The Article
J.A. MICHELL ENGINEERING: Factory Report, Enhanced Edition
22nd June 2017
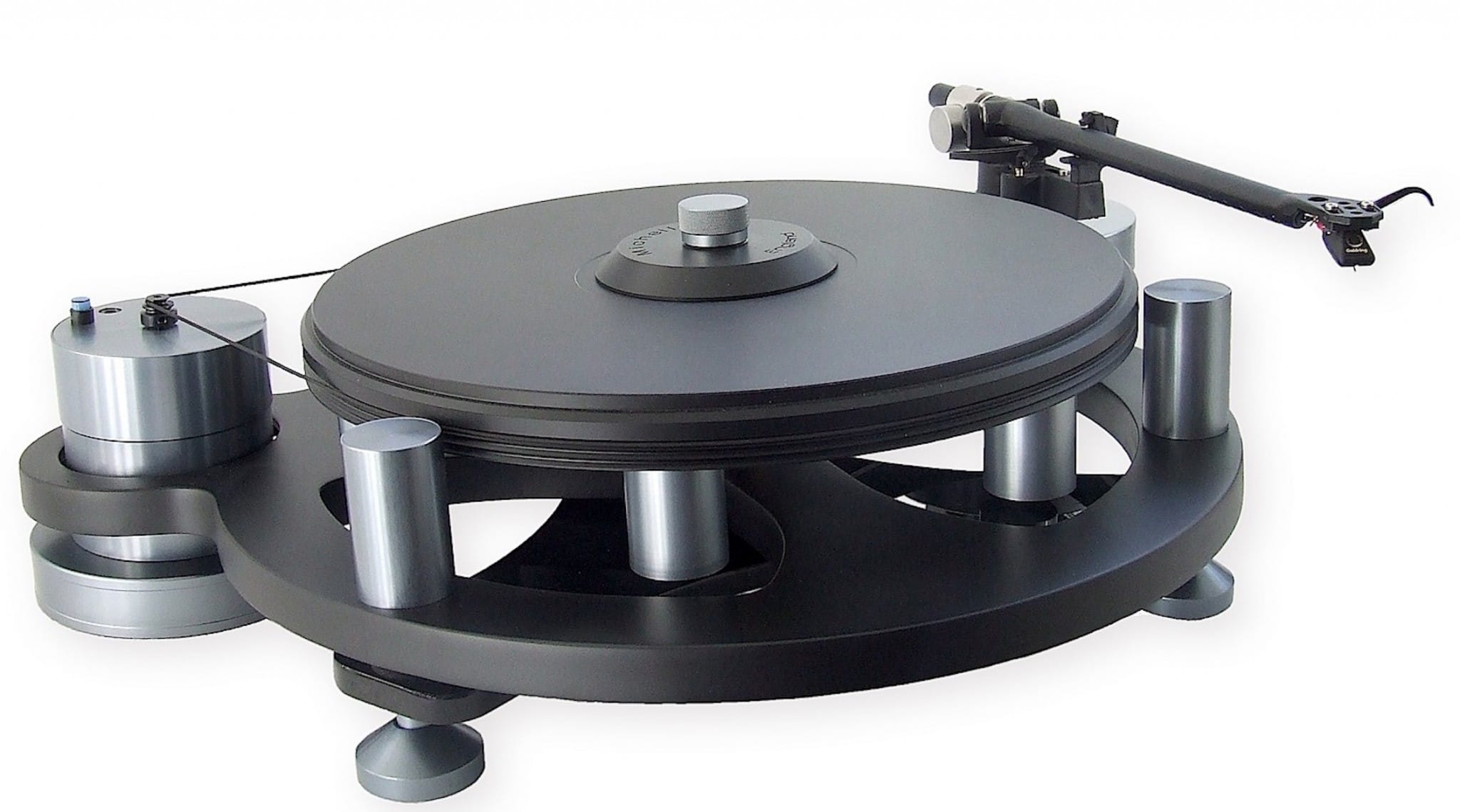
Despite the short walk from the local railway station, combating busy roads and the usual hustle and bustle of a working day, it’s easy to walk past the unassuming site. In fact, I initially did. When you eventually do enter into the courtyard that serves as the works car park for J.A. Michell Engineering, however, it hits you immediately. History surrounds and dominates the arena, surprising you like a bank of fog on a winding country lane
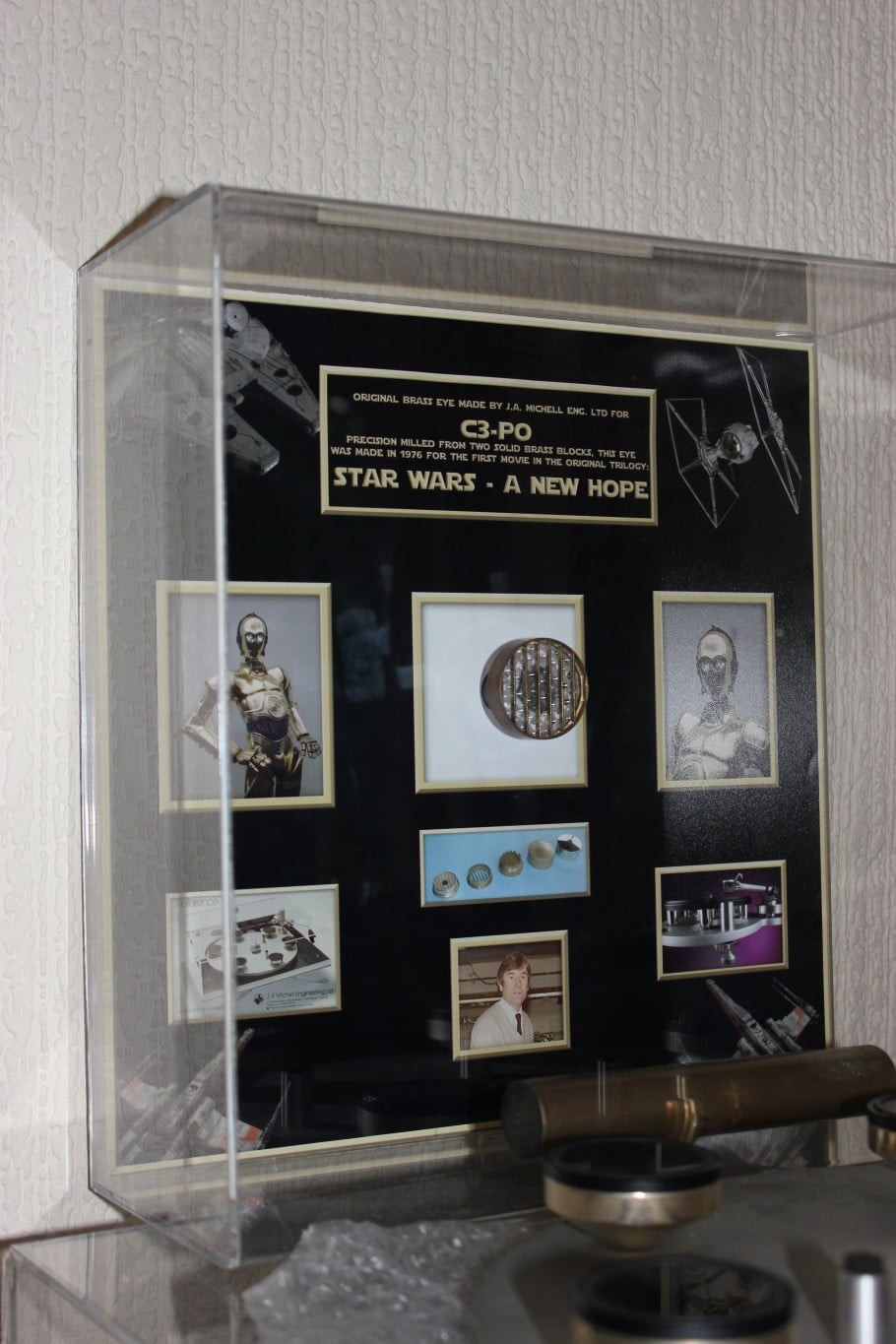
It’s not because the place used to be an old pub, either, it’s more than that, it’s personal. The much missed and respected company founder, John Michell, is present still. Like a protective ghost, John Michell’s philosophy, ethos and practices are infused within this company. He’s in the structure of the offices and workshop that hasn’t changed in form or style since he founded the business in 1973. He’s in the original German-made, Feinbau machines that made the precision parts for his early turntables but now lie dusty and unused, propping up sheets of hardboard, symbolic to the fact the J.A. Michell Engineering never throws anything away…just in case.
