The Article
ONE STEP BEYOND: Mobile Fidelity Gets Closer To The Music
22nd April 2017
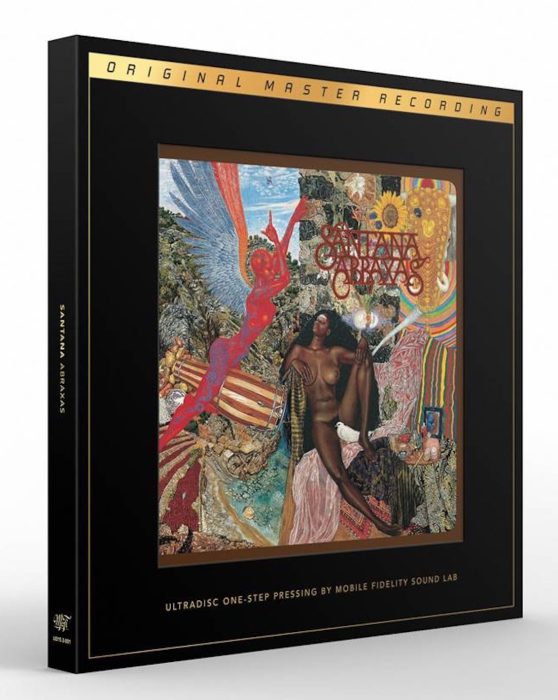
Looking to push the vinyl mastering/pressing envelope, Paul Rigby talks to John K Wood and Shawn Britton of Mobile Fidelity about its innovative One Step vinyl process
“Instead of utilising the industry-standard three-step lacquer process, Mobile Fidelity Sound Lab’s new UltraDisc One-Step (UD1S) uses only one step, bypassing two processes of generational loss.”
So said the company. Hence, the UD1S stamper, called a convert, produces the actual records. None of this ‘father’, ‘mother’ routine that you normally see, the world over, when vinyl is made on a day-to-day basis from negative and positive copies before the final vinyl is created for commercial sale (see the accompanying graphic for more information on the process).
“We compared the test pressing One Step recordings with the standard pressings,” explained Senior Mastering Engineer, Shawn Britton. “We heard a better signal to noise ratio and the surface noise was lower. To use audiophile reviewer terms [lots of sarcasm here] ‘the blacks are blacker!’ Meaning it’s fricken’ quieter, you know?! The first release using the system is Santana’s Abraxas. It starts out with the track, Singing Winds, Crying Beasts with cymbal washes and then, what Stan Ricker (the late, great mastering engineer and pioneer of half-speed mastering) used to call “Twinkly shit.” Which was a great term to use at hi-fi shows, by the way. For those wind chimes, you hear greater detail. You hear more of those low level details. Reverb tails carry out better, there’s a more pliable sound stage. It’s pretty impressive. I thought that it might be a high frequency thing but we now think that the bass is more solid too.”
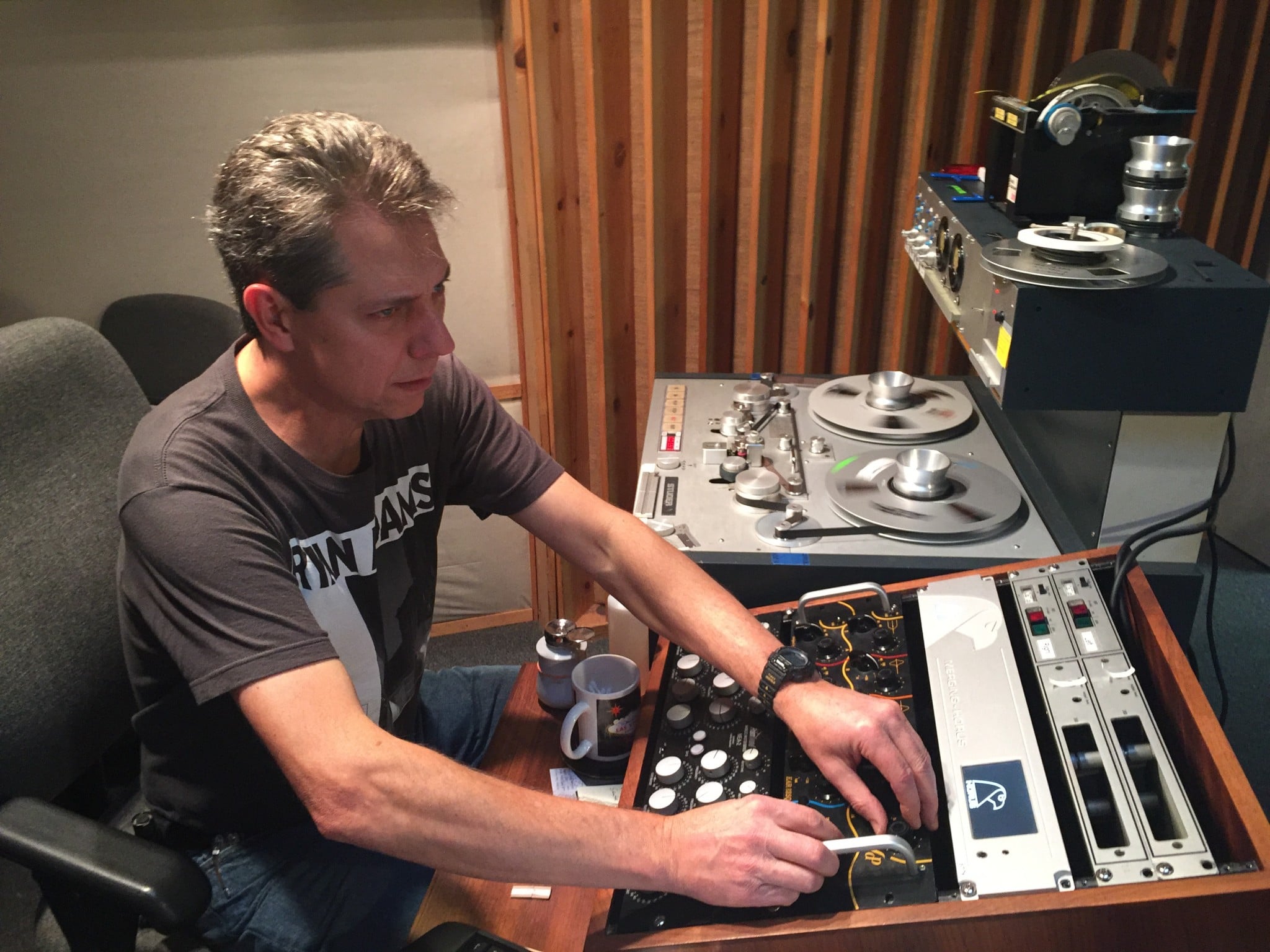
Why does the One Step system sound so good? Well the clue is in that first paragraph, “I would think from a physical point of view that, when you electro-plate something and then peel it apart, as in the case of a lacquer and the convert then metallise that which would make it a father at that point and then peel that apart, there’s bound to be some slight distortions introduced in those processes,” said Britton. “If you think about the groove walls – these things are 2mil deep – smaller than a human hair. The grooves, therefore, are so small that groove wall deformation is entirely possible.”
