world, actually. Vinyl pellets are the raw material that’s bought in by vinyl pressing plants and is used to make vinyl records.
I also talked to a lady, based in Canada. A chemist, she is employed as a consultant to Abbey Road and has an excellent knowledge of vinyl.
Similarly, I talked to the MD of a company, based in the UK this time, who create blank acetate discs and cutting stylii for the recording industry called Micro-Point, formerly Transco-blanx. Both products were and are used by Abbey Road during the creation of demo discs. Micro-Point’s products have been in use since the 50s. Again, their knowledge was invaluable.
As was the information I received by the General Manager of the current Vinyl Factory vinyl pressing plant, the old EMI Hayes site. The same one used to press all of those old Beatles records of yore and one that originally swore by its original ‘kite’ marks of excellence, I recall. In fact I myself once paid a visit to the place and was shown the thick ‘kite’ standards document they used, when the plant was still in EMI hands. Oh and by a man in a white lab coat, would you believe. Yes, they still existed, even then. I think this was around the year 2000. Possibly a bit later.
So you can see. I ran around collecting as much information as possible, over the months, in my quest to find the best possible method of cleaning vinyl discs.
I repeat though, the Vinyl Cleaning Guide I present here is not perfect. It can’t be. Such a thing doesn’t exist. It remains the best system I have to hand for now. Who knows, next week, I might change and improve upon it.
THE SYSTEM
The Vinyl Cleaning Guide I use is based on three elements:
ALCOHOL
The first is the use of alcohol. Depending on the advancement of my own research, I have rejected, adopted, rejected and have now adopted it again. My initial caution in its use related to the fact that alcohol can be aggressive when used in direct contact with vinyl. It can soften the material leading to groove wall distortion and even brittleness in extreme cases, if used over long period of time.
Used judiciously and in small amounts though, it can be highly beneficial in terms of vinyl cleaning. It took me a while to find that out. I eventually found the correct proportions over months of testing.
I have produced a more in-depth study of alcohol in video form. You can find the link below. This video also talks about the nature of vinyl itself. A subject that is also important when cleaning the stuff is being considered.
Most people think that vinyl is made purely from PVC. More knowledgable people realise that other substances are used in its creation. In fact, a vinyl disc is an amalgamation of a dozen or so different chemicals (the quantities vary depending on the individual pellet company producing the recipe). All of which are useful in terms of vinyl production and sound quality.
What many don’t know though is that the recipe for vinyl itself is not fixed or constant. Each vinyl pellet company has their own recipe (well recipes, six variants are on hand every single working day) while that recipe can change multiple times over the years via modifications and tweaks.
Which means, if you add up the multiple recipes used on a daily basis by each company, that there’s a 40-50 pellet companies currently operating in the world and hundreds more have gone to the wall over the past several decades, the history of vinyl consists of possibly thousands of different vinyl recipes, all of which hold their own chemical properties and behave differently when faced with stress, pressures, heat and yes, cleaning products.
This also means that, quite possibly, and especially if you hold older examples, every vinyl disc in your current collection may very well be chemically unique.
You can find more via the link below:
SURFACTANTS
Alcohol is one of the main points of this cleaning regime but surfactants is another. Finding out about surfactants was a revelation to me in terms of vinyl cleaning. Its use took the standard of my cleaned vinyl discs onto another level. I only came across the technique when ultrasonic technology entered my professional life a few years back but I soon found that surfactants could be applied to any sort of of vinyl cleaning.
I have written a Guide to surfactants HERE which will explain what they’re all about, what surfactants are currently out there and my preferred product. I won’t repeat myself here so please check out the link for more on that. Suffice to say that surfactants play a part in this cleaning guide.
ABRASION
Finally, one of the most neglected parts of vinyl cleaning is abrasion. I haven’t talked too much about this in the past so let’s examine the process now and find out why its important to the cleaning of vinyl.
Talk of abrasion is not something you tend to see within editorial dedicated to hi-fi. And yet. Here we are.
Don’t settle down too much because I want to whisk you off to your school days for a moment. Abrasion was always that thing you talked about in Geography class as the force that transformed rocks into nicely rounded pebbles. Ready made to add a tad of textural variety to your garden or to hand paint as a ladybird or hedgehog and sell on Etsy. Isn’t nature wonderful?
Abrasion is also something that’s sorely needed in hi-fi. Trouble is, we ain’t getting enough of it.
To explain why, I want you to picture TV personality and actor, Tony Robinson. The Baldrick of this parish and the man who would gaily bounce around a different sort of trench on the BBC TV programme, Time Team. Within which, he would run around terribly fast, hither and thither, securing breathless updates on the latest dig, offering wide-eyed excitement and puppy-dog enthusiasm. Fit to burst, he was.
Archeology for the masses it might have been but I want you to recall the sights inside one of those trenches.
Just ignore the wide-brimmed hat and West Country accent of Phil Harding for a sec and look below. There you will see an eager young tike, prodding the hardened soil. A piece of pottery is partially revealed. Our intrepid urchin is carefully brushing away the friable dust and soil. There, like some remnant of the Roman version of Habitat, we can see the patterns on a fragile pot. No doubt used to contain olives. Perhaps wine. Who can tell?
Now keep looking at that pot.
This trench is actually a metaphor. A metaphor for a vinyl groove. That dust is the daily grime that builds up in the groove. The solid, caked, baked soil? That is a heady concoction sautéed lightly from hardened oils emanating from sweat, the fabled ‘release agent’ from the original pressing plant and other substances that I wouldn’t like to dwell upon in a family-friendly website.
The pot itself? The detail you’re desperately trying to access when you listen to a vinyl record on your hi-fi.
Time Team perfectly illustrates, not just how difficult it is to properly clean your vinyl, it offers the essential clue as to why many of us vinyl fans are not cleaning our vinyl properly. Because your detail remains stuck in the trench. It’s all down to abrasion. Or the lack of it.
Whenever you clean your record, the chances are that you will clean it manually with a felt pad or carbon brush or some such. If you’re flush with a bit of cash, you may have spent out on a record cleaning machine (RCM). There’s plenty out there, you know the brands. They range from a couple of hundred pounds to a couple of thousand.
I’ve tested and used most of them.
In use, you either clean ‘dry’ with that felt pad or brush hoping to dislodge as much dust and grime as possible.
With a RCM, you’re probably looking at using the machine in conjunction with a liquid of some sort. The reckless will apply, directly to the vinyl surface, a liquid containing a high-strength alcohol that will risk immediate damage to the groove. Others will apply an enzyme-based liquid.
The upshot for both applications is that you spread the liquid around the vinyl surface with a brush of some sort, cross your fingers then you hoover up the liquid and then you’re done.
The hope is that you will improve sound quality. You will. But the degree of improvement will only go so far and not far enough.
I’ve been testing record cleaning liquids and hardware for decades now. Every time I found a new toy to play with, one that did a good job, right then I would think to myself, “This is it! I’ve finally found the answer! I can rest easy now and just play my vinyl.”
Then I would write about it, proclaiming how amazing liquid Y was and how much more efficient RCM X was and how System Z was truly the way to go.
Three months later, I would discover a new liquid/system/hardware and I’d have to think again.
Well, I’ve been doing a lost of testing of late and the one element that is becoming essential in terms of vinyl cleaning is, you guessed it, abrasion.
Liquids – whether applied directly to the vinyl surface or applied as vinyl is dunked into a machine-held bath – act like an archeologist’s brush. They shine the easily accessible detail, the detail that’s there yet veiled.
If you want to find the rest. The detail hiding behind the hardened oils? That trench-based hardened soil I mentioned above? The hardened stuff in the groove that won’t shift by dowsing with a drop or two of liquid? You need abrasion. Nothing too aggressive of course. We have to be gentle when applying it because this is vinyl we’re talking about, after all. Nevertheless.
Abrasion is also part of this cleaning system. We’ll find lots of abrasion below, during our cleaning process.
REQUIRED TOOLS
The above forms the basis of this Vinyl Cleaning Guide and provides clues as to how this thing actually works. Now I turn to the tools. What will you need to complete your clean?
Buyer’s links are provided below.
1: Disco Antistat
Price: £46.50
Contact: Amazon, eBay, etc
This Vinyl Cleaning Guide looks at cleaning your vinyl. It’s not a buyer’s guide of manual cleaning tools. I have spent years doing that sort of filtering and the Disco Antistat is my manual cleaner of choice. This is the best manual cleaner I have found, currently for sale on the market. It offers a relatively low cost, great value, it’s easy to use and is wholly effective. But look, I won’t repeat myself here, either. You can read a full review of this product HERE. Oh and ideally, you will need two units for this Cleaning Guide. You can get away with one but two is best.
2: Distilled Water
Price: £2.95 per litre
Contact: Amazon, eBay, etc
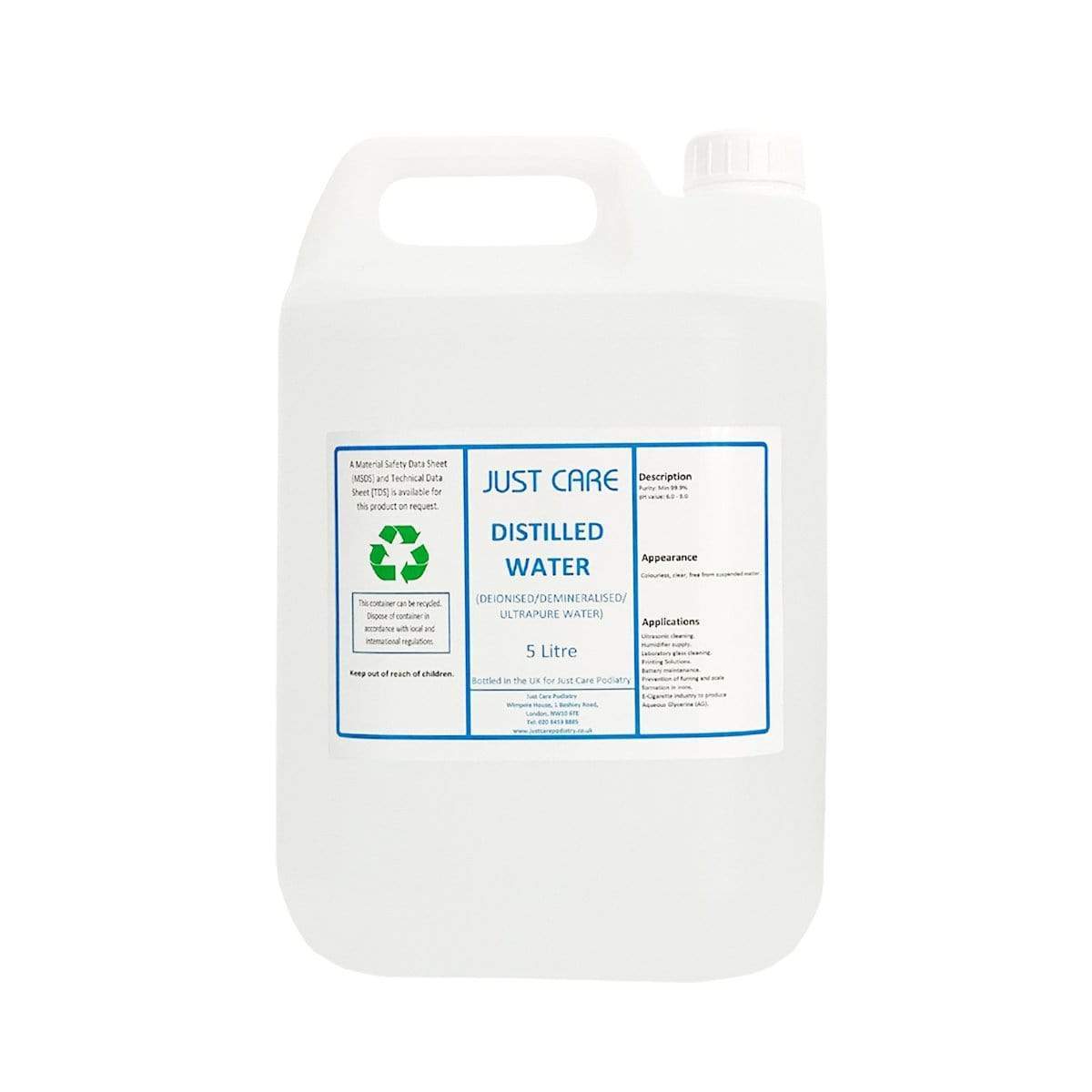
Distilled water will be the main content of the Disco Antistat’s bath. I use distilled water as opposed to any other filtered variant because of the range of potentially troublesome elements that distilled water rejects and other do not. For example, deionised water reportedly does not remove bacteria, viruses or other organic compounds.