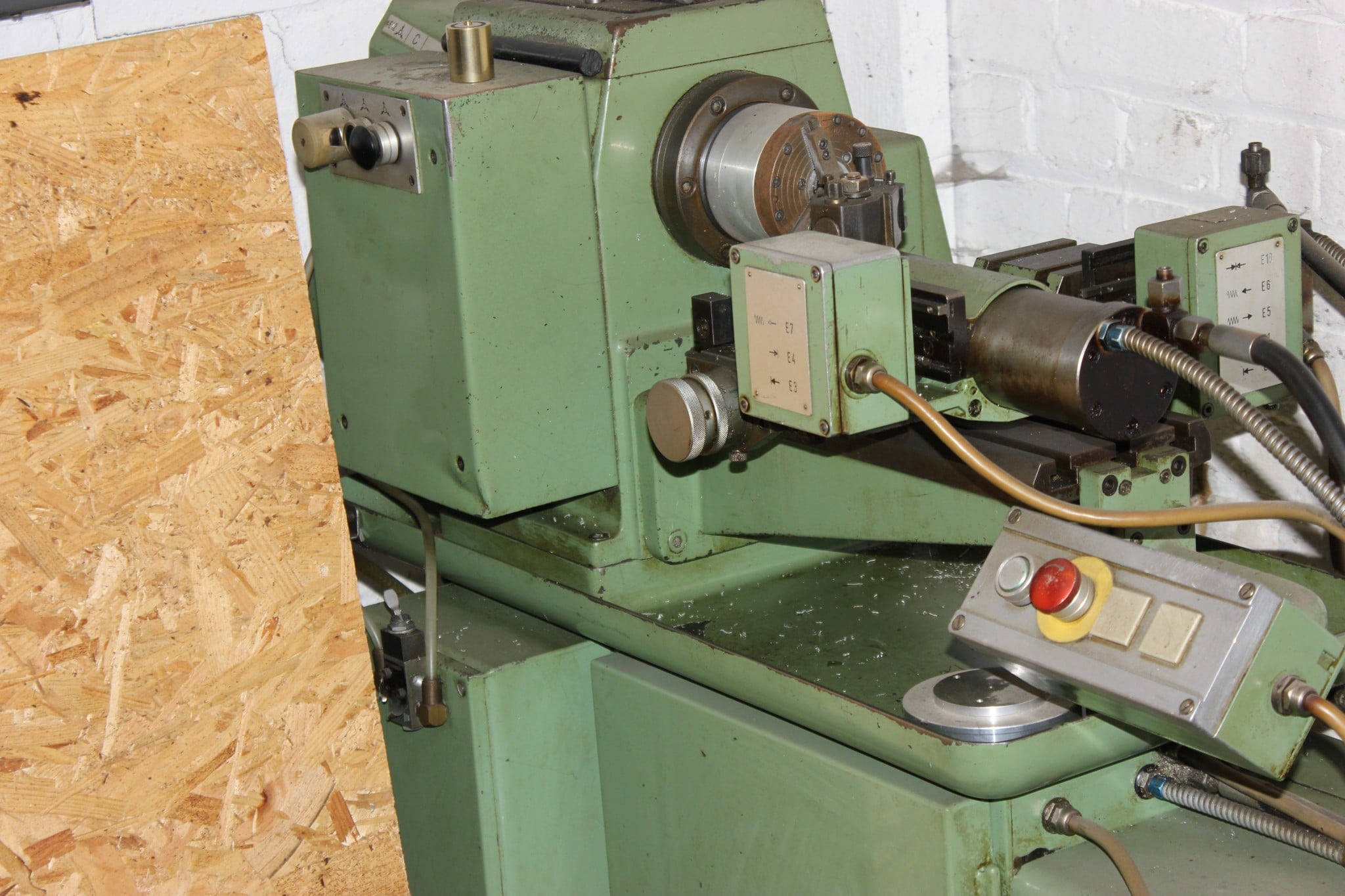
He’s in the faces of the members of staff, many of which knew and worked with John as well as the face of his daughter, Julie, who sits as a company director. He can be seen in the designs of the entire range of products that the company sells, whether they be turntables or the gamut of accessories and upgrades that support those decks. Finally, he can be heard and seen within the Works Manager, Steve Rowland, a man who only joined the company to help out when John Michell was too ill, from cancer, to fulfill his normal daily duties.
THE FIRST CLAMP
“What you have to remember about John was that this place was his life,” said Rowland, “he didn’t delegate at all. I joined the company in January 2003. When John died, that October, I would go to the guys and say, well, we’ve got to do ‘this’. I’d get a ‘Well, I don’t know’ reply. I’d say ‘What do you mean? You’ve been here forever’ and they’d say ‘Well, John always did that.’ So, they’d go to a hi-fi show and the staff would start to set everything up and John would say, ‘No, leave that. I’ll do that.’”
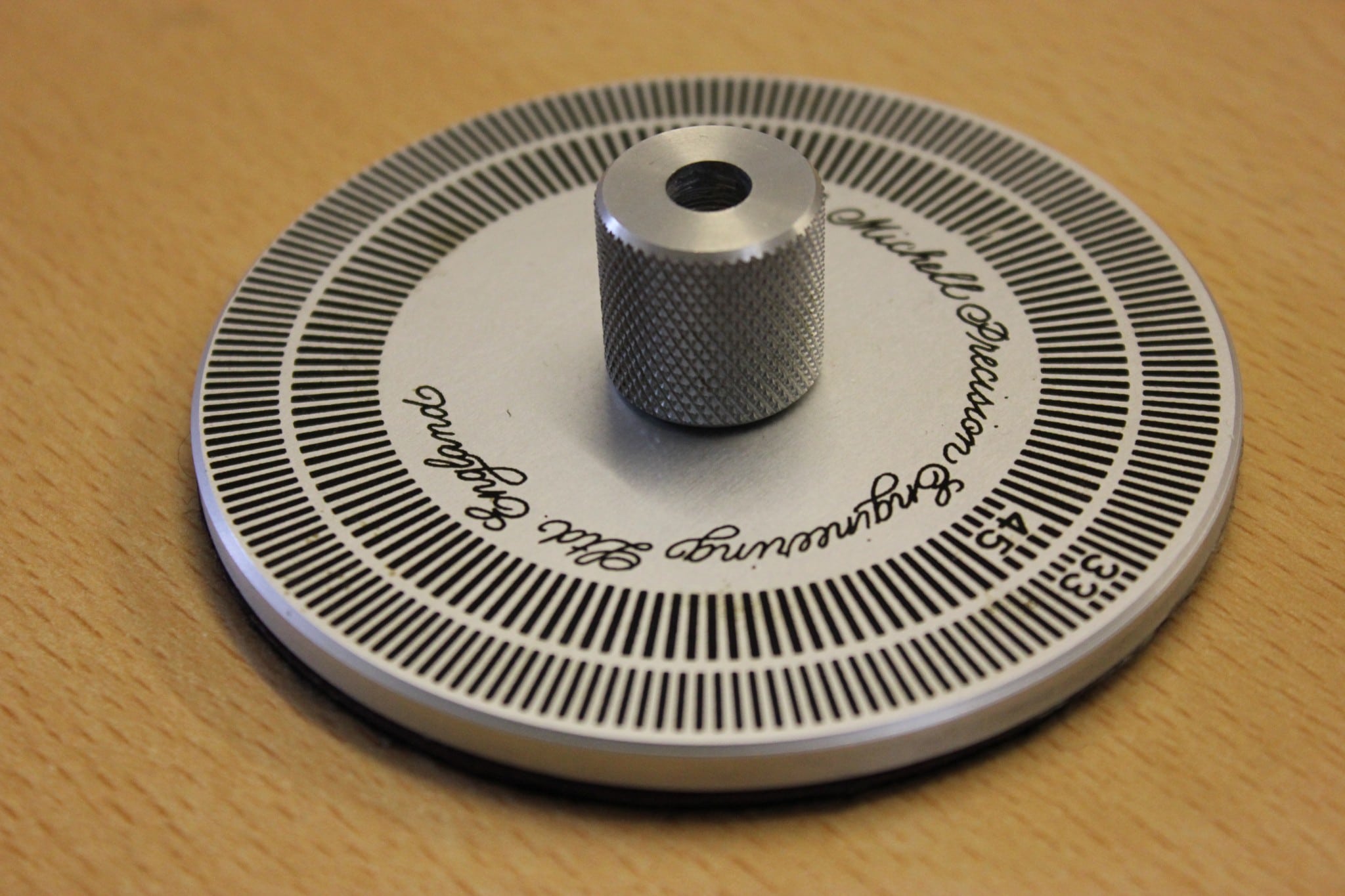
Not to put too finer point on it, John Michell was a control freak, although he hated administrative duties. He much preferred to be sketching his latest engineering ideas on a pad during a lunch break. In fact, he’d rather be unblocking the drains in the car park than being stuck in the office.
