The Article
AUDIO DESK GO ULTRASONIC: it’s forever blowing bubbles
28th October 2016
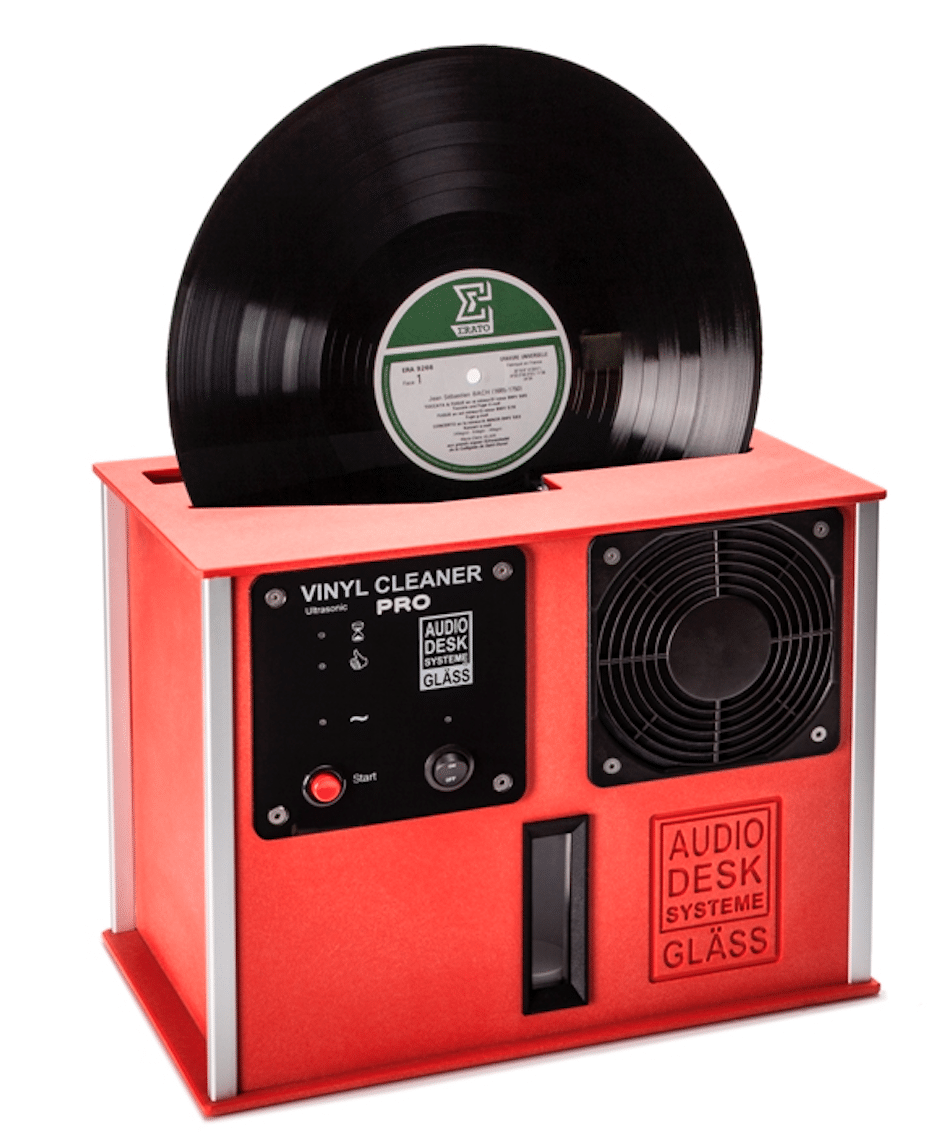
Ultrasonics is an increasingly popular method of cleaning vinyl records. Paul Rigby reviews Audio Desk’s Ultrasonic Pro Vinyl Cleaner
I had heard much about the ultrasonic methods of cleaning vinyl and was aware of some of the very expensive ultrasonic cleaners currently occupying the market such as the model offered by KL Audio for around £4,400 (in addition to one or two rather cheaper, Heath Robinson constructions at the other end of the scale). Up to this point, I must admit that I have had my doubts about ultrasonics and the technology’s capabilities when it came to vinyl cleaning but then became aware of the German, Audio Desk model designed by Rainer Gläss. As my curiosity was peaked and because I realised that I could now fully investigate such a cleaner for myself, I couldn’t wait to grab one for review.