3: Alcohol
Price: £4.05 per litre
Contact: Amazon, eBay, etc
I use Isopropanol at 99.9% strength. I see no purpose in using a solution of lower strength because products such as Rubbing Alcohol (70%) merely fill the other 30% with distilled water, lowering the monetary value of the product because you’ll need to use more of the stuff to achieve the same ends. Hence, I would recommend using Isopropanol at 99.9%.
4: Tergikleen
Price: £26.50 per bottle
Contact: eBay
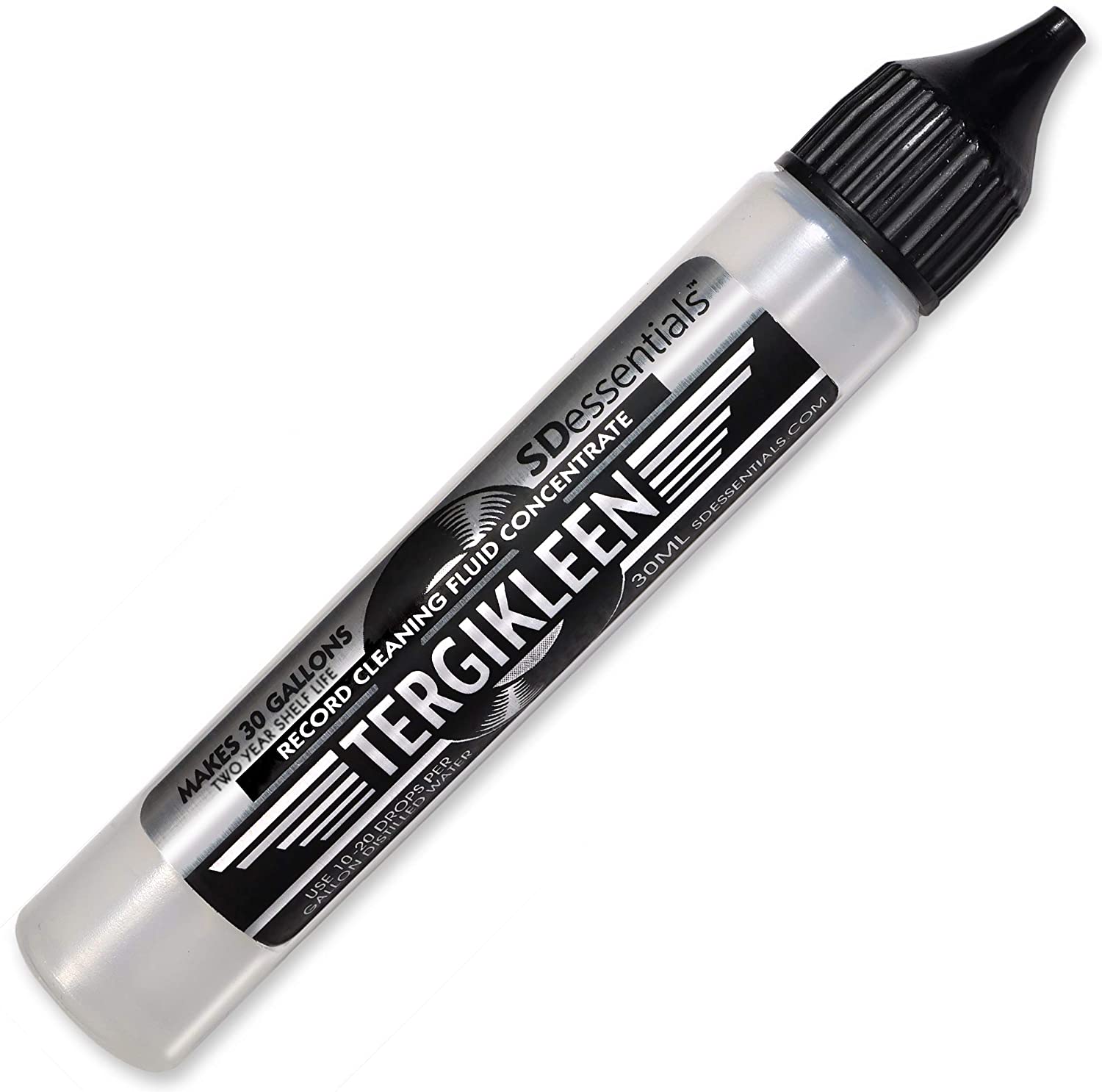
This is my surfactant of choice but you might prefer another. The surfactant feature I talk about above provides a selection of surfactants to choose from. Tergikleen is based upon the well-known surfactant, Tergitol.
5: Pipette
Price: £7.69 for two bottles
Contact: Amazon
To apply surfactant to the vinyl surface. Or more specifically, a glass bottle secured with a pipette, screw-top vial. I use two at 50ml capacity which provides a bit of leeway before it has to be filled again but it’s small enough to be used ‘on site’. That is, where you do your vinyl cleaning. Use one for the surfactant and the other to hold your Glycol. Label both in case of future mix ups. Both liquids are easier to dispense form these small vials.
6: Kabuki brush
Price: Various [see text]
You will need this when applying surfactant to the vinyl surface. A Kabuki brush is a lady’s make-up brush. Short and wide in nature and featuring stubby bristles, this little thing is perfect for pushing surfactant deep into the grooves. Don’t be afraid to spend out on this one. You can buy one for a couple of pounds but I’d recommend getting a good quality example to prevent bristle and fine hair shedding. There’s no point in trying to clean your vinyl if you only succeed in adding more debris to the grooves at the same time. Mine cost around £20. There’s lots of brands out there. Try a specialist make-up store on line but Amazon should be fine too.
7: Water Bottle [two]
Price: £2
Contact: Supermarket and general shops
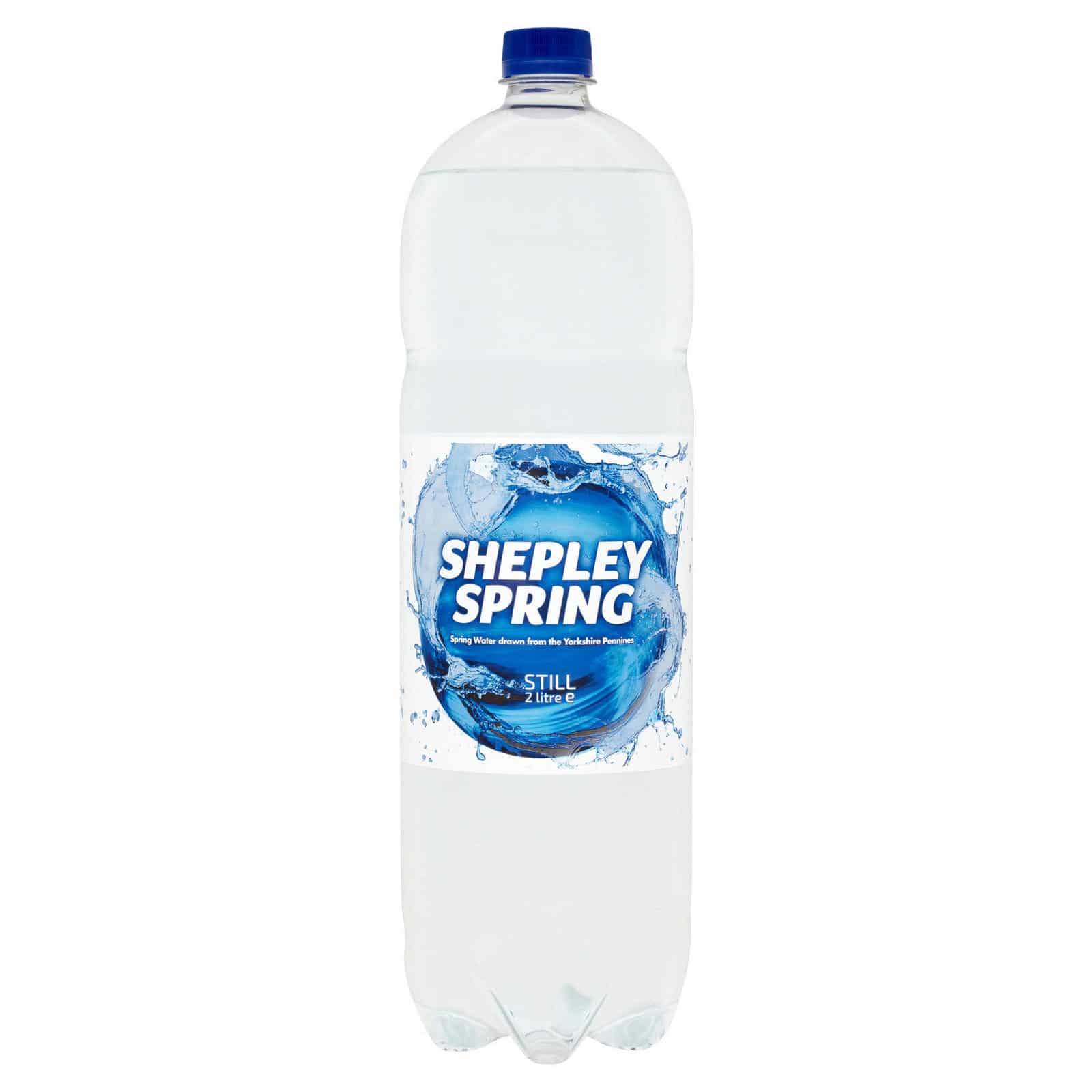
What I’m talking about here is an empty spring water-type bottle of 1.5-2 litres. The sort you might buy from a typical supermarket. You will need two of these.
8: Propylene Glycol
Price: £11.67
Contact: Amazon, eBay, etc
Because the Disco Antistat cleans your vinyl in a vertical position, if you add surfactant to its surface, gravity will try to pull it off again when the disc sits vertically. Mixing your surfactant with a measure of Glycol will fix the surfactant deep into the grooves with no loss of surface contact. Do NOT buy ethylene glycol, it’s particularly nasty stuff. When you receive your large bottle of Glycol, decant a small amount into a glass vial (see 5).
9: Measuring Tube
Price: £8.50
Contact: Amazon, eBay, etc
To measure the amount of alcohol you will need per litre of distilled water. The price here include a pack of five plastic measuring tubes.
10: Container tap
Price: £5
Contact: eBay
Because I know that I’ll be cleaning vinyl for some time to come, I tend to buy 25 litre ‘barrels’ of distilled water. Then I remove the default screw lid and attach this tap instead. I lift the barrel onto a bench surface, lay it on its side and the tap easily dispenses water into my 2 litre bottle easily and efficiently.
TO THE EXTREME
Before I begin the actual Vinyl Cleaning Guide’s step-by-step sequence, allow me to say this. What you’re going to read below is cleaning to the extreme. Not to me but maybe to you. The amount of cleaning I do below might seem excessive but I do it because, of course, I can hear the difference. Otherwise I wouldn’t bother.
But look. Just because I wander towards the halls of madness, doesn’t mean that you have to follow me. You can reduce the actually amount of cleaning to suit you and the time you have available so look upon this section of the Vinyl Cleaning Guide as that only, a guide. Take what you want from it. You don’t have to copy the entire Vinyl Cleaning Guide step by step if you don’t want to. You will hear sonic improvements even if you only clean to a fraction of the level.