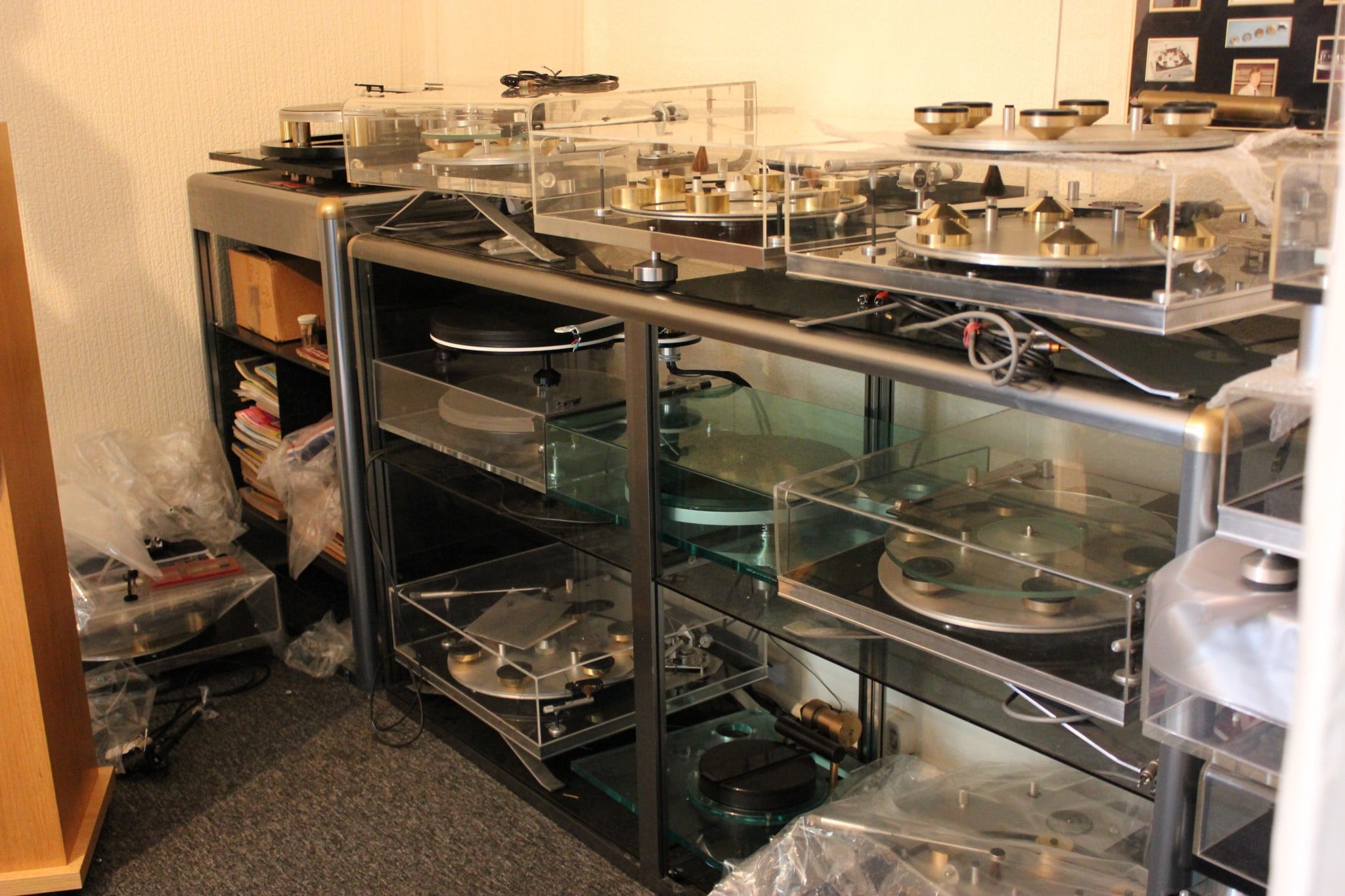
Anyone who has worked with, used or seen a Michell turntable would find it hard to disagree that John Michell had high standards. He was analogue’s restless prodigy, his imagination and innovation is there to see in his early forays in the film industry. Whether that be the building of the Discovery space ship for Stanley Kubrick’s legendary film, 2001: A Space Odyssey or within his attention to detail building the complex eye and fitting of the overly helpful robot, C3PO, in George Lucas’ blockbuster, Star Wars.
MICHELL MONA LISA
It was also seen in Michell’s early days as a jobbing engineer, making parts for Transcriptor turntables to the flowering of that potential with the launch of the highly modified Hydraulic Reference deck sporting the J.A. Michell Eng. Ltd badge. What followed was a series of distinctive designs such as the Prisma and Focus One. The GyroDec, however, became Michell’s own Mona Lisa: a study in beauty that refuses to age.
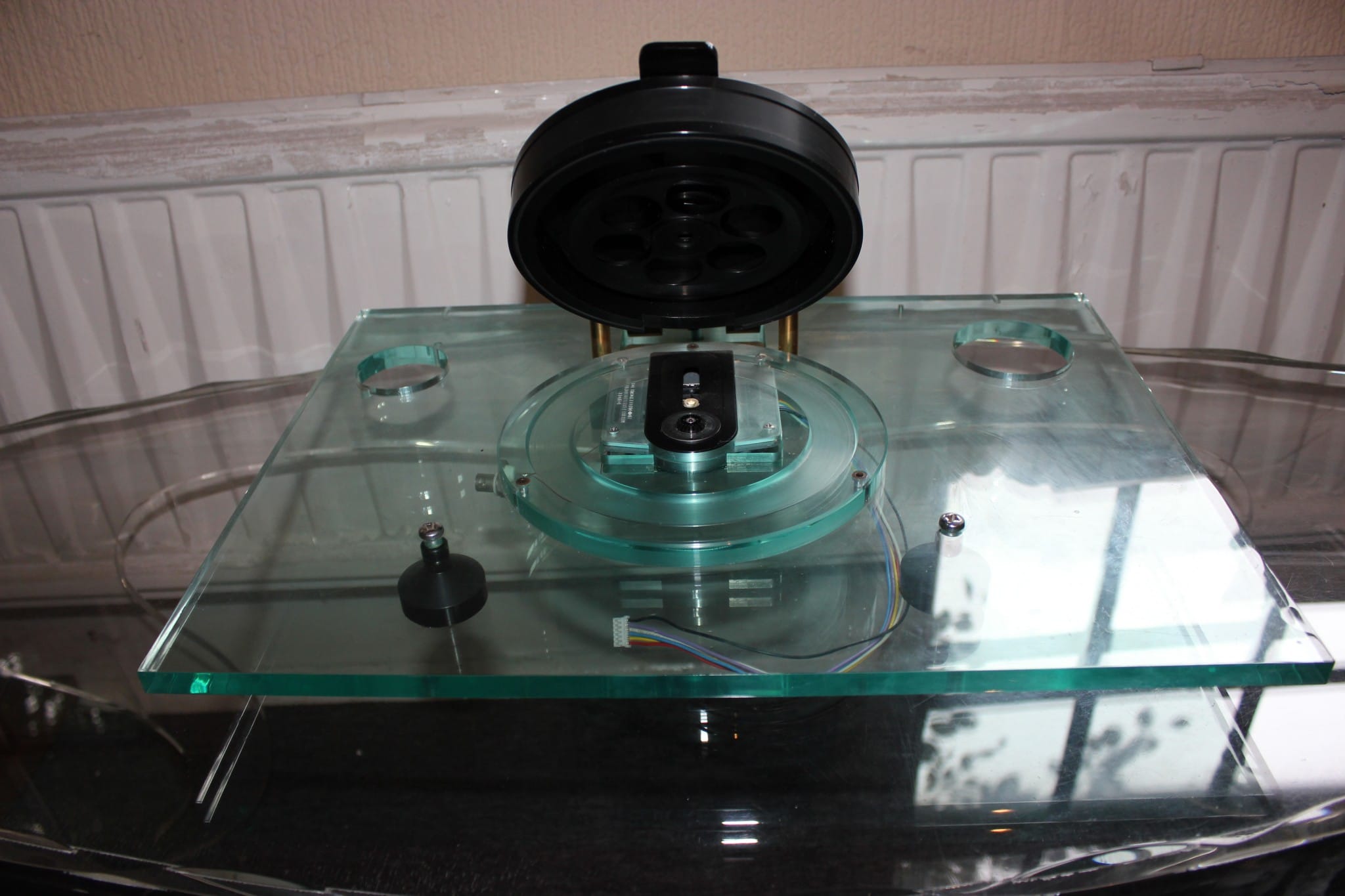
In John’s last years he saw the introduction of the TecnoArm, TecnoWeight and HR Power Supply but, since his death, the company has been restricted to cosmetic enhancements and the Orbe’s Never-Connected power supply, released in 2006. You have to ask, though. Why is that? Despite the accessories and upgrades to current designs, why haven’t we seen a completely new turntable from Michell since the Orbe, in 1995?