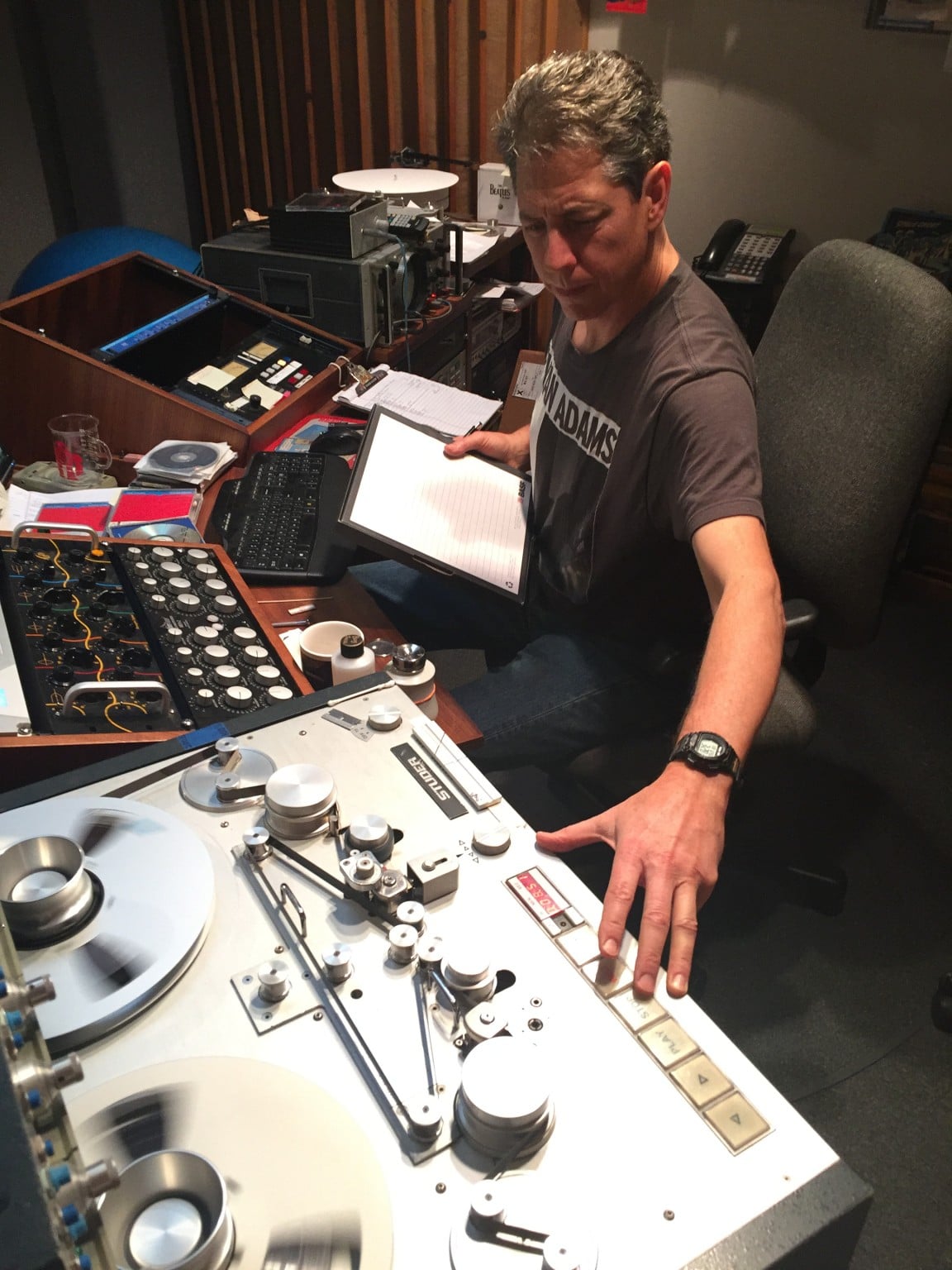
Hence, if you remove the extra steps currently utilised in the vinyl record creation process – and these processes are very physical – then there is less chance of even tiny groove deformation occurring and thus more chance for the music to really sing.
“In LP mastering, one of the concerns that you always have is that low level details are going to be lost in the surface noise so what some people (i.e. mastering engineers) do, in very quiet passages, is goose up the level a little bit to get it out of the surface noise but you don’t have to do that now, with One Step” said Britton. “That’s something that we like to stay away from here, we want the full dynamic range of the music as it is off the master tapes. Adjusting any levels would only be for the greater good of the album. For example, to equalise the volume over different tracks so that you are not adjusting the volume control track by track, so it doesn’t jar. That’s dependent on the mixing too.”