CLEANING YOUR VINYL – STEP BY STEP
1: Let’s address the Disco Antistat’s bath first. First rinse the bath with distilled water. Then we need to fill that bath with cleaning liquid. That will consist of a mixture of distilled water and alcohol, mixed together. To contain that mixture, we need to find a suitable bottle which is where one of the plastic spring water bottles comes into play.
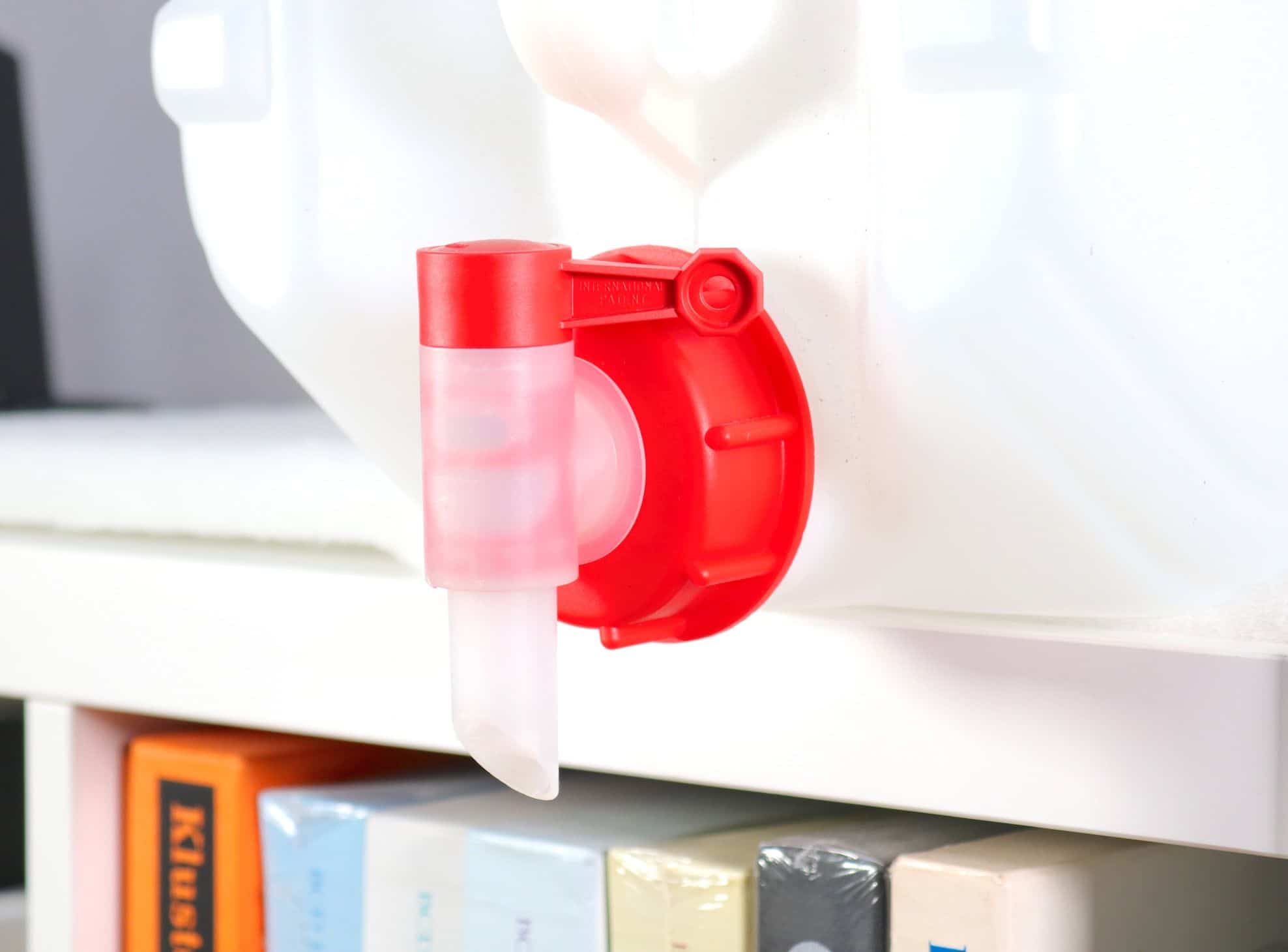
Before you use either bottle, give them both a good clean. Spring water contains impurities (in vinyl cleaning terms, at least) so add around a quarter to a third of the capacity with distilled water. Seal with its cap. Give it a thorough shake, empty that out and repeat twice more. Once done, the bottle is primed for use.
2: Fill your first bottle with distilled water.
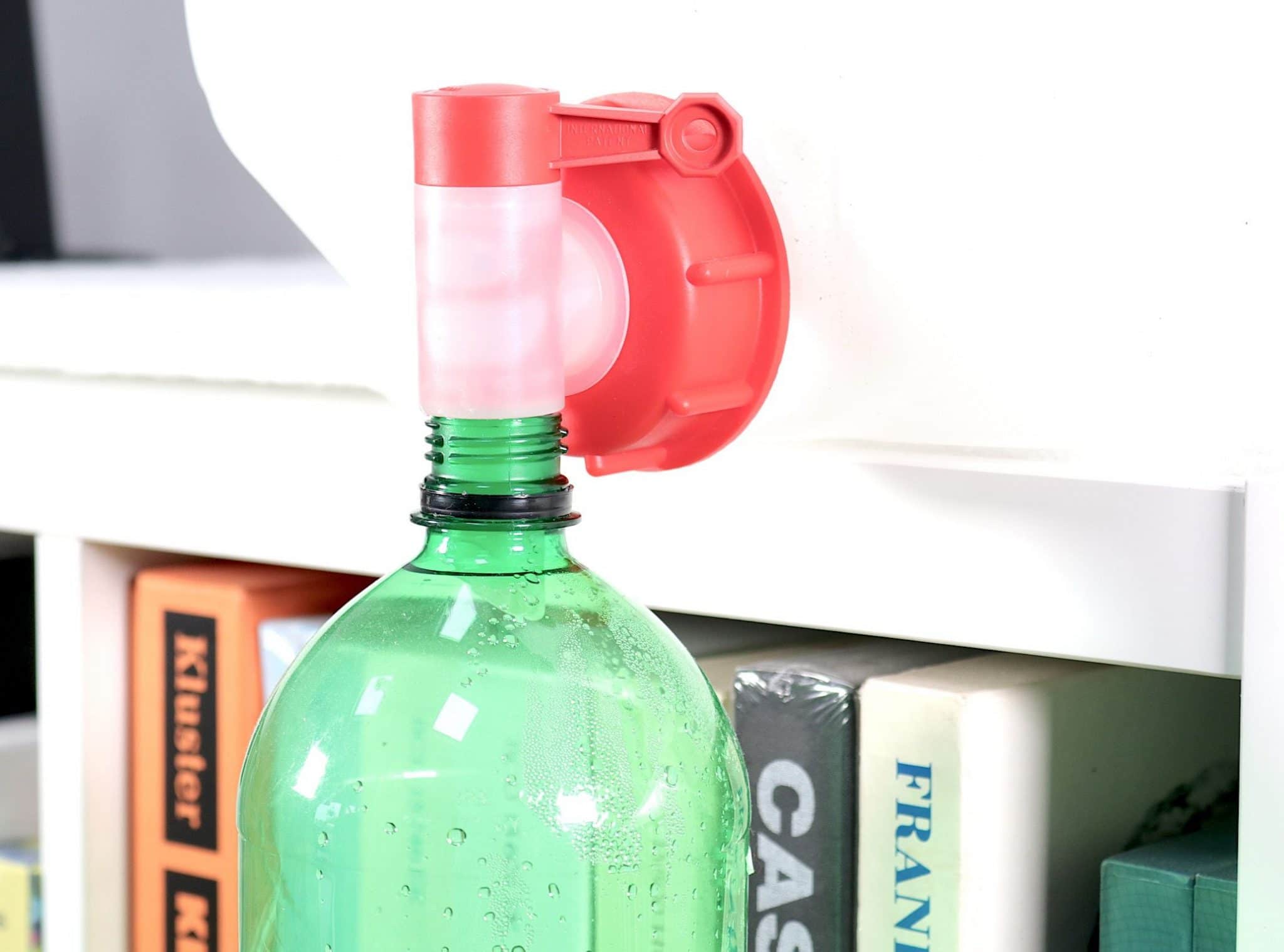
3: Add your alcohol. You need 7% of the capacity of the bottle. So, if you have a litre bottle, that’s 70ml of alcohol you need to add to the distilled water. Use a measuring tube for this task. Seal with a cap. Give that mixture a shake and you’re sorted.
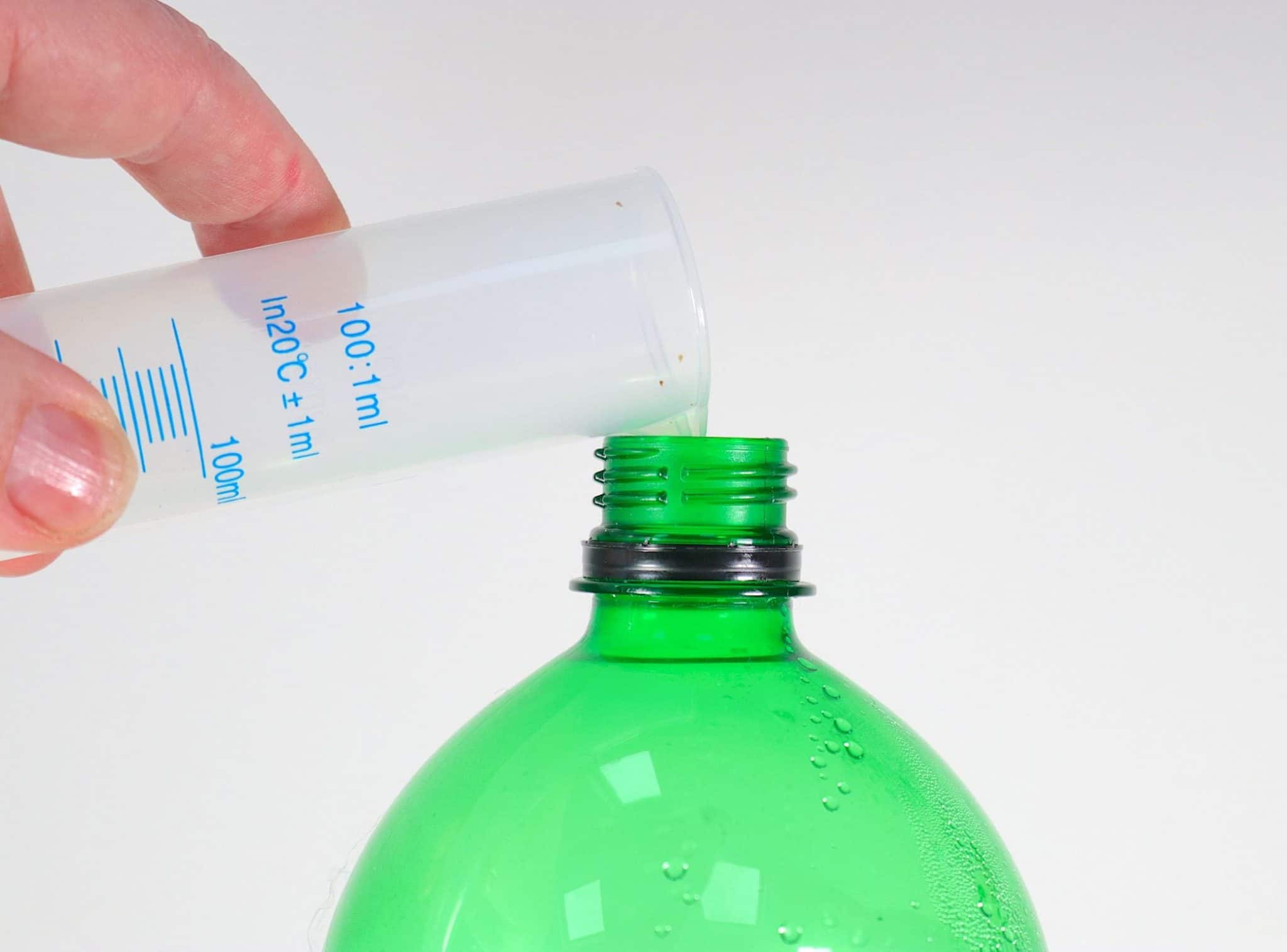
You only need 1% of alcohol to make a sonic difference but 7% is the figure of choice here because you also need to melt the Glycol off the vinyl surface.