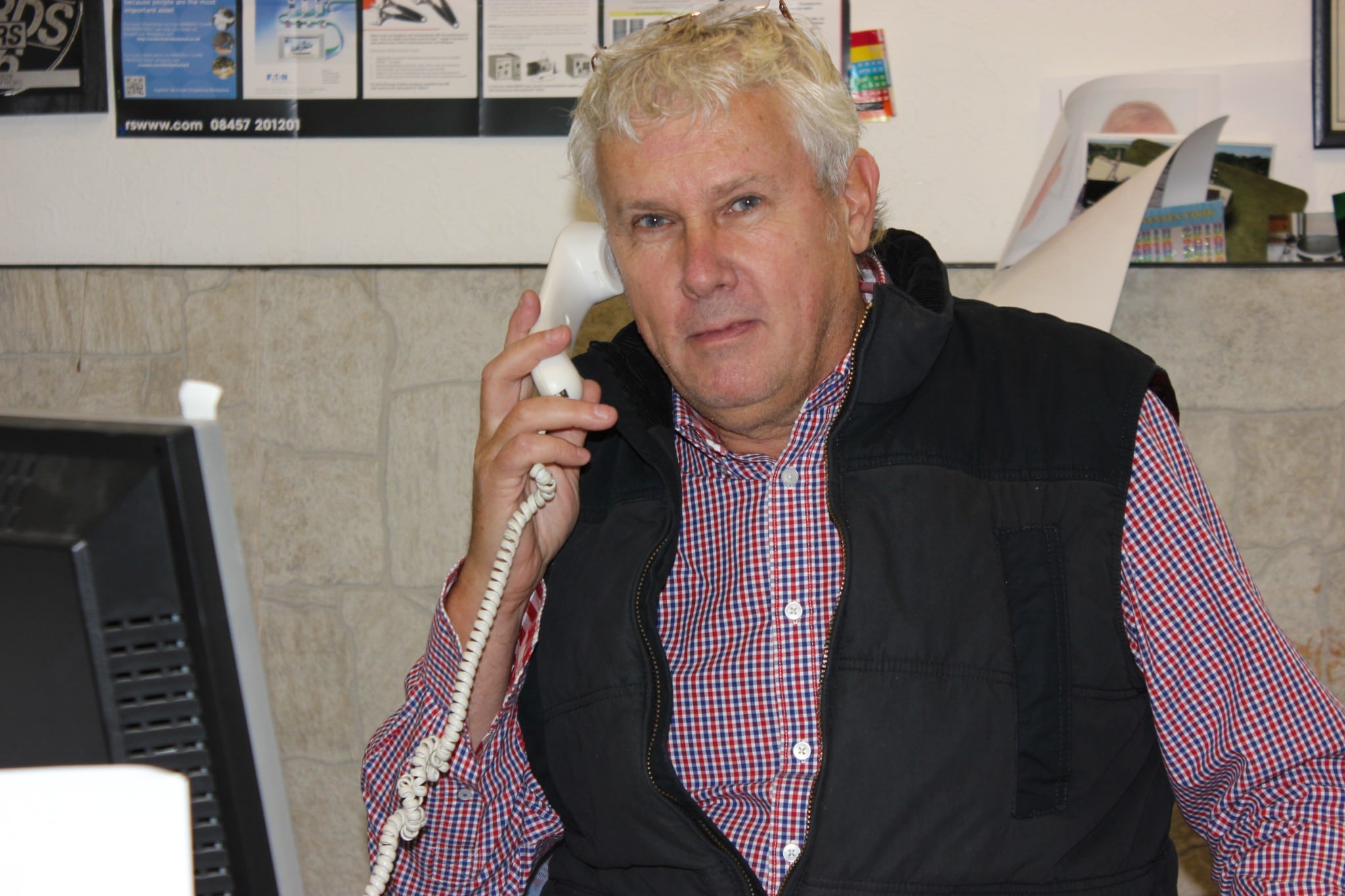
Curiously, because there has been no engineering prowess at the company since John Michell past away. A remarkable situation for any company trying to survive in the current hi-fi market. In fact, during the later stages of John’s illness, the future for the company became clouded, “He came very close to selling. Very close indeed,” said Rowland. “There was a third party that knew that he was ill and had mentioned it to others. Because of John’s total control of the company, they thought that this place stood no chance of John keeping it going if he wasn’t there to control it. It was his daughter, Julie, who convinced him not to sell.”
A NEW TURNTABLE?
When John eventually died, Rowland wondered if the company could carry on. Michell received plenty of support from the industry and retail sectors, however, not to mention the loyal customer base that slowly stabilised the company. Opening up new markets in Eastern Europe, Asia and Japan added to the security.
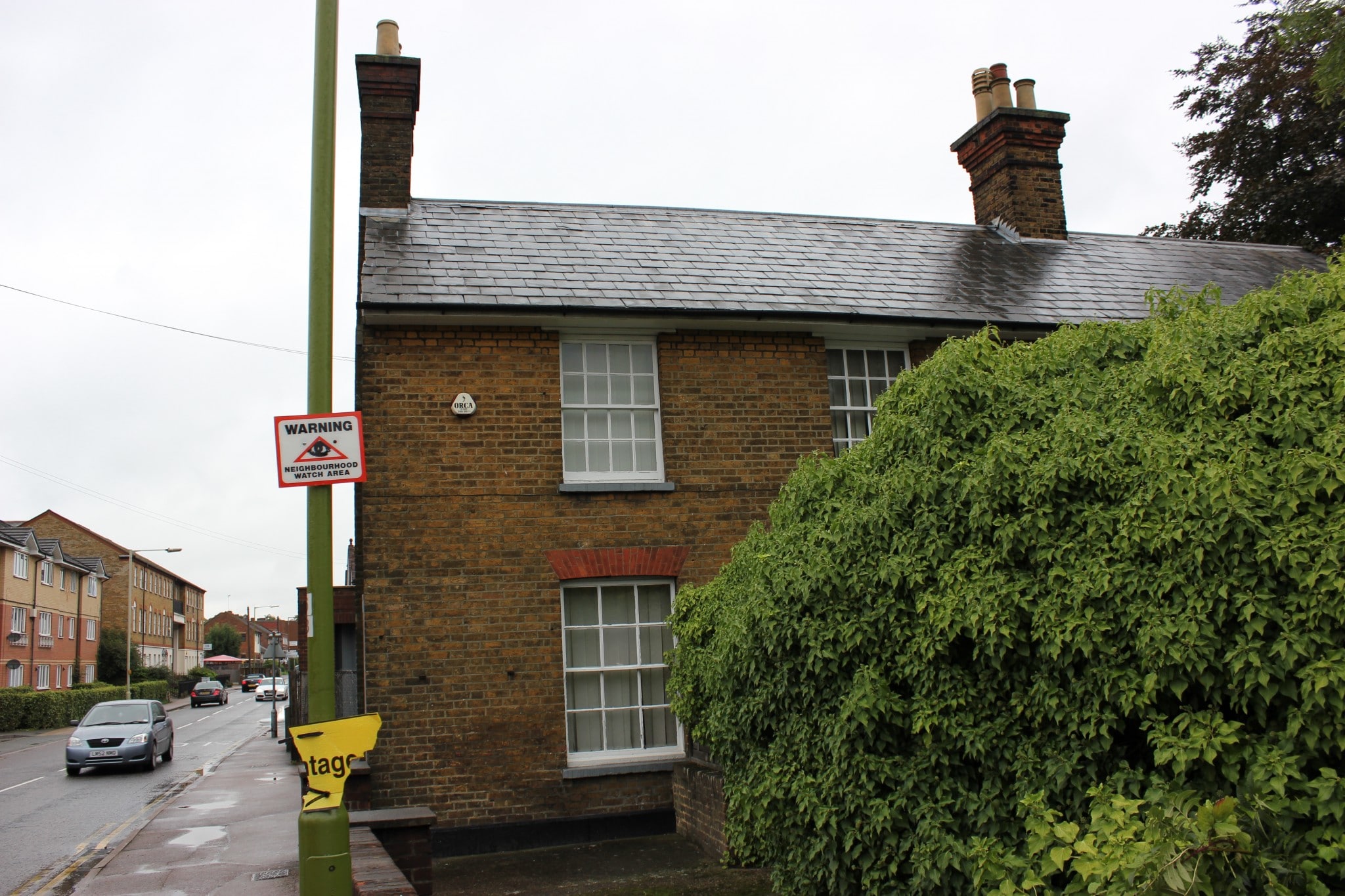
With a bit of luck and a following wind, however, Michell has a future. One that might just be wrapped up in Steve and Julie Rowland’s son-in-law, the young Jonny Nye. Brought in from the Home Automation industry where he worked for two high profile companies, Nye is an engineer. He’s even picked up that Michell-esque habit of sketching new ideas on bits of paper during his lunch hour.