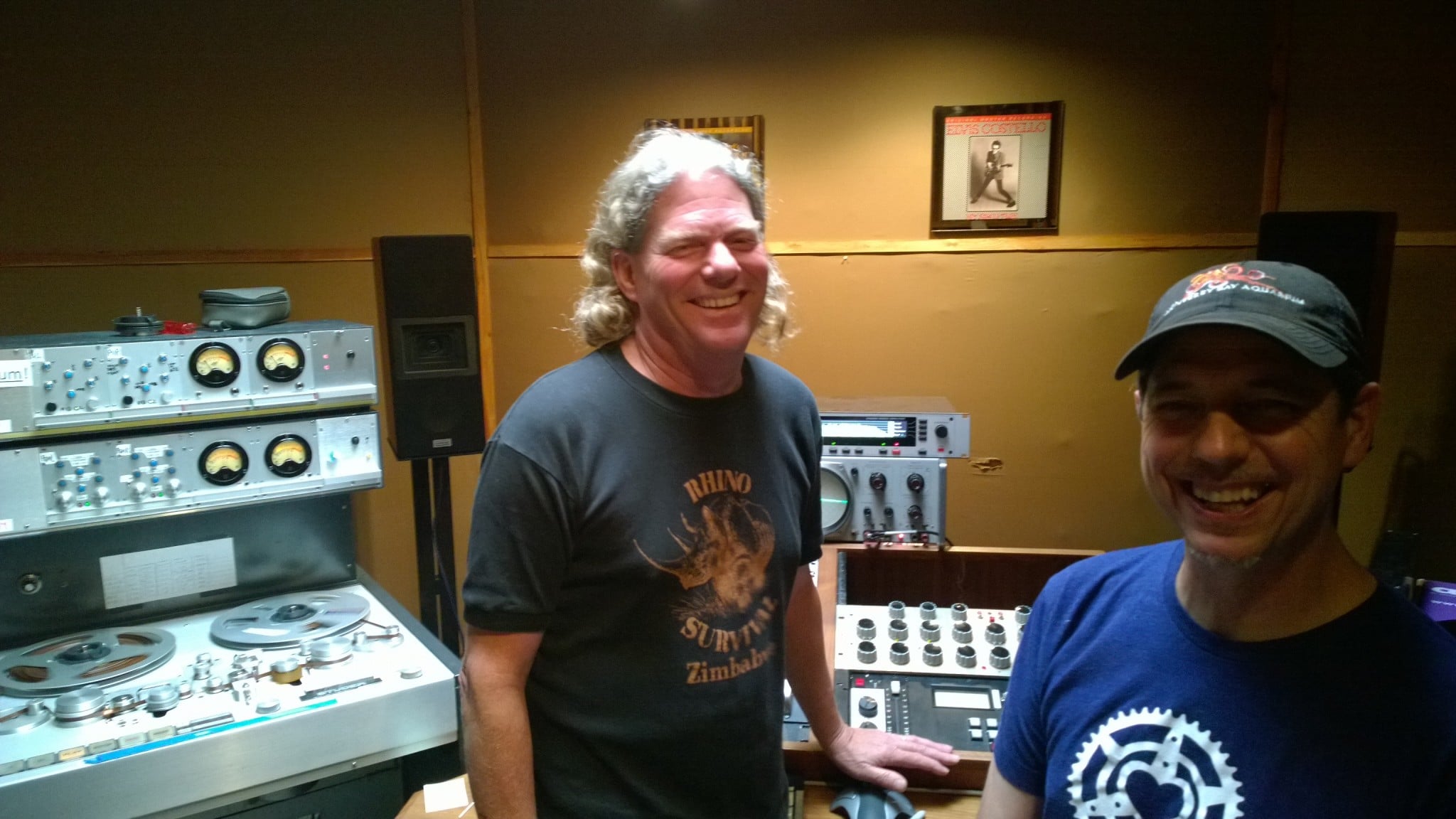
The One Step process, which also runs at 45rpm to further enhance sound quality, might produce superb sonics but it is hardly a common process. As Executive Vice President of Mo-Fi, John K Wood explained, “No-one has tried this process commercially before, it’s too expensive. I know of no-one else who has done it before in the same way that we are doing it. There might have been a few small experiments out there. I know that Stereophile magazine tried to do it, for example, but they abandoned the project because it was too expensive. We can do it because we are charging $100 per product.”