Just 1% won’t be enough for the job. 7% will melt the Glycol but also perform cleaning in the groove.
The alcohol cleaning is a bit like brushing that pottery I mentioned above in the Abrasion section. Alcohol will effectively clean away the friable and easily removable grime.
Never apply alcohol directly to the vinyl surface, though. It’s too aggressive for that.
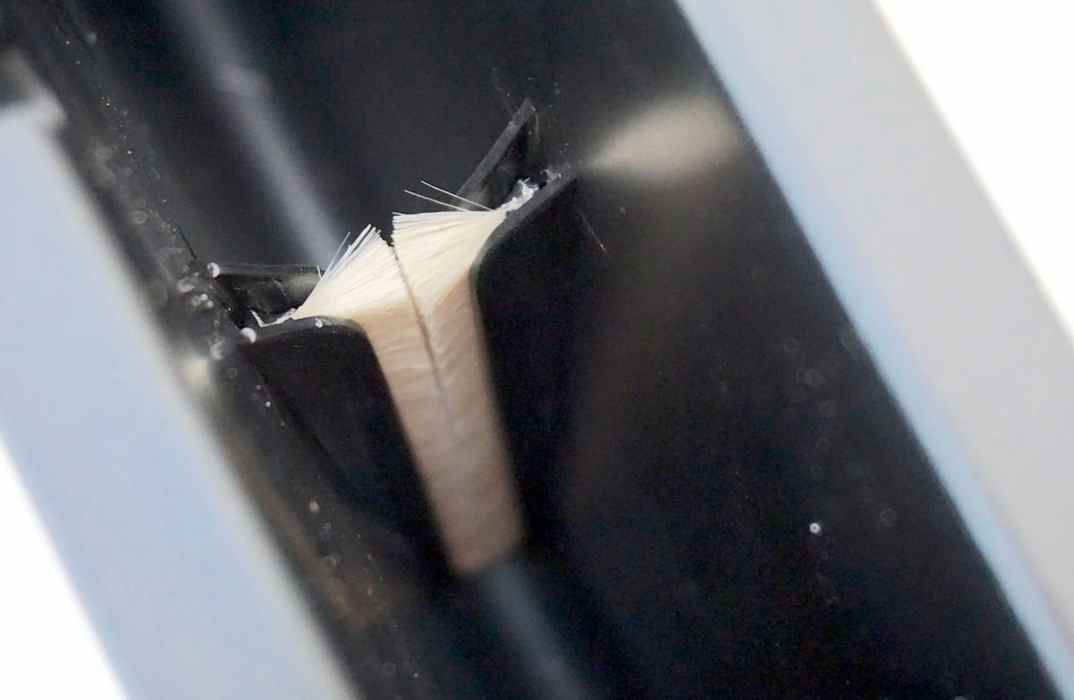
4: Fill the Disco Antistat’s bath with the water/alcohol mixture but stop just below the top of the fixed bath brushes. Just to be on the safe side, to avoid wetting the record labels. I know that the Disco Antistat’s clamps are designed to prevent that happening but, you never know and I’d rather be safe on this matter. By all means perform a dry run and vary the level for your record to make sure. OK, that’s the bath sorted. Now onto the vinyl itself.
5: Prime another spring water bottle. Fill that with distilled water.
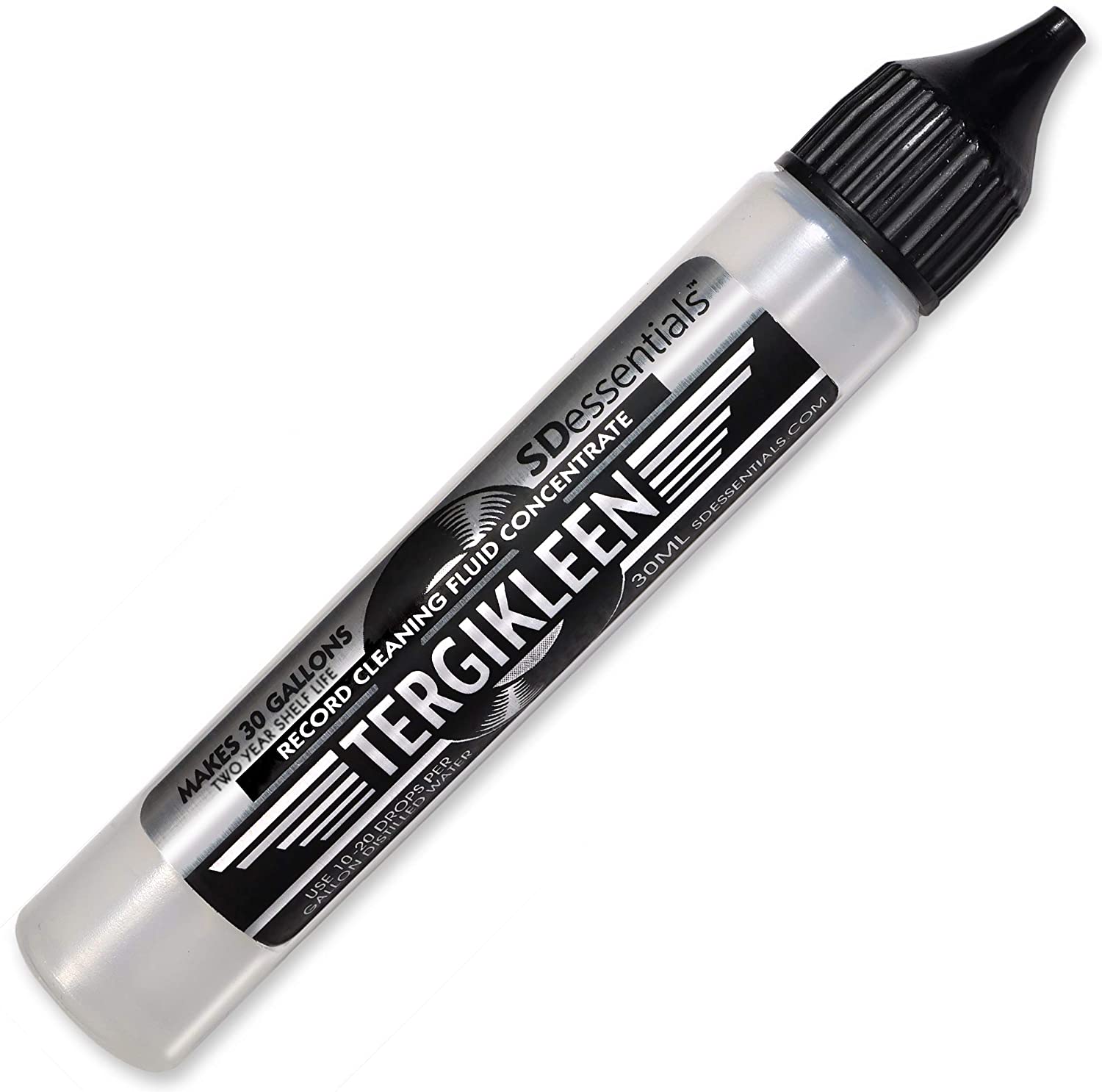
6: Take your surfactant and dilute it as directed using the included instructions. If you are using Tergikleen, I use 10 drops per litre. The drops are dispensed from the built-in dropper which offers micro-drops, smaller than the usual drops you might see from a pipette. So add 10 drops of Tergikleen per litre to the bottle of distilled water. Once applied, seal the bottle and shake for a while to mix thoroughly.
The surfactant is now ready to apply to the vinyl. The bottle is too big and cumbersome to try to move surfactant from there directly to the vinyl surface so you’re going to have to decant some of it to make the task more manageable.
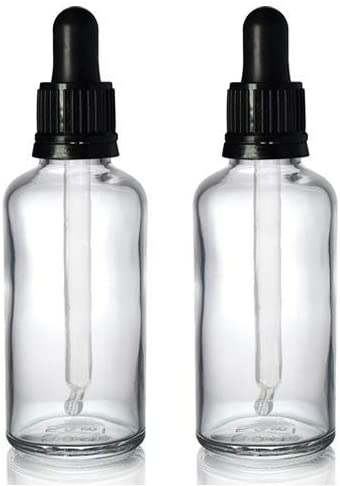
7: Fill one of the glass bottles (see image above) with Glycol. It’s easier to handle that way.
8: Before you decant the surfactant from the large, plastic spring water bottle into one of the small glass bottles take the vial from the Glycol bottle and fill it with Glycol. I say ‘fill it’ but you’ll find the vial will probably reach half way with Glycol (see mage below). Add that to the glass bottle. Repeat. You should have two vial’s worth of Glycol in your surfactant glass bottle. Fill the rest of the glass bottle with the diluted surfactant from you spring water bottle. Be careful not to spill the surfactant all over you floor. Do this over a sink and take your time. So you should now have two glasses bottles. One is filled only with Glycol. The second is now filled with surfactant and two vials of Glycol.
9: Seal the glass bottle filled with surfactant/Glycol and give it a good shake to mix thoroughly.
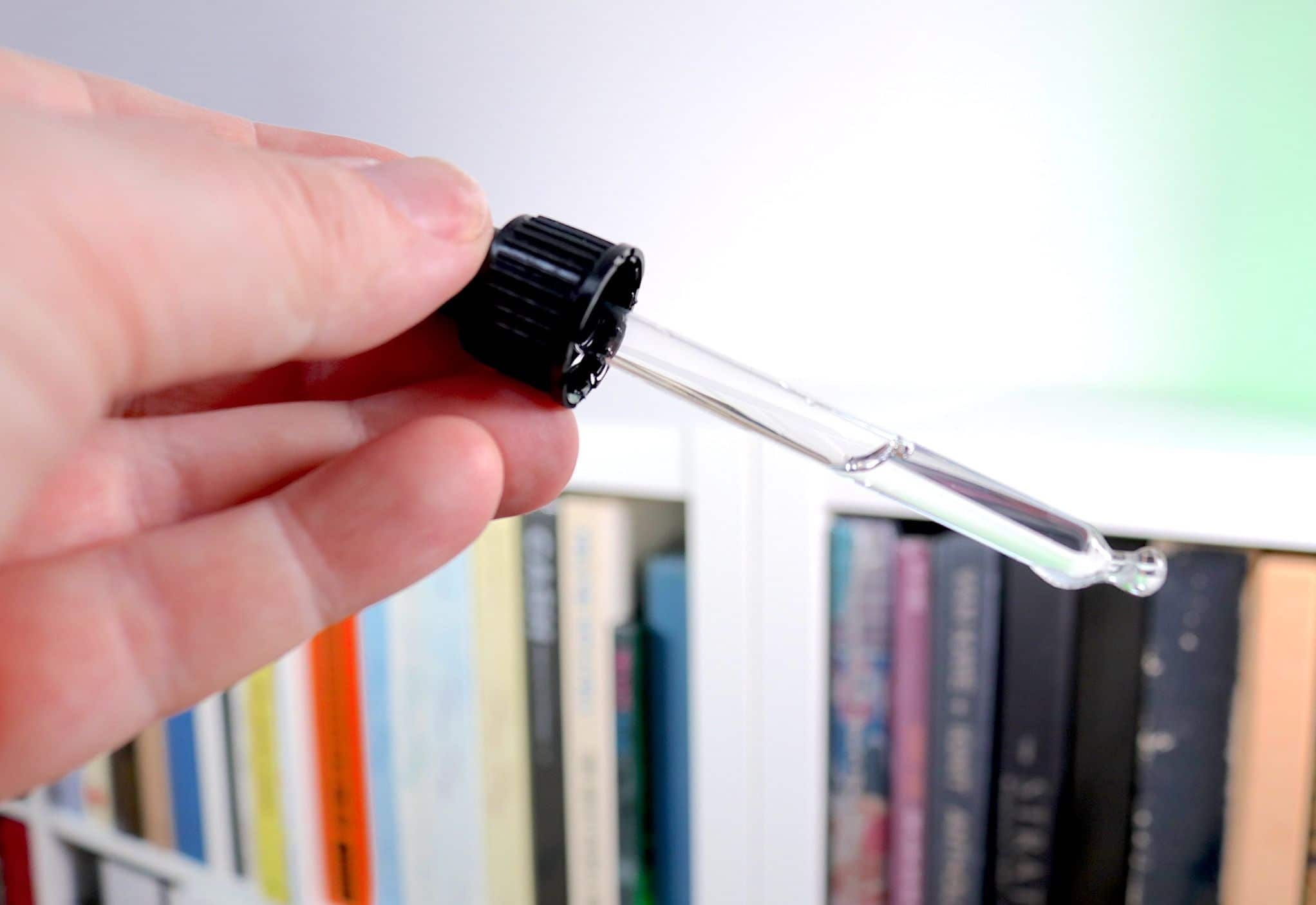
10: Now, take the glass bottle full of glycol/surfactant to your vinyl. Fill a vial with the mixture (again, it will be around half full (see image above).