More than that, there is talk of a new turntable. Don’t get excited, though. It’s literally at the drawing board stage and shows no immediate signs of leaving it. I was privileged to see the design on Rowland’s own PC and it looks impressive. Instigated by another, nameless, engineer, situated outside of the company, it resembles something that you might use to cap a nuclear power station, utilising three ‘grab handle’ suspension springs. It looks very Michell-like but, as to when it might reach the market?
“Well, the problem here is that we are slow,” said Rowland. “We’ll come up with an idea and, over the period that we’re faffing around, someone else will produce a similar idea so we’ll drop ours. For example, we thought of putting an Orbe platter on a GyroDec chassis but then Transrotor did their Fat Bob turntable and Pro-Ject also did something similar.”
CUSIS
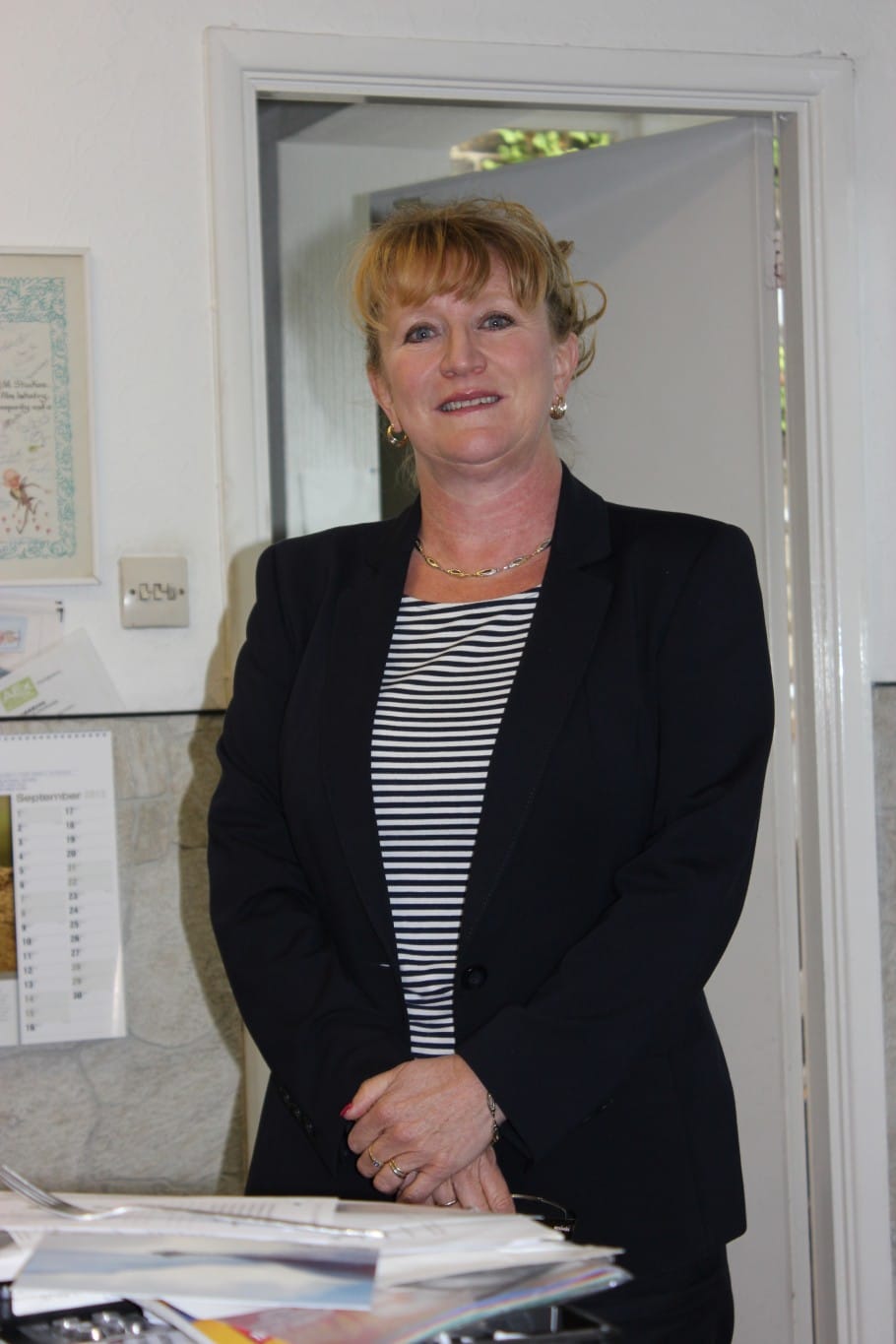
Despite the slow emergence of new product, Michell is on the verge of releasing a new cartridge, which has been developed in conjunction with Benz. I had a quick, secret peek in, of all places, the toilet of Michell’s exhibition area at the last Sound & Vision show, last February in Bristol. Progress has been made since then. The cartridge is ready to go, only the hinged jewellery box container is awaited. Called the Cusis, it will retail at £1,065. The name has a medical context and is Greek for ‘ear’. A second cartridge, the Oris, was planned but its performance was deemed too similar to the Cusis so it was dropped. Michell see the Cusis cartridge filling a gap in its range, serving as a solution to new turntable owners looking for a suitable and compatible cartridge for their new deck.
As it stands, Michell performs well in the high-end budget and midrange sectors and that is reflected in the sales figures. The company is doing well if it sells 550 turntables per year. That figure is relative, however. For example, Rega will ship 800 RP1 budget turntables on a single pallet yet Michell refuses to compete directly on that level, “We’ve been asked to do a budget turntable,” said Rowland, “but how the hell could we compete with that? Actually, we don’t do as well as we should with the TecnoDec. Priced at £735, in it’s own right, it’s a good little player. Compared to the GyroDec, the TecnoDec has the same motor, style of bearing, platter and power supply but people are too busy aspiring to buy a GyroDec.”
BLAST FROM THE PAST
Standing in the centre of the Michell workshop, you feel that you have stepped back into the 50s or 60s: it screams craftsmanship and looks like an ideal design template from the files of one of the nearby film sets or possibly Ealing Studios. Wooden benches are everywhere, old lathes and milling machines sit in dark corners, tiny drawers of wiring, tools and other, unrecognisable gizmos provide fuel to this hive which sets a gentle yet quietly industrious pace.