Once I had committed to the review, I undertook more extensive research and was astounded at just how widespread ultrasonics is in various industries. Ultrasonic cleaners come in all shapes and sizes. Some of them are very large indeed and can be used to clean complex pieces of machinery. Others are small and are used to clean circuit boards or are even used in the medical profession. The most popular use that you might have heard of is ultrasonic’s ability to successfully clean a piece of jewellery.
Before you progress down this review, I wanted you to see the process in action in more general, non-vinyl, terms. To emphasise the fact that this is not a hi-fi techie/geeky toy. It’s a real world, very serious, very effective, process. You can see the procedure in action right HERE cleaning a car part (it’s a brief silent video). If you want a slightly more in-depth and complex demonstration, try the video HERE. This video/audio explanation of the process is targeted at industry but it provides a useful, six and a half minute or so technical primer.
What Audiodesk appears to have done here is to provide a fully automatic machine that cleans both sides of your vinyl disc simultaneously, using ultrasonics in a compact and solidly built chassis. The build itself is not of the Rolls Royce quality (to keep both weight and costs down, you won’t find steel chassis parts here, for example) but it remains strong and compact.
In use, the cleaner holds the vinyl record vertically within in a vat of Audiodesk’s own cleaning liquid. So, you slip a record into the central top slot which securely holds the vinyl. Once you turn on the power switch, a side-mounted red button is pressed. You can press to hear one beep for one cleaning cycle, up to five beeps for five cleaning cycles. Whereupon the record rotates (I found that the record sometimes – not all of the time – needed a quick press or anti-clockwise tweak in order for the internal rollers to ‘catch’ the disc to rotate it.) If you look down into the cavity, you will see it automatically fill with the supplied and pre-added liquid (which has been created by Audiodesk to a ‘secret’ recipe). As the record begins to rotate, four micro-fibre rollers (which need to be replaced after 500-1,000 LP cleans at £49 for four) swing onto the surface of the disc and rotate. The rollers spread the liquid over the record.
Once the record is wet (the label is left untouched, incidentally), the ultrasonic action begins, producing compression waves that produces millions of tiny bubbles that compress and break up, causing cavitation, the creation of tiny bubble explosions, directed liquid that is fired and forced into the grooves. The agitation effect displaces gunk, grease, muck and other contaminants which is then drained through a washable filter (which sits in the outer slot you can see in the images) whereupon a fan dries the still rotating vinyl LP (12”-only records need apply: you cannot use 10” or 7” discs here). If there’s any liquid still on the disc (an occasional occurance), you can repeat the drying process.
The typical five to six-minute cycle is not a silent one, especially during drying but there is not a great deal of excessive noise here. We’re not talking screaming vacuum cleaner-like levels.
Around 100 discs can be cleaned via one batch of cleaning liquid (a concentrate that is added to distilled water), whereupon a drain outlet at the rear enables evacuation of the same, you can then rinse the machine with warm water and then new liquid can be added at £12 per bottle (two bottles are provided ‘free’, initially).
SOUND QUALITY
I chose the original fifties recording of The Four Freshman Again! and the track Baltimore Oriole: a ballad featuring a solo voice, slow strumming guitar, upright bass and occasional backing vocal. Apart from a few very minor ticks here and there, this was a pretty immaculate record although is is an aged record and has seen a bit of life, as it where. Yet one clean with the Audio Desk revealed a wealth of new detail. A veil was removed from the soundstage, exposing a host of a new details including a subtle throat swallow from the lead vocal, a more precise and focused vocal presentation, more air around the guitar and bass and a removal of the upper midrange forwardness during backing vocal crescendos.