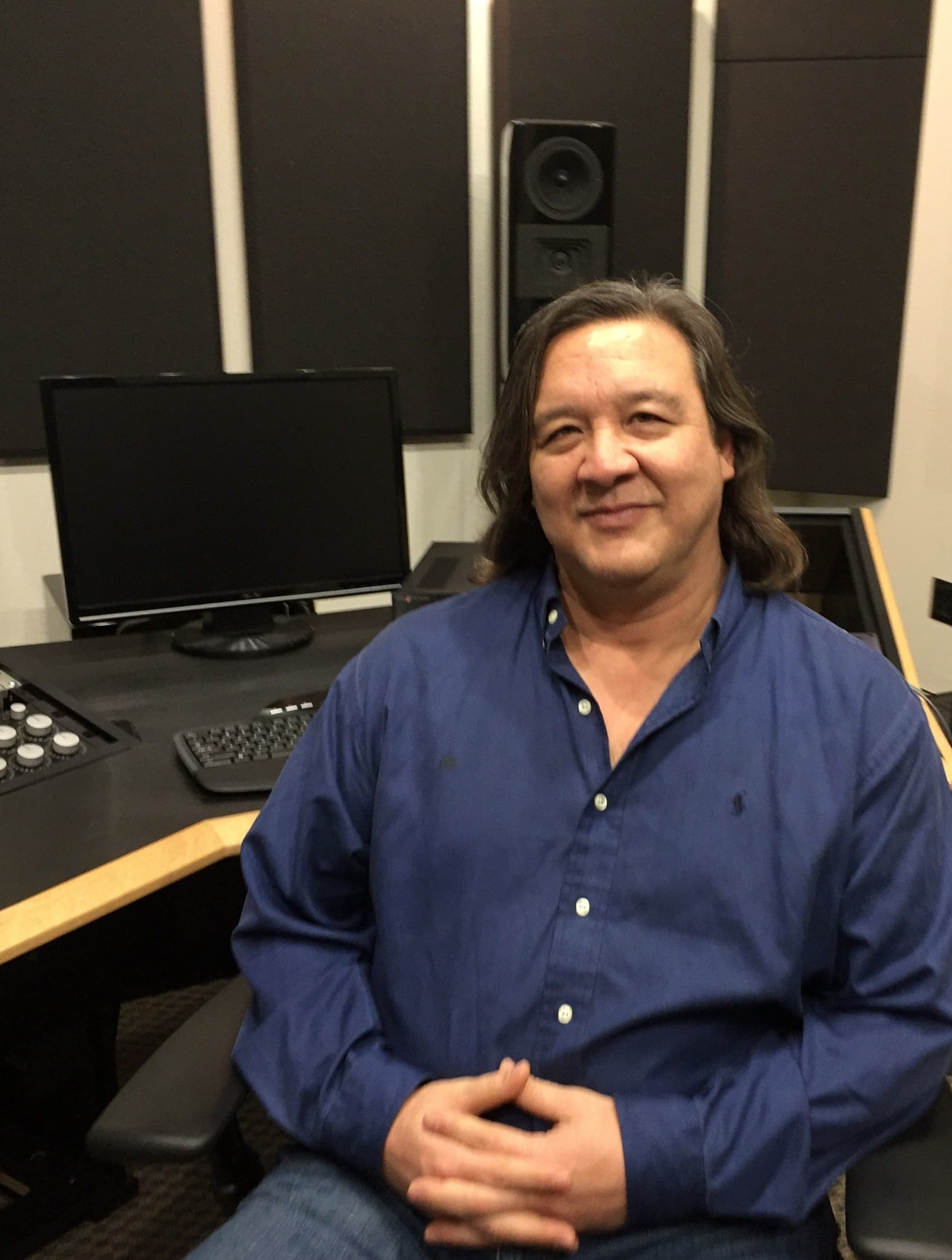
So why now for Mobile Fidelity? Why launch into this process at this time? “Well, we actually started developing the system three years ago. Tim de Paravacini built our cutting lathe electronics for the Neumann lathe and the tape machine electronic enhancements to our Studer reel-to-reel tape deck. He mentioned it to us. We are always asking Tim, ‘What can we do better? Can we tweak the tape machine more? What can we do to the lathe? Let’s try something.’ So Tim mentioned this One Step process to us, which hasn’t really been used in the past because the yields are ridiculously low. We always take heed of what Tim says so we thought, ok, let’s do it.”