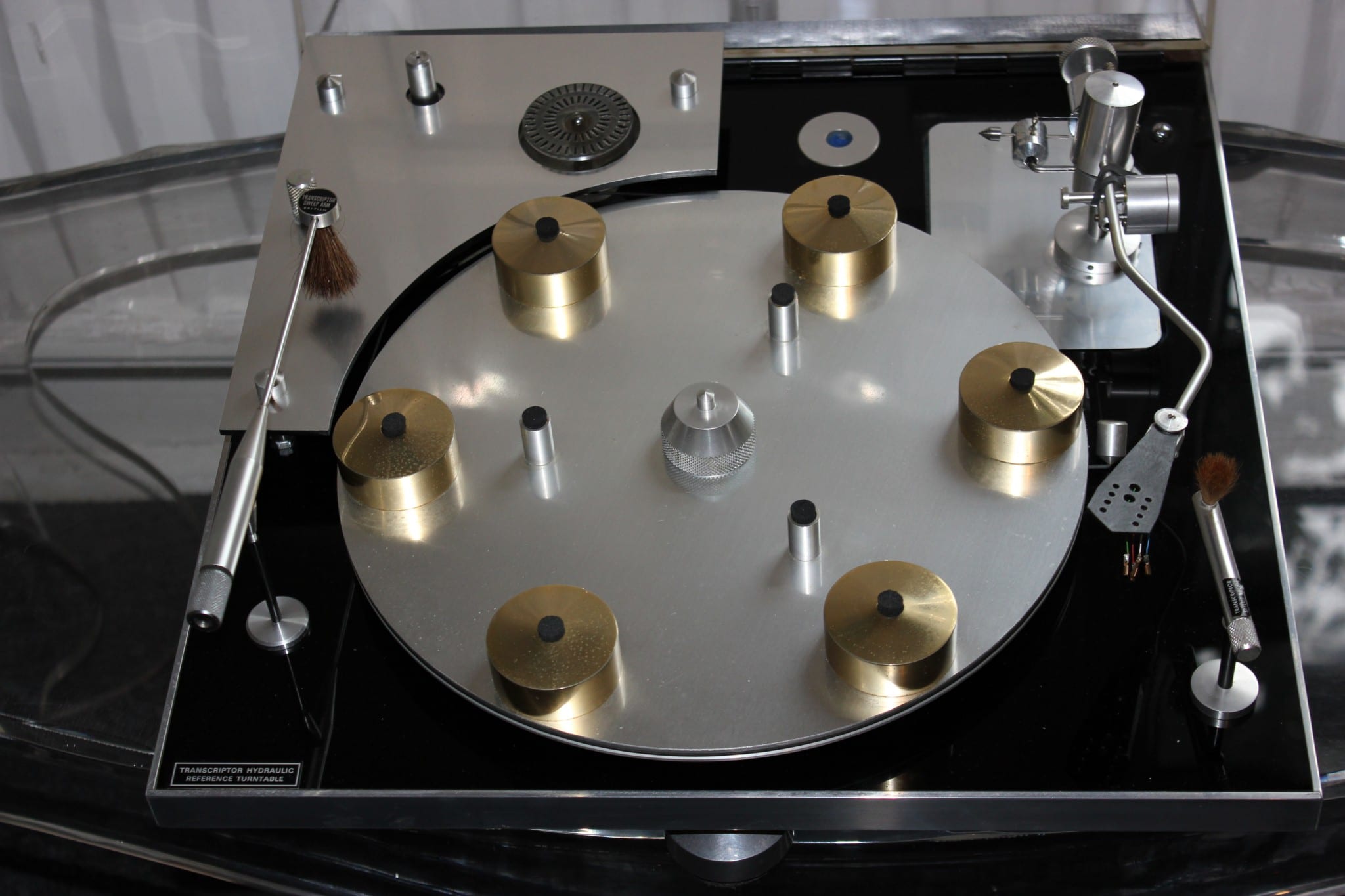
One of the reasons that Michell products are so popular, apart from the rich history that runs through the company, is its traditional manufacturing methods and standards of manufacture. For example, unlike other iconic hi-fi names like Wharfedale and Quad, Michell has not been tempted by cut-price Chinese manufacturing techniques. With the exception of a European-sourced motor, all of the parts are obtained from UK-based companies who sub-contract to Michell, supplying parts to Michell’s specifications. Michell buys the raw material, it then delivers it to the sub-contractors and they make the parts from that material. In this way, Michell retains control and maintains consistency, which is often a criticism of Chinese methods.
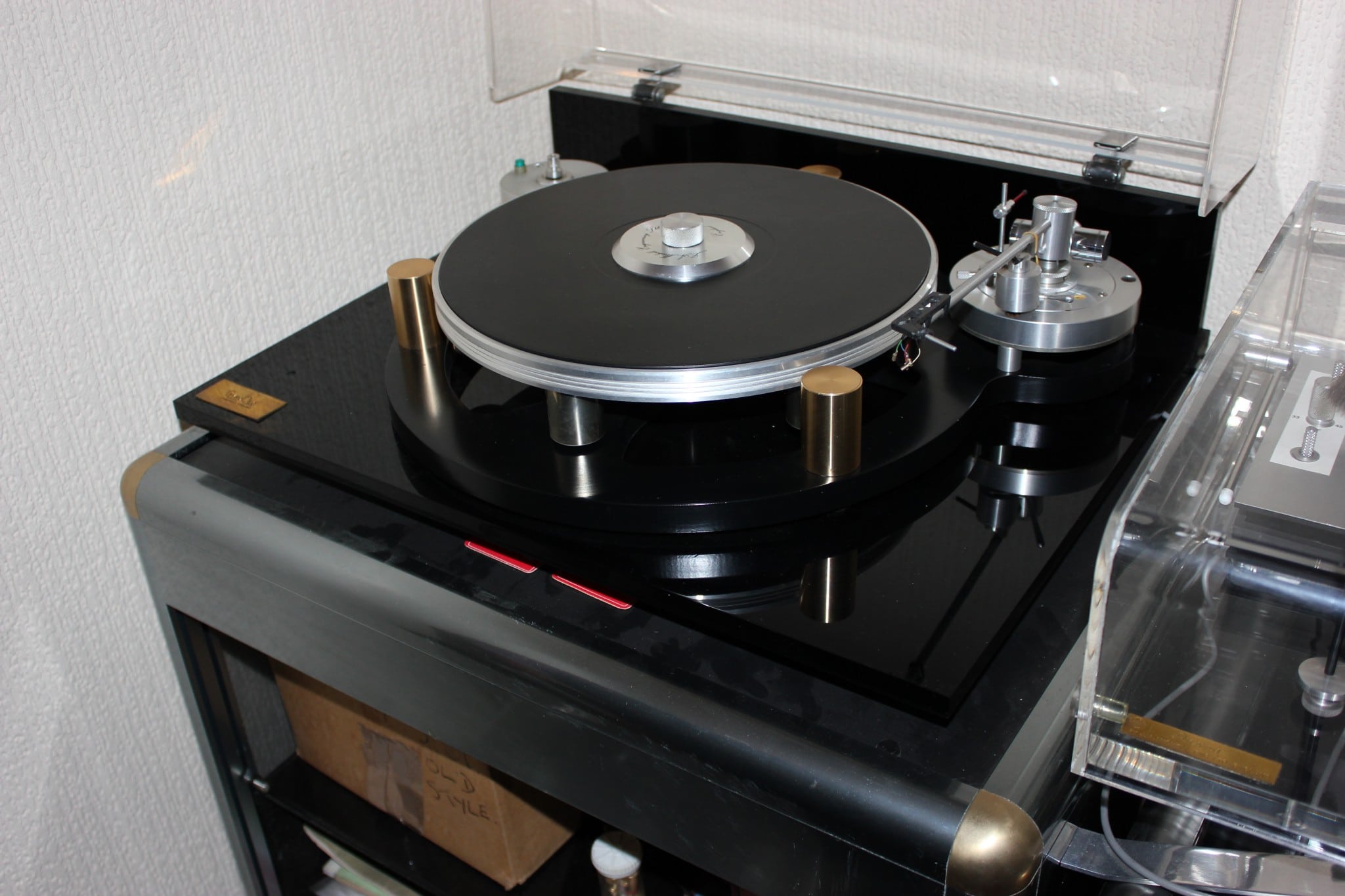
Michell Engineering used to employ 20 people, at its height. That’s been reduced to just six or seven with three in the workshop itself. Because of this concentration of labour, each workshop technician subsequently gains more significance. Working in the space, during my visit, was Jonny Nye, “Our daily routines change regularly,” he said “I would normally check the orders and assemble the GyroDec and Orbes. Recently we’ve had a load of platters come in so we need to check them out for quality.”
IT HAS A BEARING
Picking up the latest GyroDec bearing, Nye was also eager to talk about its hidden capabilities. A subtle spiral engraving is machined on the bore of the bearing so, when the platter is turning, oil is drawn around the spindle to lubricate the thrustball, it exits back into the well as an Archimedes Screw.
It then circulates so that any stray, foreign, items that would possibly sit around the ball, grinding against it are ‘filtered’, carried by the oil from the ball, back down into the well. The bearing is self-cleaning, in effect.