You need to apply this mixture to the vinyl surface but you want an even spread of the liquid across the record’s surface. Hence, ‘draw’ a stripe of liquid, using the pipette from the inner edge of the run-off outwards to the edge of the record itself. In a straight line. Draw four lines. One at 12 o’clock another at 3 o’clock, then one at 6 and the final at 9 o’clock.
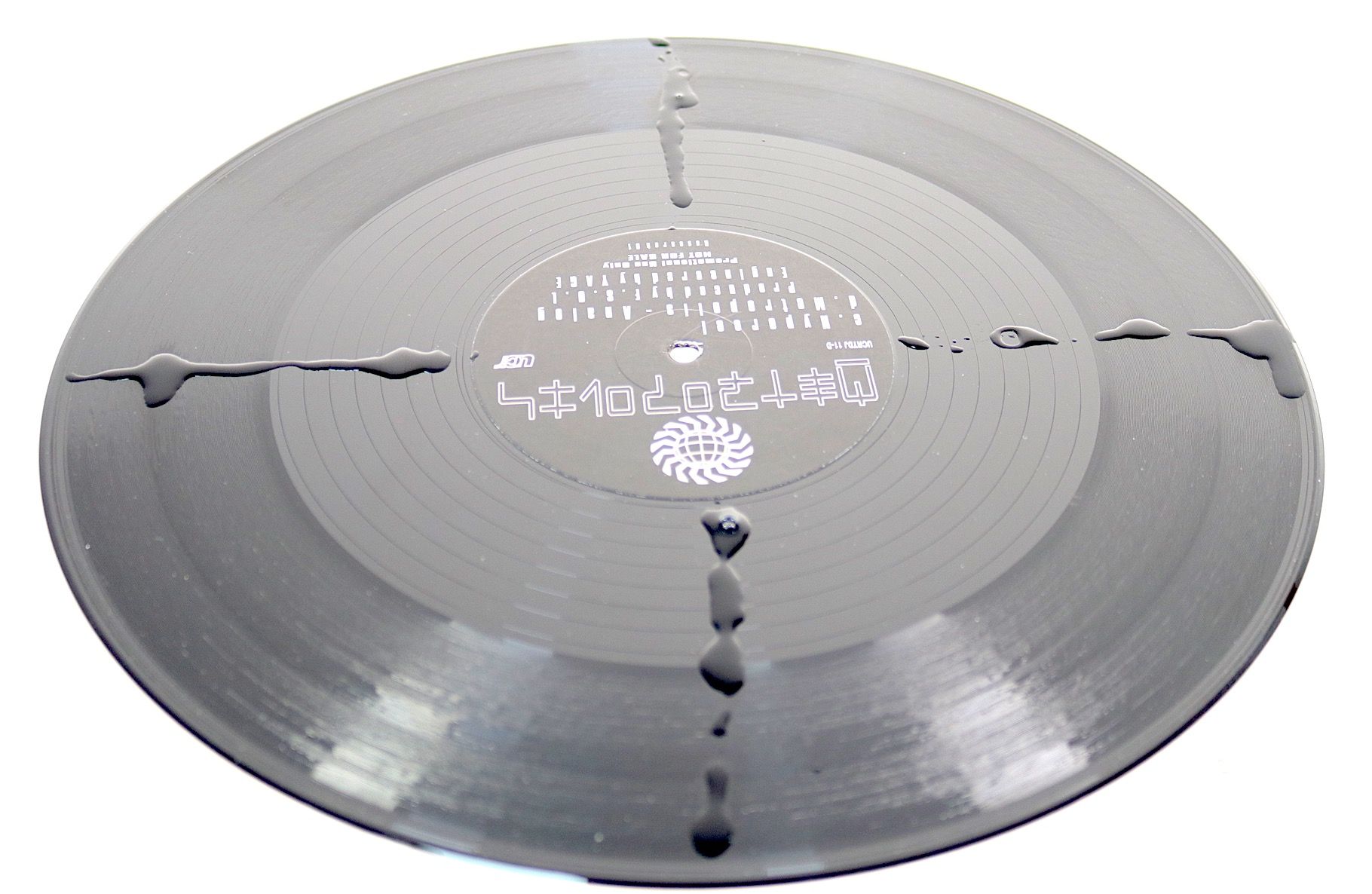
11: Take your Kabuki brush. Move the brush around the vinyl surface to evenly spread the surfactant. You don’t have to be too OCD about this. Don’t worry if there are dry spots after you do this. We’ll get to that next.
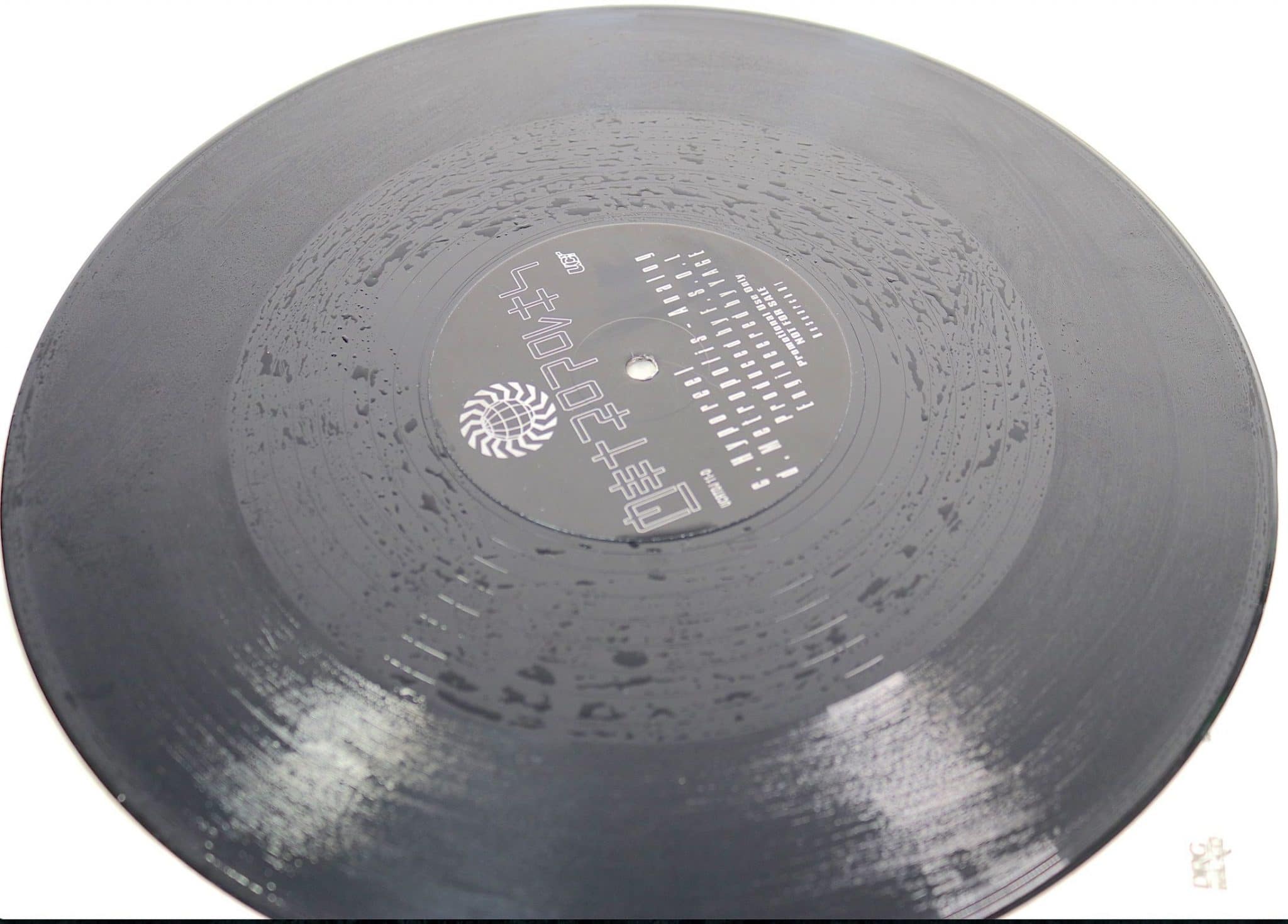
12: Holding the Kabuki brush move your fingers from the handle and down to the actual bristles themselves. The idea is to have around a centimetre of bristle sticking out from your fingers. Holding the majority of the bristles with your fingers, that’s the amount of visible bristle you should see. The remaining bristles will be quite stiff in nature now.