Listening to the original 1969 Motown master of Joe Harnell’s instrumental piano version of Stevie Wonder’s My Cherie Amour, complete with full orchestra backing including strings, the Audio Desk treatment gave the piano added dynamic range while adding an open and expansive presentation to this central instrument. The backing orchestra was also far more complex. A saxophone could be clearly heard for the first time, strings ‘swept’ instead of ‘barked’ with the percussion offered complex cymbal and rimshot work and no longer sounded like the shutting of a car door. Finally, secondary percussion tambourines offered a new brassy sound to their strikes.
More importantly was a head-to-head with my prized Loricraft PRC-3SE record cleaning machine in conjunction with L’Art du Son, the best cleaning liquid I have found on the market, thus far. I cleaned The Police’s Ghost in the Machine LP with this liquid, five times on the Loricraft (to reach a sort of cleaning plateau: sound quality wasn’t going to get any better, put it that way), listened extensively to the LP and then cleaned again with the Audio Desk. While the Loricraft stripped away a significant veil to reveal new sonic details the Audio Desk removed an additional layer to improve sound quality still further. The soundstage was stretched left and right and filled with more detail: vocals especially but also the synth backing. Percussion was richer and more characterful while any small hints of blooming and edgy forwardness on the vocal crescendos were removed and treble-infused cymbals sounded brassier.
The Audio Desk, let’s not forget, is about £1,000 more than the Loricraft (a system that I still highly respect, for the price, despite the Audio Desk’s performance: the latter still retains a revered cleaning technology process) but I previously didn’t believe that ultrasonic technology was capable of such sonic improvements…at any price. Frankly, I was stunned.
LIQUID TESTING
To isolate what bits of the cleaning machine were doing what, I decided to test the cleaning liquid, on its own, using the known reference, my Loricraft RCM, as a cleaner to compare the liquid with my reference L’Art Du Son. To do this, I took an original copy of David Bowie’s 1974 LP, Diamond Dogs and cleaned that with L’Art du Son liquid five times. In this way, any incremental cleaning improvements will have peaked and plateaued. I then listened and cleaned the same LP with the Audiodesk liquid once. I tested the title track specifically, a dynamic and raucous affair.
Was their an improvement? Absolutely! I was sure that this LP suffered from a measure of compression but that effect was removed with the Audio Desk’s liquid treatment. Bowie’s voice was now smooth and open while an accompanying guitar – that was supposed to be distorted and compressed – now popped out of the mix. Cowbell percussion had a more metallic ring as did the treble via cymbal crashes. The rhythm guitar was more recognisable and characterful but, more than that, seemed to extend further to the right of the soundstage. Bowie’s own work on the saxophone was tonally more interesting, textural and offered a greater degree of information.
TAKE FIVE
I then cleaned the LP on the Loricraft an addition four times and listened to that to remove the Audiodesk liquid out of the equation. Remember, by now, this one LP had undergone 10 individual cleans using two different liquid treatments on the Loricraft. Surely, by now, nothing more could be done in terms of sonic improvement?
After one cleaning rotation, I replayed the same track and, amazingly enough, heard further improvements. Another veil had been removed from the soundstage which now extended backwards, giving a 3D effect while sounding far more complex and multi-layered. The reason for this was that masking noise had been removed so that more silence was present in between each and every instrument. The ear immediately picked up on this extra swathe of information. I found my ears bouncing from one instrument to another, trying to pick everything up all at once. One example, remember I mentioned that distorted guitar above? Previously, it sounded like an effect, a novelty in fact. Now, that same distorted guitar offered more information within its own presentation. The sound wasn’t just a layer of distorted noise. There were guitar strings in there and multiple tones.
That sonic improvement continued with repeated cleans on the Audiodesk. I gave the LP five cleaning cycles in total. After that, the midrange continued to smooth out, leaving any aggressive, nasty frequencies to the past while bass was now focused and more precise while the drum kit used on this track offered more variation in terms of the different drums being hit. That is, the tonal differences for each drum were more noticeable.