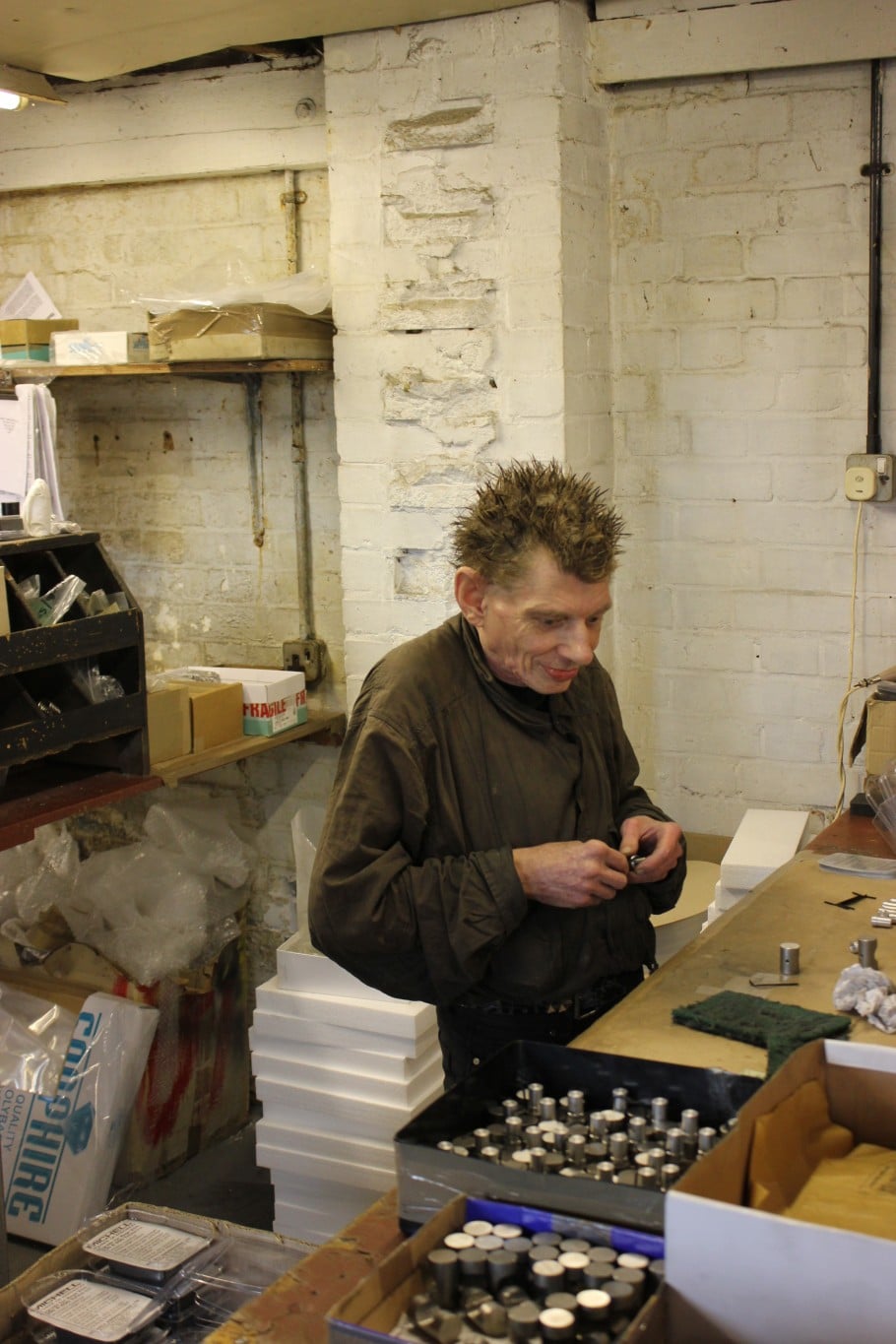
Sitting behind Nye, occupying his own desk, is Michael Rayner, who looks after the electronics within each turntable, “After examining each component, we look for physical defects, then run the components, check the bearing, the motor and the power supply,” he said.
Rayner arrived at Michell in 1978, after leaving school, working in the machine shop on lathes and the mill. During my visit, Rayner worked upon the power supplies, motors and cables for different turntables. Not just for the UK market. Different specifications are required for the USA and Europe.
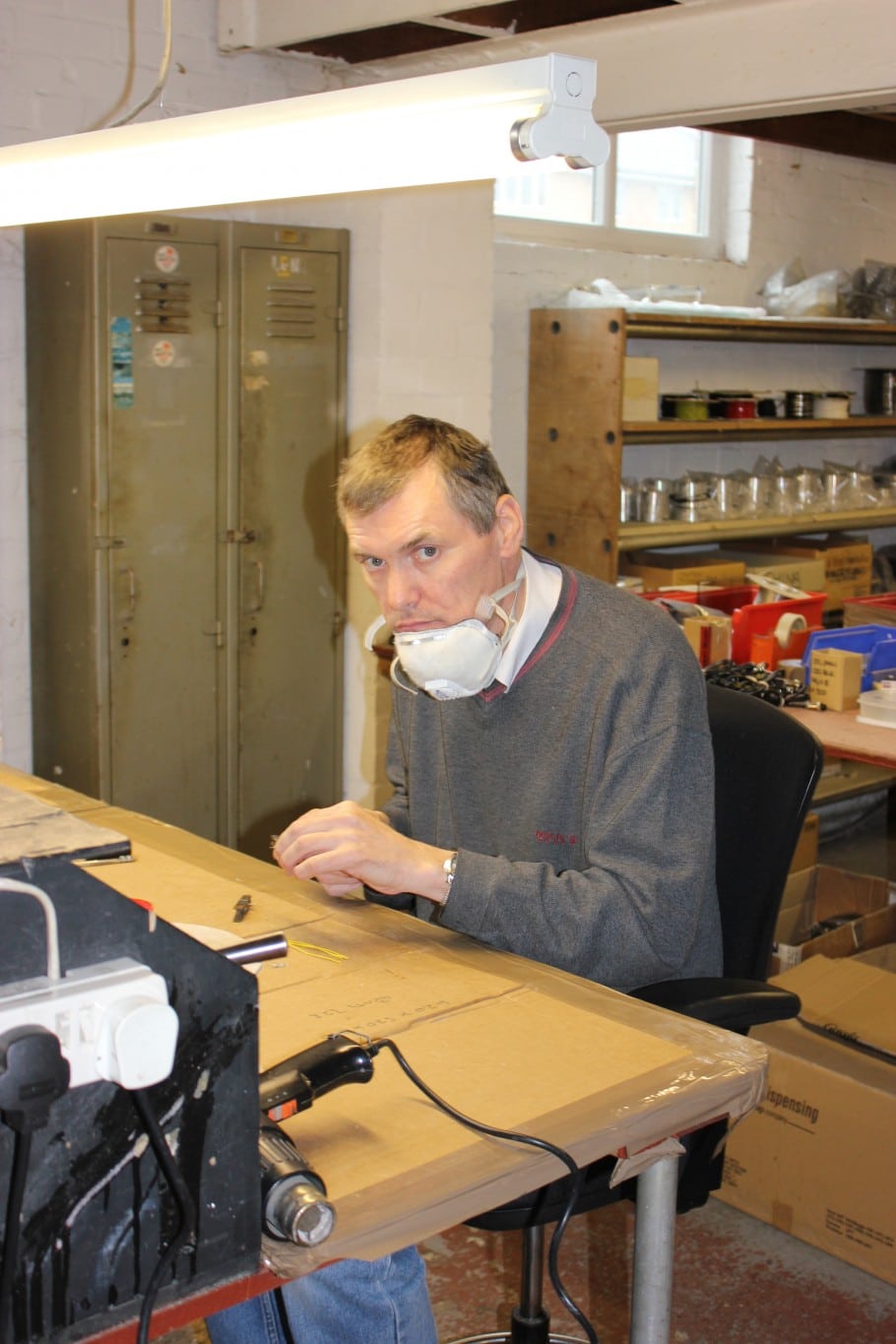
Repairs are another major part of the working day. Situated behind Rayner, during my visit, were vintage Focus One and Syncro turntables waiting for attention, “You get issues with the old electronics on the older models,” said Rayner.
Sometimes handling three or four turntable repairs in a week, all three workshop staff members have a role in repairing the items or applying upgrades. That includes the enigmatic Paul ‘Punky’ Rundle, devoted to machining and assembling the TecnoDec, “I also create accessories such as the TecnoWeight and so on,” he said.