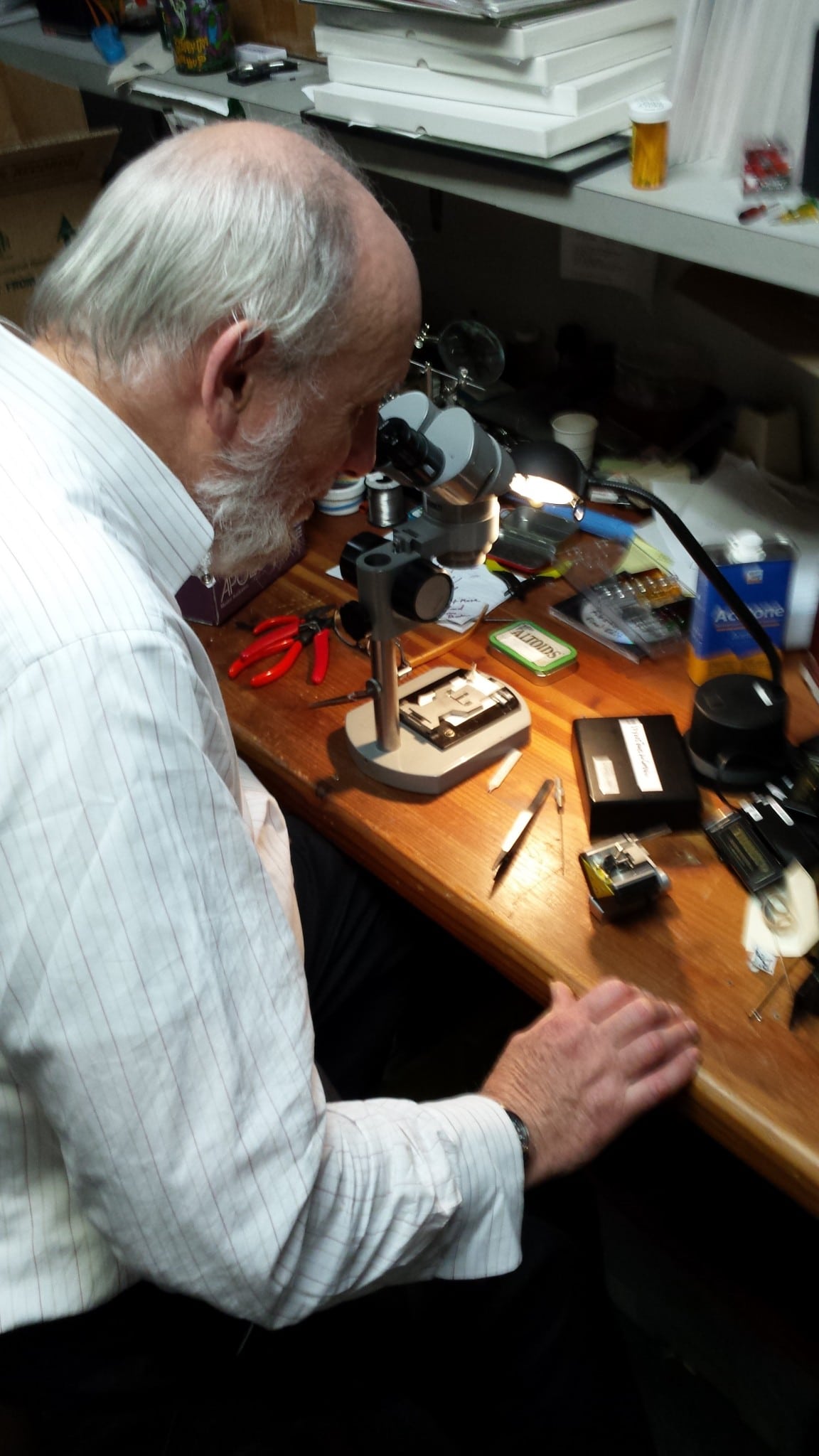
Ah, the “yields”. The problem with working with a fragile ‘convert’ to produce the final records is that Mobile Fidelity was only comfortable in producing 500 records from it while retaining maximum sound quality before wear and tear was due to set in. But what if you want to produce 2,500 units from the original lacquer (as Mo-Fi has done for the debut release, Santana’s Abraxas)? It means that five separate converts had to be produced to end at the final figure of 2,500. And that was a reason for the high final price. Despite utilising less generational steps you do end up spending more money on One Step because, “The cutting engineer has to cut five A-sides and five B-sides, there’s more stylus replacements during that cutting process, then there’s his extra time, then the pressing plant has five processes too and then there is their time. And so on…,” said Wood.