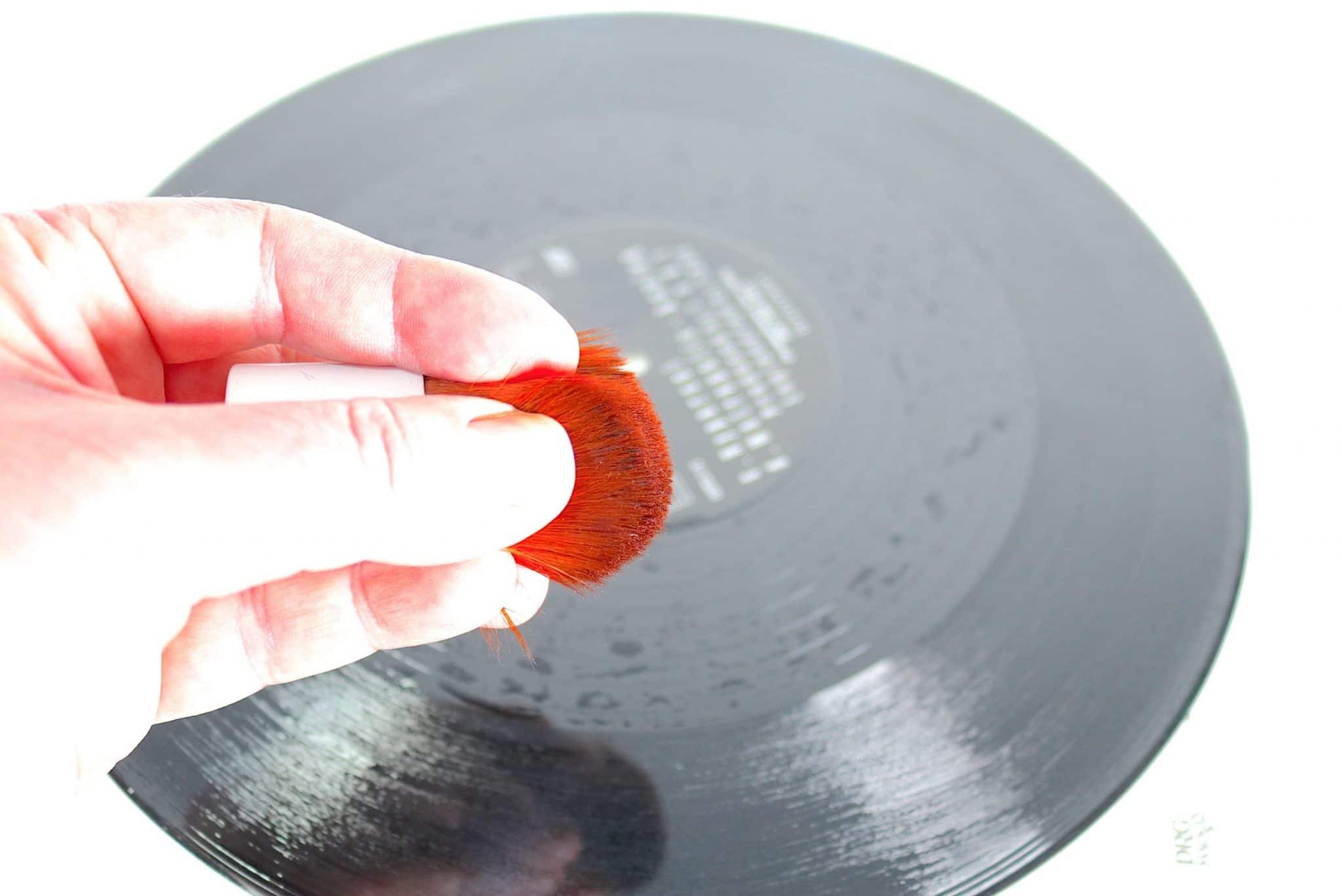
13: Using this stiff bristle, press the surfactant into the grooves in a spiral fashion working clockwise from the outer edge towards the centre and then anti-clockwise from the centre to the outer edge. That’s one side done.
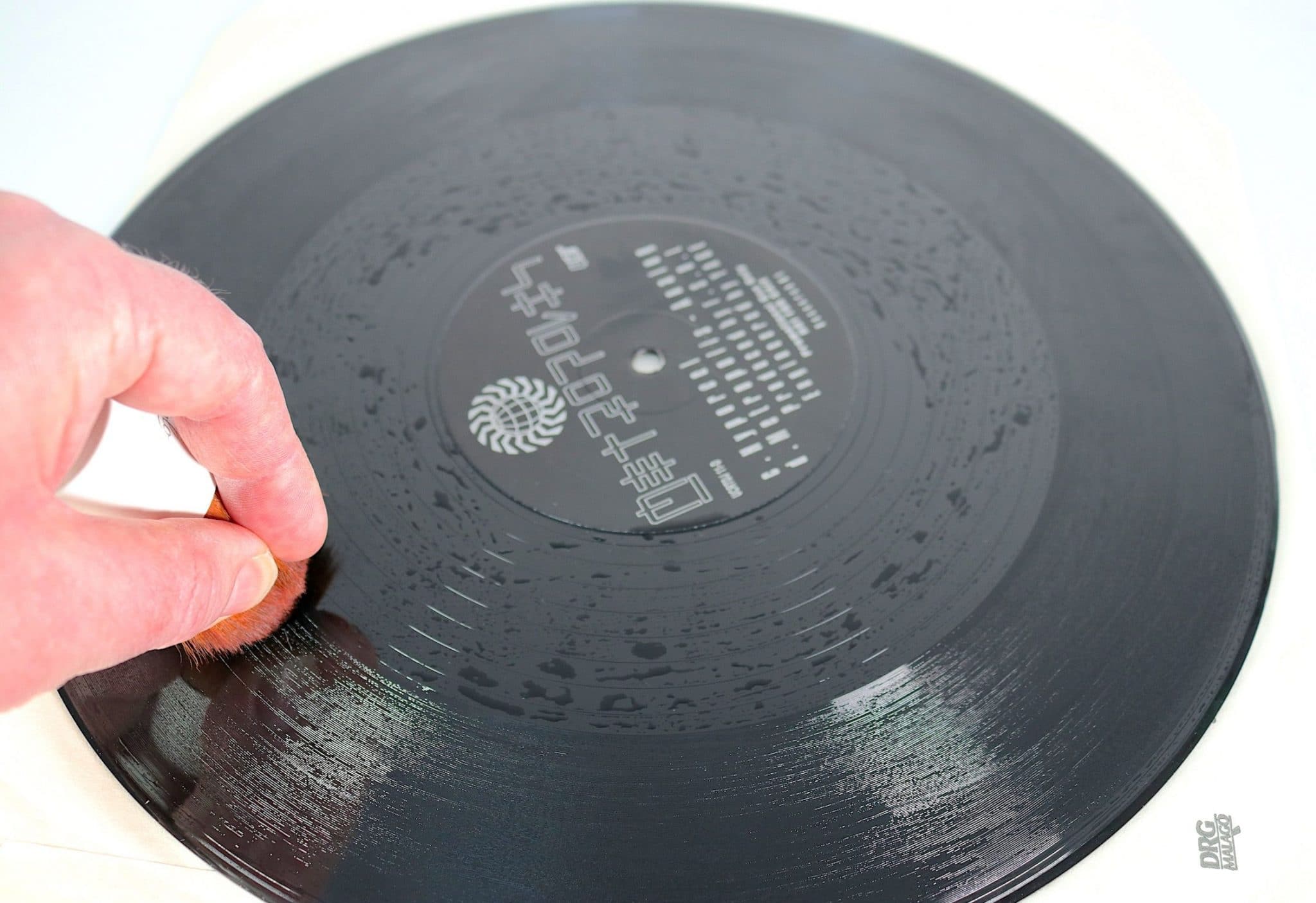
14: Repeat the whole process on the flip side of the record. Your record has now been prepared for cleaning.
15: Add the Disco Antistat clamps to the record as per the Disco’s own instructions and insert the clamped record into the Disco’s bath. Slowly rotate the record six times in a clockwise direction. Stop. Then rotate the record six times in a clockwise direction. Stop.
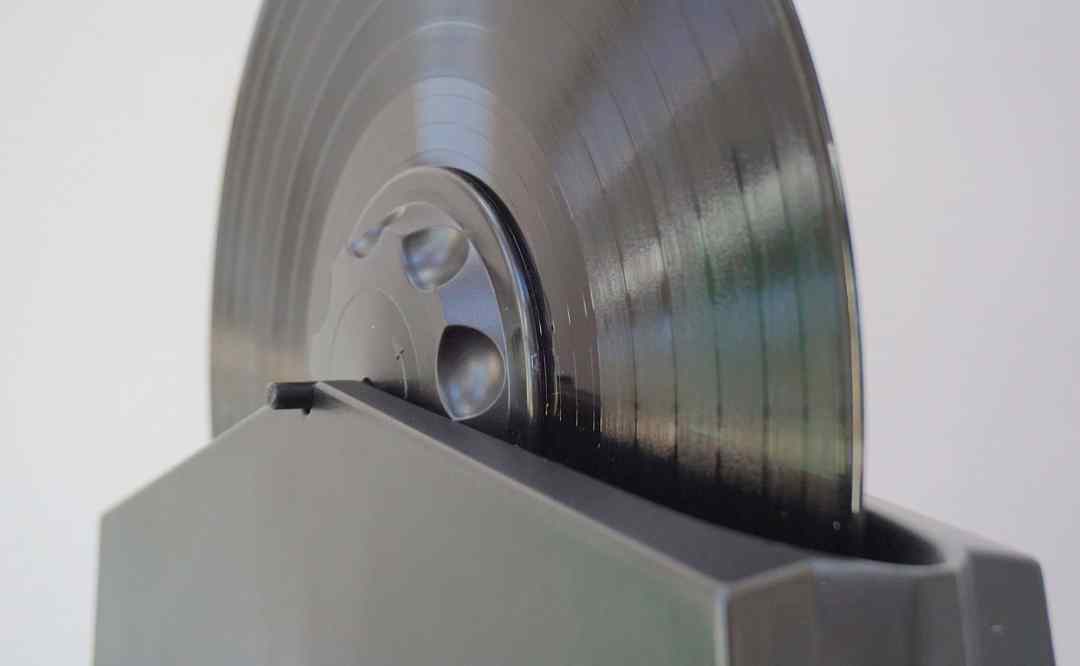
What is happening is this. The surfactant is allowing the liquid to get closer to the vinyl groove surface by breaking surface tension. Allowing for a deeper clean, if you will.
The Glycol is ensuring that the surfactant sticks to all of the grooves during this time to maintain an even clean.
The alcohol is cleaning the loose, friable material and more easily removable oils from the groove surface.
The abrasion is being applied by the built-in goat-hair brushes. The relatedly tough Disco brushes will help to break down the hardened oils and gunk I mentioned above.
The combination of these products and actions will produce an effective clean, noticeably improving sound quality.
16: Steps 10-15 are seen as a single ‘cycle’. The extreme bit for some is this. While one cycle takes long enough to achieve and will enhance sound quality and you can stop there if you wish, during tests, I found that more cycles applied to the same record improved sound quality. That is, the sound from a record sounded better after two cycles when compared to one. And with three cycles when compared to two. And so on.
I stopped – finally – at six cycles. This will take a long time. Over an hour for each record. I repeat, you don’t have to go there but I’m doomed because I’ve heard the differences so I can’t go back, I’m afraid. You decide how far you want to push it.
17: When the cleaning cycles are completed – however many that may be – then insert the record one final time but do not add any surfactant this time. Don’t add anything to the vinyl surface. Just add the record ‘as is’ and complete the same rotations clockwise and anti-clockwise. This is a rinse cycle to remove any lingering residue.
If you are able to buy a second Disco Antistat then perform the rinse cycle in the second unit. Keep the second unit for rising only with a bath filled with the same proportion of distilled water and alcohol. In this way, the Rinse bath will last longer before it has to be changed.
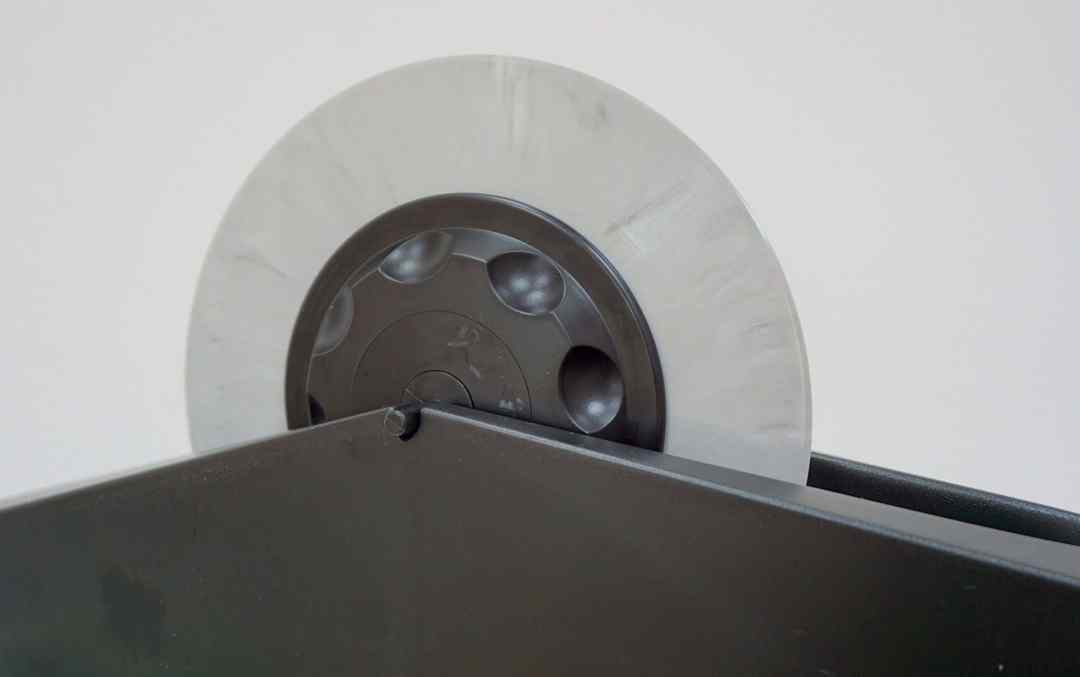
After a series of cleans, you may want to change the bath water for a fresh batch because the surfactant will slowly build up in it. I’ll leave that change over time up to you because it depends on how much surfactant you apply to the vinyl surface in the first place, the frequency of your cleaning and the amount of cycles you decide to run with.