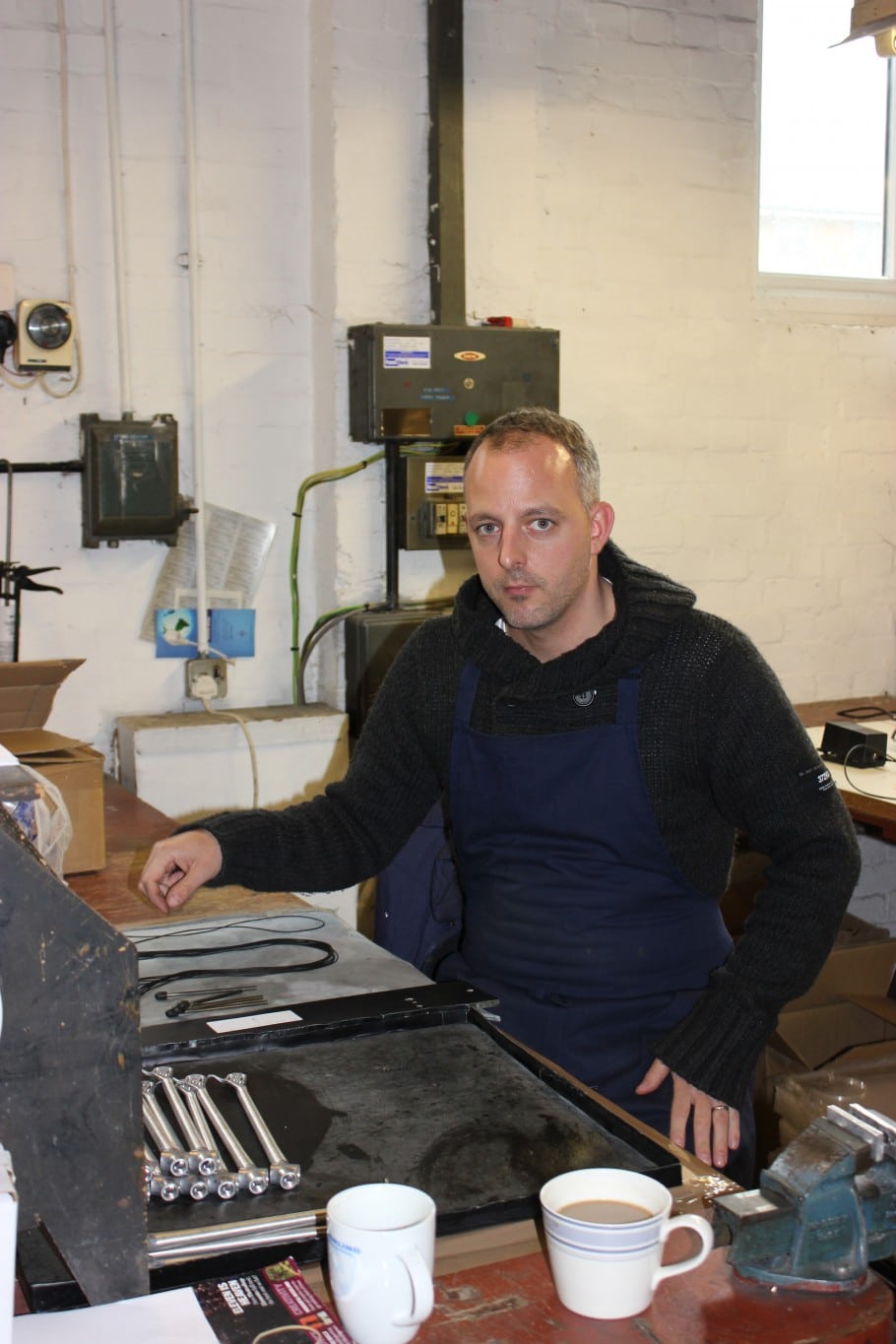
When individual parts arrive in the company, they are assembled for fit and for operational testing and then left to run to make sure that no problems occur during operation. The parts are then disassembled, ready for packing as a kit of parts.
As such, Michell is perceived as a quintessential British manufacturer. Commenting on his refusal to reach out to China, Rowland commented that, “Rightly or wrongly, John wouldn’t have done it that way. And I won’t either.”
Msyday even Rega or Tom evans phono stage. Thanks Paul
How much money do you want to spend on this?
I was thinking probably £400-£900 Paul.
As my jvc amp is top of the range with mm & mc on it will be a good japan phono stage.
So when I upgrade my turntable to michell in a few years a phono stage with mc may be more of a must.
So for my project turntable at the moment I may upgrade to ortofon bronze.
I would look at Trichord Dino for £500 and then, when you upgrade later, you can also upgrade the Trichord in stages to keep pace. More details here: https://theaudiophileman.com/trichord-researchdino-mk-3-phono-stage-upgrades-stay-path/
Hi Paul,
Excellent article and reminded me of when I got my Hydraulic Reference serviced at Boreham Wood (are they still there?) a few years ago. Unfortunately the arm has started to just skim over my records to my horror. Short of blu-tacking a two pence piece to the top of the cartridge like people did in the 80s, I thought about a replacement cartridge. I have tried the obvious adjusting the counterbalance etc. but was wondering if you could recommend a suitable cartridge?
My budget isn’t huge and unless the cusis has dropped by 90% then that’d be a pipe dream for me.
Hi Neil – I assume your stylus is shiny clean? Even a worn stylus shouldn’t be skating unless the tip has been knocked off, there’s a heap of gunge on the tip or your anti-skating has been altered so that it drags the stylus across the grooves. Let me know about that first before I talk about new carts please.
Hi Paul,
Thanks for the quick reply. I’ve just taken some close up photos of the stylus – thank the deities for modern phone cameras! It’s very fluffy despite a wipe with the optional squirrel hair stylus cleaner and a blast with some air duster. Do you recommend anything else to wipe the fluff away with?
My first thoughts are a cotton bud and some alcohol (carb cleaner or brake cleaner are what I’ve got to hand). Jewellery spyglass and tweezers are my other option…but I haven’t got any yet.
Hi Neil – if you’re on a budget, I recommend this cleaner: https://vinylpassion.ecwid.com/VP-Dust-Buster-Stylus-Cleaner-p39645643
You carefully dip the stylus into it and the grime is dragged off and left in the pot, as it where. It’s much safer than using harsh liquids which can loosen the bond between the cantilever and stylus tip.
Hi, I have a J.A Michell Hydraulic Tunrtable and I m searching for some Pieces to repair it.
Can you please take contact with me also per Tel (Switzerland) 0041795094125
Best regards
Laurent
I am nothing but a lowly journalist, Laurent – you need to contact the company itself. I’m sure they will help. Full contacts here: http://www.michell-engineering.co.uk
I have spotted this rather late in the day but I found it very interesting and somewhat nostalgic. I am a long time Michell fan having owned first a Focus one with a Unipivot arm. I wish I still had it but I traded it in for a Gyrodec a year or so after it came out and still have it. It has a similar look to the photo of 001 above with a black opaque base. In those years I met Jon Michell a few times mostly at Hifi shows. A fascinating and very clever man. I have updated my Gyro a bit over the years and have always been looked after by the good people at Michell Engineering, a company run as it should be. I must admit I have stubbornly avoided upgrading the platter from the original aluminium platter as I do not want my Gyro to be like Trigger’s broom with little or nothing left of the original. It’s an old friend now.
Ah yes, “Look after your broom.” Wise words. Glad you’re enjoying your turntable. And thanks for reading, Robin.
Hello to you: here I am already returned in contact with you, there is of that 1 year can be, to see less or more! Indeed I have a turntable bought in 1977, which I like very much (my first steps in the world of the HIFI, for a problem with the engine of my JA Michell model reference electronic. I had even sent the engine, to make repair it at your place, but the parcel remained at the customs during 3 to 4 months, and returned to me. However I do not despair! My step today is to ask you if you have the plans of the whole engine wiring, because I notice that many wires are unsoldered!
In the expectation of your answer, receive my best regards
Hi Stephane – there may be some misunderstanding here. It appears that you believe that I am part of the Michell turntable company. Not so. I’m a mere journalist who reviews HiFi and rambles on about other music ephemera. I would encourage you to contact the company direct. I wish you luck in pursuing your issues. Here’s a link for the company contacts page: https://www.michell-engineering.co.uk/contact-us
Hi Paul, I’m considering a Gyro SE Tecnoarm 2 for my next turntable purchase as I really like it’s design and also the company’s heritage and approach. I believe the Benz Micro Glider cartridge to be a good match for this combo. I have an Icon Audio PS3 MKII phono stage, I believe you know this product very well… Icon Audio spec sheet states gain MC 72db so I assume the Glider SL (as opposed to the SM or SH) is the best option as Benz’s website states suitable for moving coil phono stages above 60db. Does that seem a good choice to you, both in terms of cart and turntable?
Sure Gary – try and grab a home demo though. Make sure your 100% happy before you buy. On a general note, I tend to avoid published cartridge gain specs. I set them by ear. It sounds better 🙂
I set the phono amp so that it’s doing *just* enough and no more. I repeat, *just enough*. That is, too low gain on a phono will sound muffled, lacking detail, little clarity. From that point (and I’d actually start listening tests in that iffy gain zone – set a figure and sound test and repeat as you increase the gain in very small increments), increase slowly until the detail and clarity pops into place.
Then note that figure. Then keep going until the sound sounds bright. Then note that figure. Then back off back down until you hit a sweet spot. I tend to use the lower part of the sweet spot. Exactly where the clarity appears.
This might be a figure under that recommended by the cart manual. The actual sound may be low in volume terms though. This is exactly the point where – I believe – many HiFi users mess up because they, at this point, use the phono amp as a means to produce volume. No. The main amp is there for volume. Don’t use a phono amp to produce louder music. The phono amp is there to properly amplify your cart. Nothing else. If you up the gain on a phono amp to grab volume, the result is a hard-edged, slightly clinical overall sound. Mainly because you’ve over-amplified your cartridge. Use the main amp only for volume purposes.
If I’ve confused you, please shout and I’ll explain in another way.
I’ll be sure to get a home demo before making the final decision. I also want to demo Michell’s Cusis S after reading your post about it. I’ve just adjusted the gain settings on the phono stage…wow what a difference that has made, it’s like the sound has just woken up, clarity is so much better now. I think the gain was set to around a third power previously and is now at a tenth! Thankyou so much, sounds like I’ve just had a free cartridge upgrade.
Glad it worked for you, Gary. Have fun!