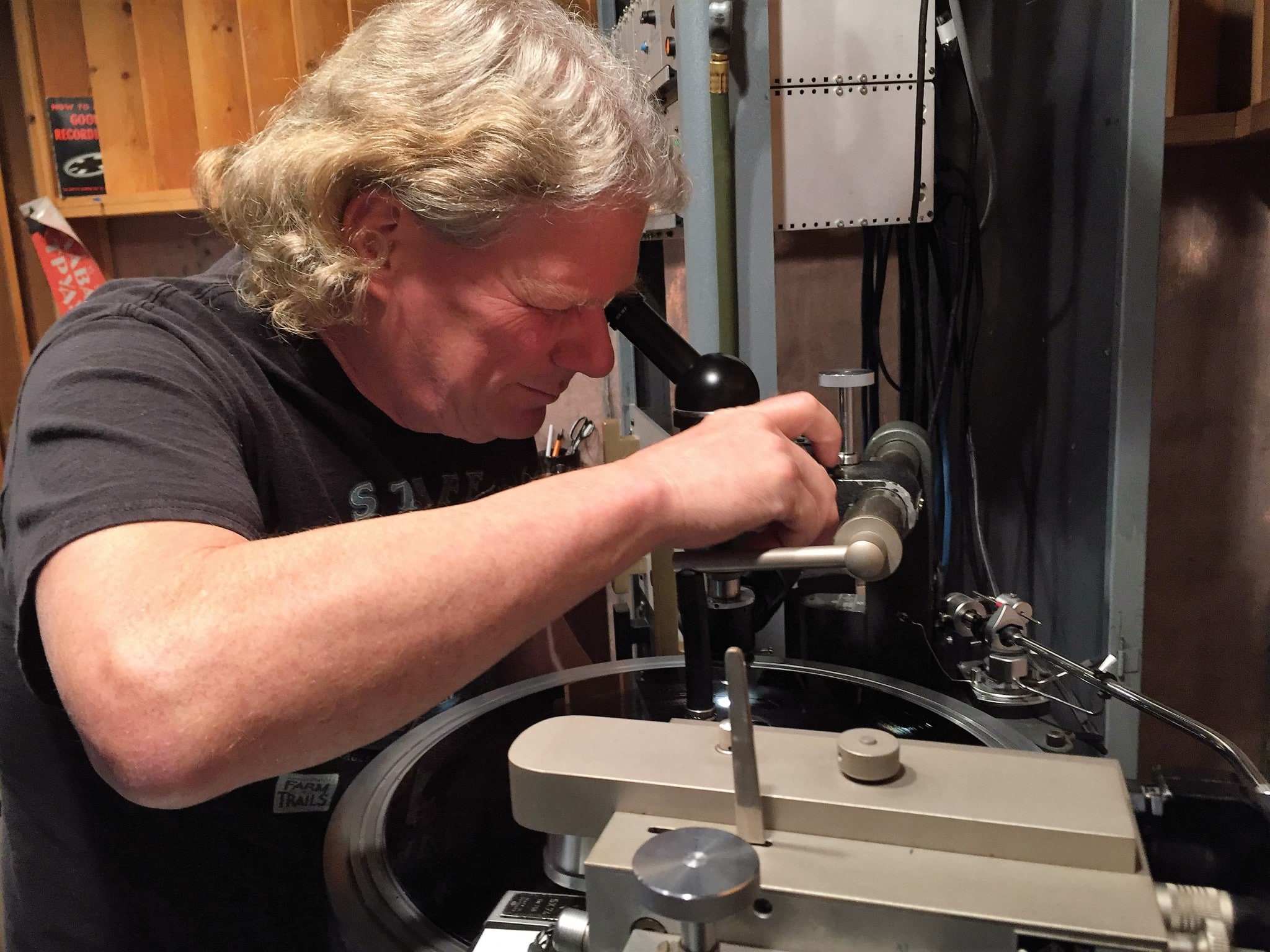
Santana’s Abraxas is a classic album but why choose that particular title? Why not do a modern recording to tape?
“Why use that beat-up old record, eh? Abraxas is known as a really well recorded rock album,” said Wood. “Sure, there’s audiophile recordings of a triangle that rings out in a church that sounds fantastic but this type of record is what we do best.”
“We wanted to present this sort of compelling stuff with the sound quality to match. Abraxas is a well known album too which helps. Thus, anything that appears on One Step will be noted for its recording quality. There’s a balance between the sound quality and the music, of course. We wanted it to be an experience kind of thing. Each title has to fit. We’ll be very selective.”
A DOLLAR TOO FAR?
Mobile Fidelity wanted to produce the first pressing of Santana’s Abraxas as a statement product for the One Step process, not knowing if there was a real customer demand for it. The company was prepared to ‘take a hit’, in terms of investment, if the records didn’t sell, “That was a concern, yes,” said Wood “Is there a market for a $100, 2LP record in a box? The Santana LP was a trial but the response was excellent. What happened? We sold out before we even had stock! There’s copies on eBay now, looking for $200-300. I’ve seen a low number edition on sale for $800. And that’s just now! The demand was overwhelmingly stronger than we thought it would be.”