18: Once the rinse has been completed, remove the record and the clamps and insert the record into the supplied drying rack for drying. A warm room will be more efficient.
CONCLUSION
And that’s it for this Vinyl Cleaning Guide, folks. I must add though that the above is a one-off intensive clean. You won’t have to do this every time you want to clean the same record. So don’t be concerned about that.
See this Vinyl Cleaning Guide above as a sort of ticket into your record collection. A test that any piece of vinyl has to run through before it earns the right to sit on your storage shelves.
Once a record has been through the above then you only need a maintenance clean whenever you feel it’s necessary. If it is, do one cycle only, when required.
If you have any questions about the above or if you need me to elaborate then, by all means, give me a shout in the Comments and I’ll help all I can.
I hope that this feature has helped in some way to improve your vinyl cleaning technique and, more importantly, the final sonic performance of your records. Next up? Cleaning with a vacuum-based record cleaning machine!
[Don’t forget to check out my Patreon Page at www.patreon.com/audiophileman, for exclusive postings and more!]
Hi Paul, thank you for your earlier reply in helping me get my glycol ratio right. I’m having revelatory results following your exact method with 2 disco-antistat stations.
I suspect some are having cleaning issues based on the quality of the distilled water they are using. I can only imagine the havoc that leaching chemicals from the plastic containers that distilled water is often sold in is bringing to your readers’ vinyl collections.
This is why I implore you to do some reviews on some of the commercially available water distilling machines on the market, from the budget bench-top machines up through those costing several thousand US dollars and occupying the better half of a standard garage bay. The only way you can truly gain control over the results of high end record cleaning is by having perfectly brewed, user-distilled water with contaminants measuring in the low parts-per-trillion.
I eagerly wait with tongue firmly planted in cheek for your upcoming review of this essential production component for our record cleaning frenzy.
Hi Ezra – glad I could be of help. As for your suggestion? Blimey, that would be taking my vinyl cleaning OCD leanings into a whole new padded cell 🙂
I have heard of such machines but haven’t used them. Some of them are not *that* expensive as you can see by the link here: https://waterdistillersdirect.co.uk
Even so, I haven’t gone down that particular rabbit hole. Partly because I wonder about the cost to value benefit for an audiophile and partly because the distilled water sources I’ve used have always been fine.
I tend to only target water suppliers who actively supply laboratories on a regular basis. As opposed to the chap who fills a bottle from the tap and uses an ink-jet printers to print a fancy label (Peckham Spring, anyone?)
The idea being, if these elite institutions found their water supply second rate, then they wouldn’t touch the said company with a barge pole.
Even so, now you’ve mentioned it…it’s got me thinking 🙂
Back in the days I was maintaining aquariums I used a home osmosis system. It doesn’t cost an arm or a leg and could be an option..
Randsom link :
https://www.amazon.fr/inversée-rendement-journalier-réservoir-nécessaire/dp/B073Q6N8NJ/ref=sr_1_10?adgrpid=55773078906&dchild=1&gclid=Cj0KCQiA0-6ABhDMARIsAFVdQv8bwpmCMiK8P0Bqs3unVn9ai6Sime4BVgxwLVN9m7117QciDO2xvvoaAnfeEALw_wcB&hvadid=275351160629&hvdev=c&hvlocphy=9056136&hvnetw=g&hvqmt=e&hvrand=16821854149993076645&hvtargid=kwd-1764763359&hydadcr=10736_1710814&keywords=osmoseur&qid=1612438970&sr=8-10&tag=googhydr0a8-21
Hi Paul,
When firmly inserting with the Kabuki brush the surfactant I see a greasy substance emerge, I can’t get that off. This also happens with new records.
Therefore my question, is there too much Glycol in the combo combination ratio OR am I using the wrong Glycol?
I am using Monopropylene Glycol:
http://www.lubrisolve.co.uk.
Despite rinsing for a long time afterwards I feel that the result is still not good.
You may either be adding too much Glycol or not enough alcohol. That is, if you are seeing the residue after cleaning. The prescribed ratios in the Guide have worked for me on numerous occasions without any residue.
Hi Paul, a great article, thank you.
I know Part2 and 3 are still yet to be published, but could I ask a question about this process in conjunction with my Audio Desk RCM.
Would you still use the Surfactant/Glycol mix before putting in the machine., and is the Audio Desk cleaning soloution appropriate to remove the glycol (as your alcohol mix does). I know it’s not recommended to use a different cleaning soloution in the Audio Desk.
Many thanks
Kevin
No worries, Kevin and yes – I’d still use the surfactant/Glycol/brush method before putting in your Audio Desk. The AD solution is good. Not great. But good. If Tergitol is first division, the AD solution is third division. But it does help, yes. And don’t forget, AD want you to spend money on their products. It’s an income stream for them. I’ve used plenty of other products – including alcohol – for, well what, a couple of years, without any issues. Your choice though and your responsibility (he says, covering his backside 🙂 )
Perfect, thanks Paul.
I’ll use up what I have left of the AD cleaner and thereafter I’ll go with your 1% alcohol mix.
Thanks Kevin
Hi Paul,
Have been cleaning a few records now I’ve got myself up and running. I’m cleaning most records with a surfactant brushing beforehand as per your guide. I’m generally finding that i’m getting better results on newer less crackly records in terms of improving the sound, as opposed to ‘cleaning up’ and old dusty record. Do you find similar in that this method is better at bringing out the best in a cleaner record rather than restoring an old really filthy, crackly one? I’m wondering if taking it to the full six steps on a crackly record would reduce this or if this method has limits in this area? (I don’t currently have access to an ultrasonic method of cleaning for comparison)
Also I’m finding that after air drying i’m getting marks where the slower evaporating water left, is this something you find too?
Both, Oscar to be honest. It would depend on the condition of your records, of course and the life they’ve lead. Some will need repeated cleans to get the baked off stuff out of the grooves. It’s like using elbow grease and a scourer on a kitchen surface: a few seconds rub might begin to remove the grime but you may need a full minute to remove it completely. It’s a rough metaphor but you get my meaning, I’m sure.
I also find that, after 6 complete cycles and a full rinse, if I still hear crackles and pops then I tend to assign that to groove damage.
I don’t see any marks, no. Again though, that might just be evidence of the grime being exhumed from the grooves. It depends what’s in there. Could be anything. Hey, I’d seen some people on YouTube ‘clean’ their vinyl with WD-40, which is basically natural gas condensates, petroleum distillates and the distillation of coal tar and peat plus kerosene and other oils. Imagine doing that, leaving it in there for 10 years so it goes hard and then trying to remove that stuff with a single cleaning cycle.
I’m not suggesting your LPs are covered in that but I am saying that second-hand LPs can be subject to bizarre cleaning methods before they arrive into your hands.
I would take each record on its own merits, especially if you have any second hand LPs.
Hey Paul,
Thanks for your reply. I’ll go down the elbow grease method for some of the more stubborn records and repeat as you suggest. I see what you mean about how caked different kind of nasty stuff can become, I am generally finding the issues to be on secondhand records yes so could be they’ve been through some interesting substance mixes before they got to me. I’ll keep on with the cycles and dream of a day I can afford a more professional solution!
With regards to the marks it is mainly noticeable on the run off, where the liquid has dried rather than evaporated (if that makes scientific sense). I just thought I’d mention it as I wondered if what I could see on the run off was actually all over the record but hidden in the grooves. That said the liquid does seem to be more conducive to drying off the grooves rather than the run off. Was wondering if anyone else has found this?
What you might be seeing is the alcohol holding grime in suspension on top of the record’s surface. The grime having been lifted from the groove but now having nowhere else to go. The latter then evaporates and then deposits the suspended ‘stuff’ onto the surface afterwards. The best solution for that particular issue would have been a vacuum-based cleaning machine which would have sucked the material away from the surface before the alcohol evaporated. Just my guess.
Paul, apologies but I just want to clarify I’m not using the AD as the Surfactant, I’m using the Triton X100 and then combining with the glycol.
If I continue this pre clean before using the Audio Desk, is the AD soloution in the RCM suitable to remove the glycol? Moving forwards would you recommended your alcohol soloution in the Audio Desk rather than their fluid (subject of course to my own risk :-).
You’ll only be able to remove the Glycol if you use alcohol in the bath. If that’s an issue, don’t use Glycol. I’ve done the A-B tests and alcohol in the bath, Glycol, etc is the better option. As you say though, at your own risk and all that 🙂
Thank you.
Hi Paul,
This is what you say: ‚Äú It doesn’t clean the record itself but allows your vinyl cleaning machinery and liquid to do a better job, because of preventing surface tension. It assists them‚Äù.
You make it appear that Tergikleen is just a surfactant to make the action of water and alcohol work better.
But Tergikleen itself indicates in their instructions how they use this agent exclusively to clean a vinyl record without distilled water and alcohol.
This application can be found everywhere on the web.
So I am still left with the following question:
What is the truth, the Tergikleen solution or your solution?
I hope you see my point.
You ultimately need to decide, Henk. I’ve already stated my case based on my own tests. I’ve done my bit. Now it’s your turn. If my system works for you, that’s all that matters. Then enjoy your music. If it doesn’t, then find another system.
To address your point directly, Tergikleen should not be used ‘neat’ on vinyl, in my opinion or the opinion of the suppliers for that matter, if that’s what you’re implying. You need to dilute it with distilled water.
And I don’t ally alcohol with Tergikleen. They are not dependant upon one another. Alcohol is part of the larger cleaning process. It doesn’t have to work with Tergikleen. I have found alcohol to improve the overall cleaning process.
And sure, you can use any substance you want to clean records. Tergikleen on its own, washing up liquid, WD40, crude oil and sulphuric acid – whatever you fancy. I wouldn’t personally recommend it, though.
As for “truth”? What I’m giving you is my truth. The results of my own research. As I said in my earlier reply, it’s up to you if you want to follow the system. You really don’t have to, Henk. You can use my system as a launching pad for your own system if you so wish or you can ignore it altogether. Ultimately, it’s all about choice. All I’m offering you is the result of my own extensive, multi-year research.
Dear All,
Thanks to Paul’s investigations, my Audiodesk RCM now delivers stellar sonic performance. I follow almost all his suggestions, incl. the use of diluted Tergikleen applied directly to the vinyl surface. I do not use glycol. There are many much cheaper ultrasonic RCMs on the market than the Audiodesk which probably yield similar results but might not offer the ultimate convenience. When properly used, as per Paul‚Äôs recommendations, ultrasonic RCMs DO DELIVER. They are a game-changer.
It is therefore with much bitterness that I want to share with the vinyl community my experience with Ortofon, the Danish world-leader in cartridge manufacture. I just sent Ortofon the attached letter.
The Demise of a God
Neither Wagner nor Shakespeare. But still Danish.