CONCLUSION
So what’s going on here? Instead of the purely passive cleaning system of most RCMs, I’d say that the Audiodesk provides passive/aggressive cleaning regime. If you look at all other record cleaning machines, not one of them actually attacks the grooves directly in any way. It’s always done indirectly. Now, you would think that such a method would be a good thing, in absolute terms. After all, if you picked at the grooves with a spike, then you would remove any embedded grime but you would also damage the groove.
What all machines do is to douse the grooves with liquid, hope the liquid loosens muck (which is why too many over-eager people use aggressive and harmful alcohol), then you are encouraged to hold a brush steady on the rotating vinyl surface to create a bow wave or swirling liquid effect in front of the brush to agitate the grime which is then, later, hoovered up.
The Audiodesk doesn’t do this. Those exploding bubbles actually direct an external force into the grooves. If you’ve viewed either or both of the videos above, you will have seen how large items react to this system. You can see how caked-in dirt, dirt that is embedded onto the surface, dirt that has often been lying on the items for a long time, is removed by ultrasonics. Apart from the superior liquid agent, that is the difference here in vinyl terms. Apart from the removal of loose particles, it’s the embedded dirt that has, up until now, never been removed, and has proven resistant even to an expensive record cleaning machine. This, is a true first for record cleaners. This, in vinyl terms, is revolutionary.
The Audiodesk is expensive in basic terms, yes, but the improvement in sound quality is akin to upgrading from a budget to a top flight turntable. In those relative terms, its cheap. A complete bargain. You know what? I spent a few long minutes, after reviewing the Audio Desk, just staring at my vinyl collection. Once oh so familiar, I suddenly realised that I didn’t know what any of them really sounded like. Not any more. With the Audio Desk, I was going to find out, for the very first time. Even my buying habits had now changed. Apart from the unlucky record buy, here or there, featuring groove damage (which can happen, we all know), now even charity shop and car boot finds hold fewer fears.
A well built, easy to use record cleaning machine with the added benefit of simultaneous, double sided cleaning and an automatic wet/dry system. What makes this design truly audiophile, though, is the ultrasonic addition and the top notch liquid cleaner. That means that, for only the third time ever on this site which features more than 200 product reviews thus far, it receives a perfect 10/10 score and the extremely rare Golden Groovy award.
TO SEE A REVIEW OF THE PRO 2019 UPDATE CLICK HERE
AUDIO DESK PRO ULTRASONIC VINYL CLEANER
Price: £2,295
Web: www.audioconsultants.co.uk
Tel: 0118 981 9891
GOOD: superlative cleaning abilities, sonic improvements, automatic, both vinyl sides cleaned
BAD: limited to Audio Desk’s own fluid, roller replacement costs, for 12” records only
RATING: 10
FUSED DIRT?
There is a sort of urban myth out there which says that it is impossible to thoroughly clean an LP or, rather, an old LP because over the years, the heat and pressure from the stylus will physically ‘fuse’ the dirt to certain areas of the groove. In this way, no record cleaning machine can remove such grit. I really don’t believe this at all. What I think we are talking about here is not fused dirt but embedded dirt. That is, dirt that sits in a groove cavity or hole and will not be removed by the stylus (which hits it and leaps over it creating a pop or a stylus jump) or hoovered up by RCM because the dirt is firmly ensconced in the vinyl itself. I believe that this sort of dirt can only (to date) be removed by ultrasonics because of the active and passive-aggressive cavitation process. I talked to part of the audiophile reissue team over at the Sundazed record label (www.sundazed.com) and chatted to Jay Millar. He was my ‘go to’ guy because he used to work for the major vinyl pressing plant over at United Record Pressings in Nashville, Tennessee, “The friction caused by the needle riding the groove does indeed cause very high temperatures but it’s very brief,” said Millar. Enough to cause fusing? “I would say it’s unlikely due to the high melting point of the dirt. The temperature of the needle, while high, is not present in one spot long enough to melt the groove even with the pressure from the weight of the stylus.”
[…] All vinyl was cleaned using an¬†Audio Desk‚Äôs Ultrasonic Pro¬†Vinyl Cleaner¬† […]