MOBILE FIDELITY’S HI-FI HARDWARE
We are familiar with Mobile Fidelity’s foray into ‘software’ and their magnificent vinyl pressings but now the outfit is looking towards entering the hardware market.
The company hasn’t approached this market segment in a half-hearted manner either because the new hi-fi products include two turntables, two phono amps, three cartridges and two turntable weights!
The StudioDeck turntable utilises a 19mm Delrin platter with a MoFi/Allen Perkins (founder of Spiral Groove) 10” arm, MDF plinth, an isolated high torque motor, a hardened steel inverted bearing with isolation feet supplied by respected outfit, HRS and a dust-cover (removable). Price is $999.
The UltraDeck is similar but increases the Delrin platter thickness to 33mm with additional arm damping and Cardas tonearm wiring. Price is $1,799.
Both can be supplied with a StudioTracker (extra $150) and a UltraTracker (extra $200) cartridges, respectively. The former is a V-Twin Generator-based, high-output MM with an elliptical stylus and polymer body (normal selling price is $199) while the latter includes a nude stylus and well damped billet aluminium body (normal price is $499).
Another new cartridge design from MoFi is the MasterTracker ($699), another high output MM with a micro linear stylus and pure Ohno copper coils that arrives in the same aluminium body type.
The StudioPhono amplifier has been designed by MoFi and Tim de Paravicini, can handle MM/MC signals and features a subsonic filter plus mono mode at $249 while the Class A UltraPhono is different at $499 as it offers variable loading, a headphone amplifier and adjustable gain.
The two turntable weights, designed by HRS, feature proprietary vibration isolation technology and come in two weights depending on the mass of your platter. Price will be announced for both soon.
To learn more, click www.mofi.com
There are an awful lot of qualifiers in the statements being made. Lots of “possibly” and “could” statements. So, in other words, these guys aren’t even sure if what they’re doing is any better than the traditional process. It’s just way more expensive for the end consumer, without any actual evidence of improvement in sound quality. Got it.
Not at all, Breed7, I have done my own tests and find the sound quality excellent. I’m not too sure what your referring to, maybe you can be more specific?
I just ordered the 6th in the One Step Series with Stevie Ray Vaughn’s Texas Flood. I love the sound quality of this series. It is all worth it to me. I spin them as they were meant to be, not stored on a shelf for a family member to auction some day after I am gone LOL.
And so you should, David, I agree. Vinyl is there to be used. Music is there to be heard and enjoyed. Glad you’re enjoying your vinyl
I’ve completed my own tests on MoFi vinyl. I’m not an expert by any means but I know what sounds good to my ear. That’s all that counts right? I’ve compared the following to the original and they all sound better. Allman Brother’s “Eat a Peach”, Gordon Lightfoot’s “Sundown”, and Cat Steven’s Tea for the Tillerman. In most cases, the albums have a better width about them. Overall deeper sound with a bass that was not present on the original. I also have the Miles Davis’ “Kind of Blue” and Derek and the Dominoes editions but have yet to listen to them. The ones I listened to sound so great and the overall presentation is wonderful. I plan on buying more MoFi editions in the future for sure.
Hi Chris – your ears are everything. Never allow a machine to tell you what to buy. Thanks for your thoughts and insight.
Hi Paul, Thank you for a good write up. I have all of the UD1S albums with the exception of Santana Abraxas, and I wish I would have discovered them when that album was preorder.
All of the albums are much better than the commercial copies that I have. The latest release, Yes – Fragile, is the best one yet.
I always buy 2 copies, one to listen to, and one for my heirs to auction off when I’m gone. 🙂
Do you happen to know what else is coming down the pike? I’m aware of Mingus, Ah, Um, and SRV, Couldn’t Stand the Weather. Do you know of others?
Hi Richard – *pencilled* in are:
Blood, Sweat And Tears – Blood, Sweat And Tears (second album)
Paul Simon – Still Crazy After All These Years
Electric Light Orchestra ‚Äé‚Äì Eldorado – A Symphony By The Electric Light Orchestra
Thanks Paul
What a fun read after being a fan of this series since Abraxas was available for preorder. I preordered two of each from the start. It’s crazy to me that my sealed Abraxas is worth so much, I figured $500 but not north of 2k and rising. But these pressings are the bees knees. I figured buying 2 copies was smart because if one ever got damaged I could never afford the secondary market prices to replace it.
Thanks Mike and yes, crazy prices!