Two years ago, my official Ortofon dealer convinced me to buy an Ortofon MC Century cartridge. There was no chance to audition the cartridge, but my dealer assured me it would be a major upgrade from my Ortofon MC Anna cartridge. I have been an Ortofon fan all my life, slowly moving up the food chain of Ortofon cartridges. The investment and risk were considerable, but the MC Century would be the culmination of my lifelong loyalty to the brand. Empathy played a considerable role in the decision.
The upgrade was disappointing. The Century improved on the Anna in the lower registers but at the cost of an incisiveness reminiscent of digital playback. Detail at the cost of musicality. Over the course of the next 2 years, my dealer reset the cartridge/ arm combination a number of times, because I kept complaining that it did not deliver on its promise. To no avail.
Finally, after more than 300 hrs play-back (closer to 500 hrs by my estimation), the Century revealed its true character. At long last, the Century delivered on its promise: thunderous but always musically accurate bass, life-like mids, soaring highs and an expansive and wholly coherent sound stage.
A few months later, early January 2021, and quite suddenly, it died. The cartridge would no longer track. My dealer rushed it to Ortofon. They had long exchanges. I highlight the most notorious ones (my highlights).
Feb 12th, 2021,
The cartridge has a lot of dust that has almost cemented to the cartridge and you can also see that the cartridge has a bit of rust on the bottom.
Best regards / Med venlig hilsen
Anders Bentley
Sales Department
Feb 17th, 2021,
The diagnostics made by our operator sounds like our recommendations for stylus and record care have not been observed, and that is how it had happened. The physical condition of the cartridge doesn’t align with the story customer has told, whilst we only rely on facts.
To avoid it would happen again, I’d recommend refer to our HiFi FAQ, p.1 Stylus and record care here https://www.ortofon.com/support/support-hifi/faq-installation/, very shortly:
1. Remove dust carefully from record surfaces by using Ortofon antistatic Record brush before every use.
2. Use Ortofon Stylus fiber brush a few times along the cantilever in the direction of the stylus tip, whenever you play a new record or change sides.
Ortofon do not recommend the use of solvents of any kind for cleaning of either record surface or stylus
Best regards/Med venlig hilsen
Katarina H. Nielsen
Technical support Web Marketing
Unbelievably, these are the very words of Ortofon.
It is obvious from Bentley’s remarks that there was a serious quality control issue at Ortofon when my cartridge (nr 16) was assembled.
Rust? Rust!
Cemented dust? Cemented!
I live uphill in a cork dry climate (Greece). I religiously clean all my records in a Glass Audiodesk RCM before their first spin, always use a microfiber brush to remove dust from any record before playing, and apply a Furutech DeStat-3 before lowering the diamond into the groove. Besides, during almost 50 years of playing vinyl almost exclusively with Ortofon cartridges, I NEVER had ANY issue, let alone with either rust of cement.
Obviously, the rusted(!) part was rusted “ab initio”. And probably contaminated during manufacture with some cutting or hydraulic oil. Which in turn contaminated the cantilever and attracted/ attached the dust, which turned to “cement”. Or some variation of the above. Ortofon itself identified and recognized the problem! It sent a microscope picture illustrating the issue. But then Ortofon went Hamlet-crazy.
According to Ortofon, the condition of the cartridge does not align with the “story” (?!) customer has told. Obviously, the customer and the Ortofon-dealer connived to deliberately rust and cement the cartridge. My official Ortofon-dealer and myself are liars.
These are the “facts” and here is the “proof”: the customer uses a Glass Audiodesk RCM (which uses water as a solvent, but then thoroughly dries the record). By the way, the use of any “solvent”-based record cleaner invalidates the warranty! And this, unashamedly, by the world’s leading manufacturer of cartridges!
Ortofon dismisses the self-evident explanation ‚Äì its own glaring shortcoming – to go on a rant against its most loyal customers. Ortofon devises a crime involving customer and dealer. It throws credibility out of the window.
A crime needs:
1. a victim: the cartridge
2. a motive: why would 2 Ortofon loyalists make up a story? One is its official dealer for 30 years, the other a loyal customer for 50 years, both with an impeccable track-record
3. a weapon: how did the suspects manage to “rust” a cartridge? And in such short time! To cement dust to the cantilever? If the use of an ultrasonic vinyl-cleaner or other “solvent” vinyl cleaner rusts cartridges or cements dust, the WHOLE vinyl-community, incl manufacturers of all feather, should put Ortofon in its place: stop the b*s*!
4. a causality: absent motive and weapon, there is no causality.
If we apply the above fact-based reasoning to Ortofon, only one conclusion imposes itself: guilty!
The God has fallen off his pedestal.
What would I like to achieve with this letter?
1. an apology: Ortofon has no idea how hurtful its baseless allegations are; it seems to have lost track of its mission, which is to provide musical enjoyment to its customers and revenue to its dealers. Instead, it is content to insult them.
2. a redress: Ortofon repairs or replaces the MC Century at its own cost and provides a 5-year warranty, independently of the customer’s use of a vinyl-cleaner.
3. a warning: it is impossible for a customer to check in-depth a piece of brand new HiFi when he buys it; if defects are present, they might appear with time; a customer must then rely on the reputation of the vendor for a reasonable outcome; in fact, in such cases, HiFi enthusiasts rely solely on the manufacturer’s reputation. Ortofon failed the test ignominiously. I can only hope that the vinyl-community, led by its most trustworthy opinion-makers, puts the company in its place. Otherwise, any Ortofon customer will fall prey to the company’s predatory practices. Any problem with an Ortofon Blue? Your fault: only use blue vinyl. Ortofon Ti? You “rusted” it. Ortofon Wood? You “rotted” it.
The rot is elsewhere. In Denmark.
Hi Paul – here’s an update on my cleaning process based on your guide which may be of interest to your readers. I use the 2nd Generation Disco-Antistat (white tub with the record clamp with the handle on the spindle) and I have a second tub/brush (w/o other kit accessories) for clean rinse tub. I’ve been following your exact process above with WONDERFUL results on records that I’ve purchased new and used from roughly 1977 through the day before yesterday.
Here are two things that I’ve added that make my process easier:
1. I hacksawed the turning handle (which I found useless and flimsy for actually spinning the lp – easier to spin with the edge of the record) on the record clamp to shorten it so that its within the circumference of the record clamp. By shortening the length of that handle, the record clamp fits PERFECTLY in the opening of a standard US plastic pint or quart container of take-away Chinese soup with the lip of the container safely resting in the dead-wax. This allows me to rest the lp/clamp on the soup container on my workbench to apply the tergikleen/glycol solution then flip and repeat for side two. The now stubby arm, when the record clamp/lp is placed in my disco-antistat, serves as a reference (like a clock hand) for me to easily count my rotations. (Version 1 disco-antistat clamps won’t have this handy feature but the clamp should fit as neatly inside the Chinese soup container for applying solution.)
2. I added an inexpensive ($149US) vacuum-based KAB EV-1 RCM to my process. Attached to my home vacuum, it quickly suctions off rinse solution from my LPs so that I can get back right away to doing 2nd,3rd,4th,etc, repeats of the process without having to wait around for the air to dry my vinyl. Not a necessary piece of kit, but for doing volume record cleaning with multiple passes of your process in less time – this has been a game changer for me.
While my wife was initially suspect of what she thought was my meth-lab in the basement, she too now hears the differences in fidelity and our new late-stage pandemic post-dinner routine includes many wonderful hours in front of the hi-fi! Life is good with clean records!!
Hi Ezra,”By shortening the length of that handle, the record clamp fits PERFECTLY in the opening of a standard US plastic pint or quart container of take-away Chinese soup with the lip of the container safely resting in the dead-wax. This allows me to rest the lp/clamp on the soup container on my workbench to apply the tergikleen/glycol solution then flip and repeat for side two. The now stubby arm, when the record clamp/lp is placed in my disco-antistat, serves as a reference (like a clock hand) for me to easily count my rotations. (Version 1 disco-antistat clamps won‚Äôt have this handy feature but the clamp should fit as neatly inside the Chinese soup container for applying solution.)”
That sounds good. Can you explain it more maybe with an image?
Thanks, Henk
After 5 different washing sessions and approximately 50 records cleaned, I thought it could be useful to share my experience so far.
First of, thank you very much Paul: I am new to ‚Äúthe vinyl side of the moon‚Äù in our hobby but I read so many articles about vinyl cleaning and they all seemed weird to me. Everyone claiming ‚Äútheir recipe is the perfect one‚Äù, but no hint on…why is that?
On the contrary, beyond the personal esteem, you convinced me because of the explanation: the background checks, the ‚Äújourney‚Äù you‚Äôve been through…a nice mix of science, theoretical research and practical experience. Not just an opinion, but facts.
…well, no, you did not convince me to go for the 6 cleaning cycles, that‚Äôs way too much for me.
Second: for anyone with no previous experience like me and wondering if this is worth it… I will not use all the nuances in Paul‚Äôs descriptions so I‚Äôll state it as simple and clear as possible: if you ever experienced the sound improvement you get from the newer stylus after removing your worn out one or the improvement after getting the right impedance/capacitance match in your pre-phono when you install a new cartridge…well that‚Äôs the level of improvement you‚Äòll get by properly washing your old records!
It’s as simple (and immediate) as that.
Now, my (little) experience so far, for whomever may find it useful.
1) Don’t throw that ugly mug away!
I received a porcellane ‚ÄúChristmas milk cup‚Äù from someone who ran short of ideas last Christmas and doesn‚Äôt know I don‚Äôt drink hot milk nor pour biscuits in it…well, that mug is heavy and stable and the size perfectly fits the outside part of the Knosti clamp, so I now use it as a stand for my records, clamps on tight, while going through the surfactant/glicol routine.
Much better than my early attempts keeping the record in one hand!
2) Save money from the measuring pipe.
At the end of the day you will never need the whole set, and here in Italy they are pricey…the measuring cup of any medical syrup for your kids‚Äô cough would do the job just fine, you just need to refill it multiple times depending on the target bottle size for the water/alcohol mix.
3) Beware the kabuki!
Although I went for a “professional” brush from a local make-up shop, the first one I used was easily losing its hair, which may eventually damage the record. You may want to try multiple (not cheap) ones.
4) Experiment with less relevant records in your collection and be gentle with the brush.
I was mislead by Paul’s words about attrition and his description about keeping the “brush-end stiff” and to “push the mix in the grooves” and I probably pushed too hard. The outcome was I ruined a few records (in old records some tracks would skip where they did not use to, in new records I would hear noise and distortion where the sound was pristine before).
That was a tough moment and I thought to give up…but I eventually kept on and just realized that given it could have not been due to the knosti itself (they would have not been in business for decades otherwise!) it had to be me.
I managed to just distribute the surfactant on the record surface and leave the “friction” part of the job to the Knosti: it then worked brilliantly.
Please note, this is a key aspect, given this part of the process is still needed even with higher tech approaches to cleaning, as Paul just stated in his Degritte video…
5) How much time do you want to invest?
I trusted Paul’s words about multiple washing cycles being better than just one, but this whole process is so time consuming (although very rewarding, as I said earlier) that there must be a trade-off.
I eventually decided to “stop in the middle” after three complete cycles, then a rinse without surfactant/glicol and an additional rinse in a separate bath: at the end of the day the first bath is the one where surfactants and glicol get diluited from previous cycles so better go for a “pure” water/alcohol rinse for the last one.
This is where I got the level of improvement I described earlier.
For three full cycles and two rinses I still need 3 hours to complete a Knosti rack of records (7 records).
Well, these were my two cents.
I hope they can be useful to someone.
Regards
Thanks for the comments, Saverio.
For the benefit of anyone else reading this, I strongly doubt that the Kabuki brush is causing skipping. Unless the bristles are tipped with metal or something completely weird. Kabukis are incredibly soft, stiffening the bristles only helps to push the liquid into the grooves. The bristles remain soft as a baby’s what not.
I’m glad that you’ve adapted the system I presented and found a cleaning regime that fits you and your vinyl. Nice one.